Software engineer Vikas Sathaye is still reeling after receiving an award at the Oscars this year for a camera mount that gets viewers closer to the action.
Engineers are not averse to awards. You put on your best suit, join your colleagues for a meal and say a few well chosen words when your name is called out. But it’s not usually on the same scale as a Hollywood ceremony as one Australian engineer discovered earlier this year.
“It was a unique experience,” said Vikas Sathaye, a software engineer at RF Industries in Adelaide.
“It was a red carpet welcome and photo shoot. It was really fascinating. We had never experienced something like that before.”
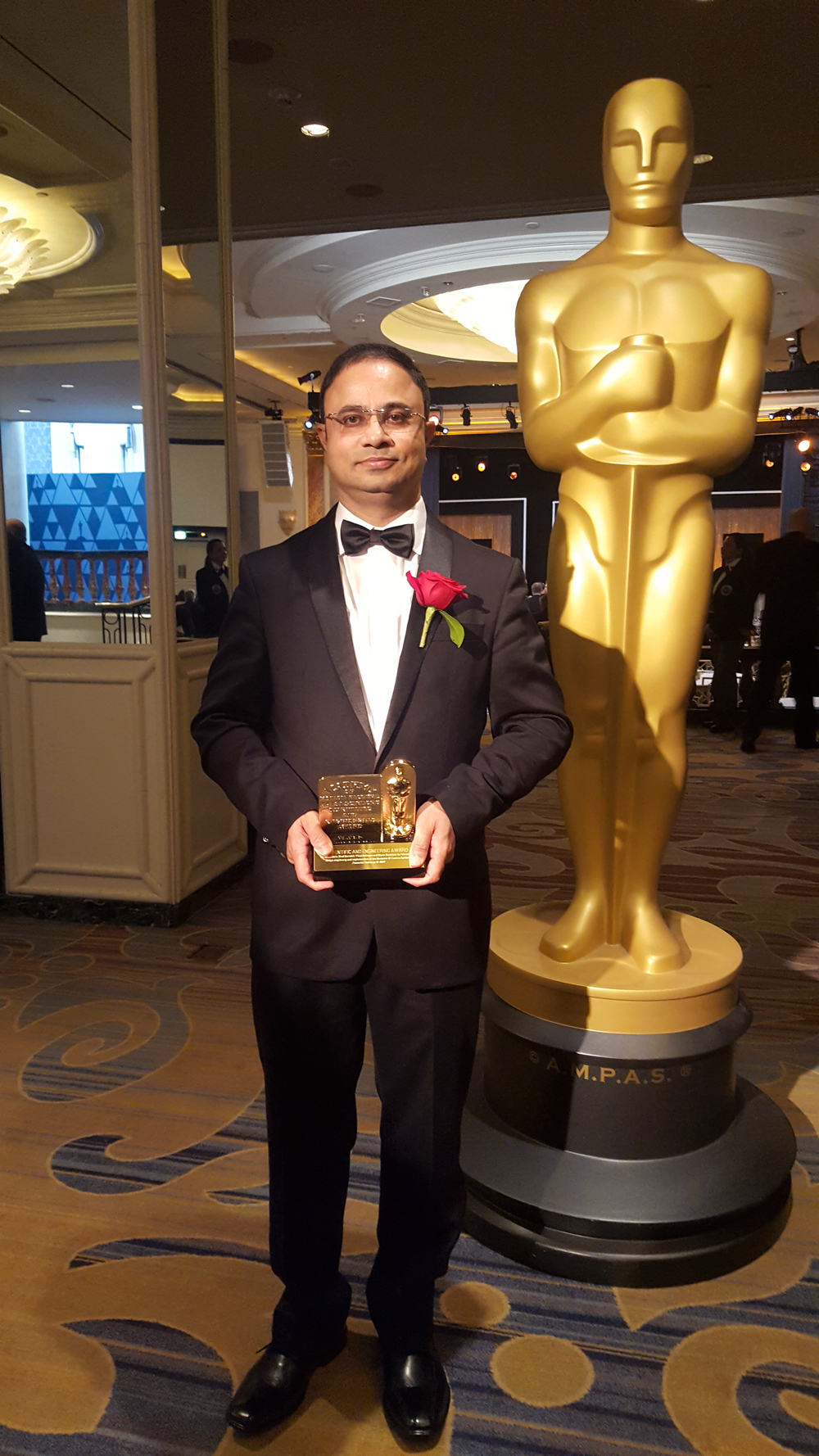
Sathaye received a scientific and engineering award from the Academy of Motion Picture Arts and Sciences, or as they’re better known, the Oscars.
The award, which was shared with New Zealand-based colleagues John Coyle, Brad Hurndell and Shane Buckham, was for the development of the Shotover K1 Camera System. This system has been used on more than 100 films from The Hobbit to Guardians of the Galaxy and Dunkirk.
The award citation said: “This innovative six-axis stabilised aerial camera mount, with its enhanced ability to frame shots while looking straight down, enables greater creative freedom while allowing pilots to fly more effectively and safely.”
Sathaye, who was born and raised in India, moved to New Zealand in 2002 and was working in the field of embedded software with Buckham, who told him about the job going in Queenstown with Shotover, a new company being set up by Coyle.
He was looking to create two gimbals that could be attached to helicopters for smooth jitter-free aerial filming. The first would be for standard 2D movies while the second would feature twin cameras for shooting 3D movies. And while gimbals traditionally used analogue control systems, theirs would be digital.
