Using high-precision 3D-printing technology, a team of researchers at Victoria University is developing detailed replicas of the human airway that could reshape our understanding of respiratory health. This work is being translated into educational settings at the Wyndham Tech School, engaging the next generation in STEM technologies through real-world examples.
Researchers at Victoria University (VU) are breaking new ground in biomedical engineering by developing cutting-edge tools to better understand and treat respiratory conditions.
VU’s researchers are harnessing high-precision 3D-resin-printing technology to create precise replicas of the human airway that allow for more accurate study of airflow dynamics and particle deposition in the human respiratory system, an advancement that presents significant opportunities for environmental and pharmaceutical research.
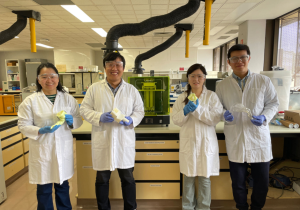
At the forefront of these efforts is a team led by Dr Jingliang Dong, Lecturer, ARC DECRA Fellow and ANFF-VIC Technology Fellow Ambassador at VU.
“The upper airway model we’re creating represents an innovative design compared to the conventional one,” Dong said. “Conventionally, we treat the whole airway as a single piece, and we don’t distinguish the individual sections. But in reality, when people inhale airborne substances or drug aerosols into the airway, some regions of the airway will receive more particles.
“That’s why we develop this model, we need to partition the airway into multiple sections according to their function and anatomical structure.”
The process behind the replicas
“After that, all the sections will be stored into a STL format so the files can be transferred to the high- precision 3D-printing machines. When we finish manufacturing all the pieces, we can assemble it into a single model.”
The 3D-printed airway model is then attached to a lung simulator.
“The lung simulator creates the physiological flow of inhalation and exhalation so that we can reproduce that airflow within every model. Then we release the particles into the model, constantly
subject to the physiological airflow.”
Using HPLC, researchers can determine the exact dosage of particles that have settled in that region.
The data allows researchers to assess the inhalation toxicity of airborne pollutants and the effectiveness of drug aerosols more accurately. Access to these detailed insights could have far reaching implications in medicine, particularly for ear, nose and throat (ENT) doctors.
“[At the lab], postgraduate students are given patient-specific images,” he said. ”Then, based on the image, we construct the models. So, they learn how to distinguish the airway and the anatomy from the surrounding tissues.
“As the biomechanical engineering field increasingly relies on AI for simulations and analysis, it is imperative that students are equipped with skills like this.
“We are on the right track to recreate all the airflow and arterial blood flow in a digital environment. The research efforts happening at VU will empower our students to be ready for the next era, where everything can be optimised or run by artificial intelligence.”
Empowering the next generation in STEM at Wyndham Tech School
This STEM Centre of Excellence, located on the VU Werribee Campus, provides secondary school students with hands-on experience with advanced technology, including resin 3D printers and laser-sintering 3D printers.
“We have 16,000 high school kids engaged in programs here each year, focused on solving real-world problems using industry standard technologies and methodologies,” Sam Nikolsky, Director at Wyndham Tech School, said.
“We’ve got students in high school using the exact same tools and the exact same processes that researchers at the forefront of biomedical engineering are using, and we’re bringing that into the classroom.”
Students develop skills in future-focused techniques such as computer-aided design, computational fluid dynamics and 3D printing.
“We work really closely with VU researchers and industry, from big companies all the way through to local startups, to understand what problems they’re working on solving; what the pathways are into their careers; what the tools, technologies and methodologies are that they’re using; and then we build the curriculum and learning programs around that,” Nikolsky said.
The school partners with 40 secondary schools across Melbourne to offer students specialised programs centred around high-tech, industry-relevant learning experiences.
“The real world is interdisciplinary,” Nikolsky said. “[At Wyndham Tech School], students can start to specialise and find things that might be a strength or a passion.