In the world of elite athletics, having the best equipment can mean the difference between coming first or second.
For paratriathlete Scott Crowley, who sustained a spinal injury 12 years ago when he was snowboarding in Canada, that means plastic gloves that adequately protect his hands when he races.
But instead of purchasing gloves from a shop or having a sponsor provide them, Crowley relied on making the gloves himself by melting plastic over the kitchen stove.
These gloves were not consistent in size or weight, and they were so inconvenient that they even melted once when he left them in the back of his car.
But 3D-printed gloves developed by the University of Adelaide’s ThincLab 3D Studio mean he no longer has to worry about making them himself.
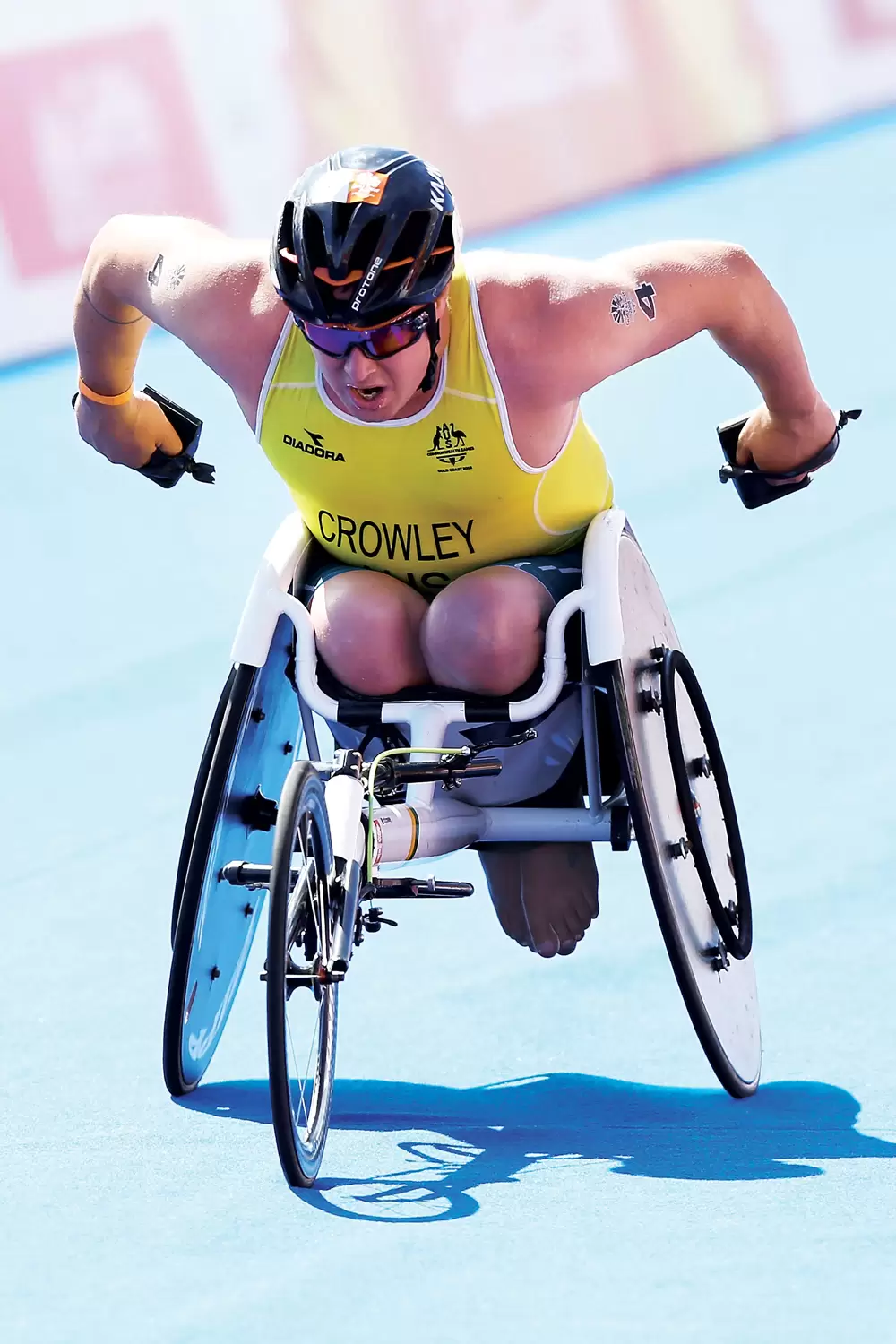
Morgan Hunter, manager at ThincLab 3D Studio, met Crowley through another staff member of ThincLab.
