Timber may be one of the oldest and most common building materials, but innovations like these are transforming its role in the future of construction.
Here are four Australian projects designed to make the most of plantations and stretch our wood resources further.
1. Reimagining densified wood
Wood densification via various compression methods improves the strength and enhances the fire resistance of low-density wood.
Resistant to indentation, scratching and abrasion, densified wood is the perfect material for parquet flooring or surfaces such as benchtops.
Chemicals are typically impregnated into wood to achieve densification, but this process carries the risk of a springback effect, said Paolo Lavisci, Program Development Manager, Mid-rise Construction at WoodSolutions.
“Wood is neutral to temperature changes but sensitive to seasonal moisture variations,” he said.
Improving the mechanical properties of low-density wood might be a sustainable practice, but chemical pre-treatment also has its own impact in terms of energy and pollution.
Enter timber technology company 3RT, which is aiming to replace old growth hardwood with fast-growing plantation hardwood timber that can be produced from peeled veneer like plywood.
3RT created a digital production unit that transforms plantation and forest residues into blocks that perform like mature hardwood within one day.
The patented process uses water-based nanoglue combined with progressive compression controlled by algorithms, said Lavisci.
“It doesn’t require a lot of energy or chemicals to penetrate the wood cell wall, and allows densification to be achieved in a controlled manner,” he said.
“The process results in the production of ‘square logs’, very similar to natural logs, and without the round shape which creates a yield problem.”
The rectangular shape produced by the 3RT unit makes further processing easier, with the drying, splitting and variability of hardwood logs also limited.
“It’s a much more controlled process that starts from low-value plantation hardwood and increases the value of this timber to match or even exceed that of the old growth,” said Lavisci.
The resulting product is suitable for both decorative and structural applications, with the potential to replace steel and aluminium as a more sustainable building material.
“We’ve also started [experimenting with] softwood veneers, but it’s early days,” he said.
2. Composite reinforced timber
Wood-based load-bearing structures consisting of laminated mass timber columns, walls, and floors are often constrained by serviceability or fire performance.
But adding a small proportion of Fibre Reinforced Polymer (FRP) to timber can significantly boost performance, said Dr Cristian Maluk from The University of Queensland (UQ) School of Civil Engineering.
Through the Australian Research Council (ARC) Future Timber Hub, he worked to develop these hybrid Timber-FRP prototypes in partnership with the Queensland Government of Agriculture and Fisheries and manufacturer Hyne Timber.
The composite reinforced timber design is focused on developing improved mass timber products and systems, including glue-laminated timber (GLT) and cross-laminated timber (CLT).
With a new class of tall construction in Australia using timber products, including Brisbane’s 25 King Street, the largest commercial timber office building in the southern hemisphere made out of GLT and CLT, Maluk said it’s crucial to extend our resources as far as they can go.
By stiffening the timber, the FRP infusion not only reduces the required product size, but also increases deflection and vibration structural performance.
“Like-for-like, you can use less timber overall by just having 1 to 2 per cent [of FRP] within the cross section,” said Maluk.
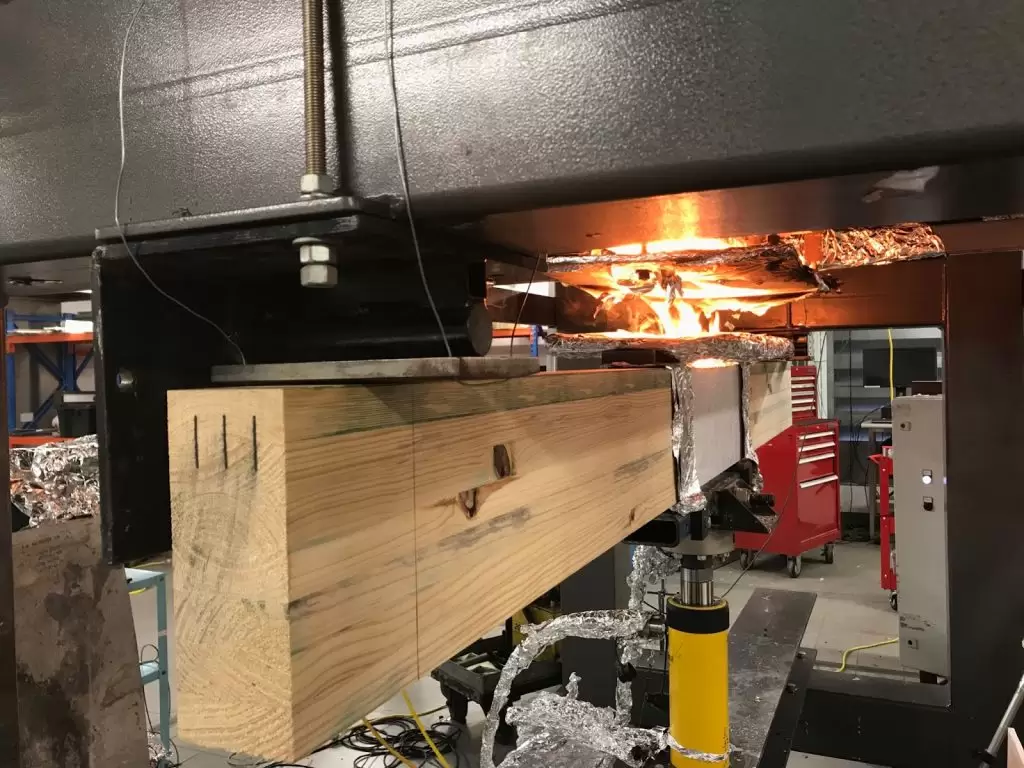
“As the FRP is embedded inside the laminated timber in the manufacturing [process], the timber cover will protect the FRP during a fire, which is typically considered to be sensitive (when left unprotected) to the elevated temperatures of a fire.”
