As Australia struggles with a national housing crisis, 3D-printed homes have the potential to address the critical demand for affordable and sustainable dwellings, especially in regional Australia and remote communities.
The ability to construct a home using 3D printing is fast going from a novel frontier of engineering to lived reality, where speed, environmental friendliness and cost effectiveness intersect.
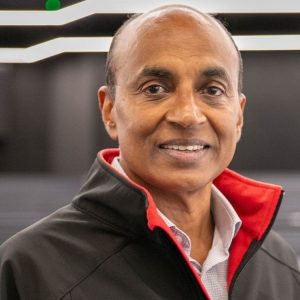
“Technically, we have proven that it’s feasible,” said Professor Jay Sanjayan, Research Centre Director, Sustainable Infrastructure at Swinburne University’s School of Engineering. “We’re now at the stage where we are working on the certification process. Swinburne is currently working with SmartCrete CRC and Standards Australia to produce guidelines, and is testing full-scale 3D-printed walls by Oasis Building Group as part of this process.”
The spectacle of a construction site using large-scale robotic construction – essentially a high-tech crane “printing” the walls of a home, layer by layer, within a matter of days – is becoming a reality in the US, where a number of start-up companies are commercialising the technology.
Engineers such as Sanjayan have set the scene for market disruption; the rest, he told create, is up to these companies to prove it is economically viable.
“We are doing the research and solving the technical challenges, but it is for the companies to work out the commercial part. There is so much interest in the area. All our PhD students who have graduated are in huge demand around the world.”
3D printing of homes is considered a breakthrough not only for the speed of the process, but for producing significantly less waste than traditional construction techniques. The concrete mix can use eco-friendly recycled materials to produce an energy-efficient home.
While it doesn’t replace the need for tradespeople (“You still have to do the kitchen, bathroom, tiles and plumbing, and they take time and money”), removing the costly and time-consuming process of constructing with timber and brick promises its own significant savings.
Its potential in addressing Australia’s housing crisis has been seized upon in NSW, where construction is underway on the state’s first 3D-printed social housing properties. The state government has estimated the innovative construction of two duplexes for Indigenous social housing tenants in Dubbo will reduce costs and cut construction time from around 40 weeks to 16 weeks.
Sanjayan said 3D printing’s potential in social housing lies not only in speedily and efficiently mass-producing homes, but in the ease by which their design can be customised.
“Traditionally with precast concrete you make one design, and then you just mass produce concrete houses. But that particular design becomes a stigma because it’s associated with social housing.
“The benefits of 3D printing are that it provides an opportunity to custom make houses, so each house can be a different shape, a different size, a different number of rooms. You simply plug it into the computer and people can come up with their own design at no extra cost.”
Expansion plans
Developers in Texas have turned to 3D-printing technology to fight their housing shortage with the world’s first 3D-printed housing estate. Called Wolf Ranch, the 100 homes outside Austin start at USD$450,000, which is USD$100,000 below the area’s median.
In other projects at the forefront of 3D printing construction techniques in Australia, Luyten 3D printed the first code-compliant house in the southern hemisphere in 2021. Printed over three days in a Melbourne warehouse, the small home was said to cost less than 70 per cent of traditional building methods.
A one-bedroom concrete home, with a full occupation certificate, was printed in Sydney in two days in 2023.
Declaring itself the world’s first 3D-printed house to be listed for sale, a three-bedroom, two-bathroom house hit the market in Long Island, New York in 2021. The sales pitch zeroed in on the relative affordability compared to other properties in the area.
While 3D printing in construction typically involves concrete, Swinburne is poised to investigate 3D printing earth houses thanks to recently awarded Australian Research Council funding.
The cross-disciplinary project, conducted with industry partner Luyten 3D, aims to explore the potential of 3DP earth as a concrete alternative in 3D construction.
“The automation we’re looking for”
Sanjayan points out that clay doesn’t have concrete’s carbon footprint and is the most abundantly available material on earth.
“You can get it anywhere in the world, and you also avoid transportation costs because you can always source it locally – in fact, on the site itself.”
While some clays are more valuable in a binding capacity, the Swinburne team aims to prove their techniques with low-grade clay.
“Architects love working with clay, and Australians love the look of it. Clay also gives more thermal mass. If we are successful, there will be a lot of interest in this.”
3D printing promises to see construction catch up with other industries such as manufacturing.
“The main problem, when you look at the last 50 years in construction, is that it has remained manual, while manufacturing has become computerised, automated and digital,” Sanjayan said. “When you compare the price of a car 50 years ago and now it’s much cheaper, because they have made it a lot more efficient, whereas in construction the costs are going up and up because it’s not automated.
“We believe 3D printing is the automation we’re looking for. Construction has to catch up, and this is how it will do it.”