“He was in one day and we were having a chat about 3D printing and he said, ‘Oh, I’ve got these gloves that are made on the kitchen stove and they’re not that great. Could you do something better?’,” Hunter said.
The team took on the challenge, first analysing Crowley’s original gloves and researching other plastic gloves that were on the market to develop some concepts and eventually going through about six or seven iterations.
Major modifications included changes to the design to fit Crowley’s hands better, such as increasing some of the gap between his thumb and the plastic so that it wouldn’t rub on his skin.
“We originally had it quite a neat, snug fit. But after a couple of uses, Scott realised that he needed a bit more movement in it so he could stretch his hands,” Hunter said.
“So we increased some of the clearances, changed the diameter of the handle a bit and eliminated a couple of webs where his fingers were.”
The team also made changes to the shape of the gloves; the original was more of a cone shape where Crowley’s hand fit inside the cone, while the final gloves are a flatter C shape.
Hunter said these changes were made after the team analysed where the wheel hit the glove itself, which included analysing how this changed over the duration of a race.
“On a long race, you might get more fatigue, so your concentration drops a bit. Having a flatter surface means that you won’t miss [hitting the wheel as much as] having a cone shape,” he said.
The finished gloves are a carbon fibre-printed hand piece covered in rubber that fits on to Crowley’s hands like knuckle busters, with his thumb fitting into a slot on the gloves.
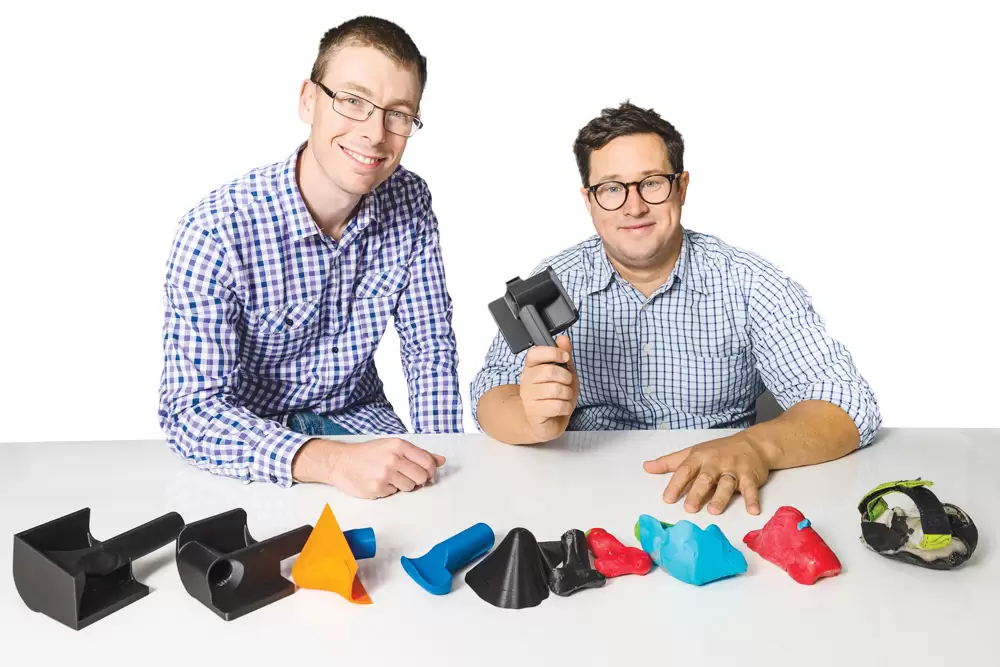
Originally, the team printed the gloves in an ABS plastic because it was the cheapest material for their initial iterations and planned to add additional carbon into the gloves at a later date. However, they eventually decided to use carbon fibre Onyx to give the strength they needed.
“Whilst the ABS was good for initial testing, we could foresee that the tensile strength and the brittleness of the ABS structure wasn’t suitable for a whole race — it would actually start to fatigue and crack — so that’s why we went for the Onyx.”
The only trade-off was the end-cost, which meant about $30 for a pair of ABS gloves compared to about $100 for the Onyx.
Crowley used the gloves at the 2018 Commonwealth Games and ThincLab has now turned its attention to developing a 3D-printed wheelchair for children that can be easily put into cars.
Hunter said while it is still in the concept stage, he foresees some of the challenges will include getting strength into the wheelchair and having a simple enough design that it can be printed on a filament-style printer and packed away easily in a vehicle.
It also needs to allow for interchangeable components to cater for the growth of a child.
“At the moment, people seem to buy a wheelchair that’s too big for them, allow them to grow into it, and then they’re in there for a bit more than what they should be,” Hunter said.
“By having a wheelchair that grows with the user, it will help them use it a bit better.”