The prototype designs are in full-scale lab-based testing but are yet to be used in commercial construction. The Hub’s designer, manufacturer, and building partners are supporting its development towards commercial pilot implementation.
“We’re currently doing a series of design studies to translate the improved product performance to a building system performance,” said Maluk.
“From there we’re hoping to do a small commercial building implementation if we can find the right case study for it.”
3. Hybrid FRP-timber thin-walled sections
Much of our built environment is made up of steel in the form of thin-walled sections, said Associate Professor Joe Gattas, also from the UQ School of Civil Engineering and the ARC Future Timber Hub.
Traditionally, timber isn’t used as a profiled thin-walled product, due to the high natural variability and defects within the material, as well as the difficulty in connecting thin-walled timber materials together.
Thin wood materials, such as veneers, might have good mechanical behaviours, but they primarily run along the grain direction.
By fusing timber veneers and FRP, however, you can control which direction the material runs, boosting bidirectional performance attributes.
“You’ve got very good uniaxial strength and stiffness of the timber, but relatively weak properties in the cross-grain axis and strength-reducing natural features,” said Gattas.
“So we place a very thin layer of FRP, perpendicular or inclined to the timber grain direction, to improve cross-grain performance and reduce the localised influence of any natural defects.”
As FRP can be applied to complex forms, this can be used to create a thin-walled section with a similar weight-specific mechanical performance to thin-walled steel products, including beams and columns.
Sustainably speaking, this means wood materials traditionally viewed as non-structural byproducts, such as low-grade veneer and plywood, forest thinnings, or agricultural fibre, could be processed into high-performance engineered wood products.
“If you can turn wood fibre into a construction resource, you can continue to store its carbon for 25 to 50 years, if not longer,” said Gattas.
While the technology is still in the early stages of development, the Hub has strong proof of concepts, and is working on securing commercial partners for the next stage.
“We’re hoping to test a structural assembly and [construct] a small building within two to three years,” he said.
4. Plantation hardwood cross-laminated timber
The lowest carbon route to construct a building often doesn’t involve significant material modification, said Associate Professor Jon Shanks, Director of TimberED Services and Associate Professor in Timber Engineering at the University of Tasmania.
“The best innovation might be a slightly different way to put a timber frame together, meaning you can use more of the resource that’s already there,” he said.
Putting “knotty” and sloping grain timber into engineered wood products like the aforementioned CLT is another solution, said Shanks.
CLT, produced by sawn, glued, and layered wood, can serve as a substitute for a concrete slab, concrete wall or even a roof, said Dr Assaad Taoum, a Senior Lecturer in Civil/Structural Engineering at UTAS.
The product can be manufactured, pre-drilled and prepared for construction offsite, then put together onsite requiring minimal labour.
The new Atlassian Sydney headquarters, set for completion in 2025, will be the tallest hybrid timber structure in the world, with internal floors made almost entirely of CLT.
While Shanks said CLT producers in Australia are predominantly making the product from plantation pine products, Tasmanian company CUSP is the first in the world to produce the material from Eucalyptus nitens, a hardwood commonly known as Shining Gum.
The innovation was identified through research conducted by the UTAS School of Engineering and School of Architecture and Design through the Centre for Sustainable Architecture with Wood, which found a way to repurpose a Shining Gum plantation originally designated for pulp and paper production when planted 20 years earlier.
While the wood was not intended for the production of structural products, the UTAS team, using responsibly sourced wood, produced reliable structural products, including CLT, from this plantation.
“Now we can replicate what we’ve done with the Shining Gum for hardwood species in other states [designated] for chips or low-end products,” he said.
The research focused on working with the existing material to minimise the amount of energy, time and money spent on modifying the product, so it can be used as close as possible to the way it was harvested, said Taoum.
“You’re acknowledging your material is variable and full of character; you’re homogenising it by layering it next to other bits of wood that have similar variability in different places. So, you’re averaging out the impact while also sequestering a whole heap of carbon at the same time,” added Shanks.
Learn more about the next big strides being made in materials engineering at Engineers Australia’s Climate Smart Engineering conference, including recycled concrete and transforming CO2 emissions into building materials. You can view the full program here.