“As a software and control system engineer my primary job was to stabilise the camera platform and move the gimbal head in the desired direction based on the joystick commands issued by the camera operator,” Sathaye said.
“Besides this I was responsible for driving the servo-lens system and to display all the camera and gimbal-related parameters as overlay on the LCD monitor.”
In the movies
They started trying to stabilise a single axis version to work out the principles involved then expanded that learning to six axes. Working out how to stabilise the single axis took a year of research and development while the six-axis version took another year after that.
“In those early days, we tested it on a truck because the helicopter was too expensive,” Sathaye said.
“We used to tie it on the back of a truck and then go on a rough ride to see how the gimbal performed, then go back to the office and check on the big screen to see if the image is stable and nice.”
By 2011, the 2D gimbal was ready to be tried on a helicopter ride performing exactly as they hoped. It was so successful that the filmmakers working around Queenstown heard about it before it was fully finished and started asking to hire it. In fact it became so popular, the Shotover crew had to turn their attention to developing the 3D version because the 2D prototype was out all the time.
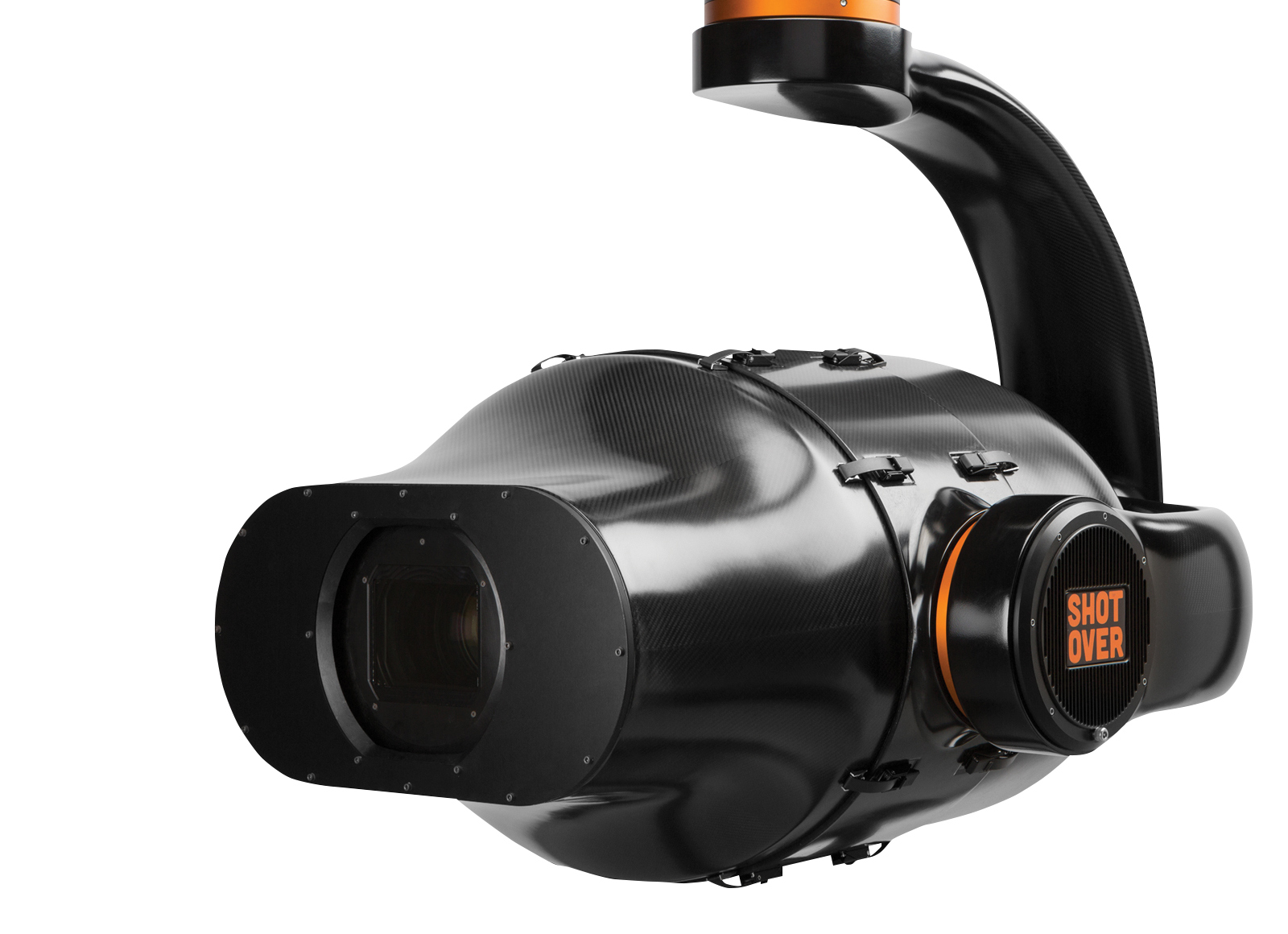
“The first challenge with 3D was that the weight was going to increase too much with a second camera in there as well so we had to work out how to make it fit in the same compact size without increasing the weight,” he said.
“So we made a choice of going to carbon fibre but, because it was a little bit flexible, it affected the stabilisation so we had to tweak the software to fix that, which meant it was 2012 before we got the final 3D prototype working.”
One of the first movies to use the new system was Walking with Dinosaurs, and because it was still at the prototype stage, Sathaye and his colleagues went on set to teach the crew how to use it and help deal with any problems as they came up.
“It was really fun working with them,” he said.
“In fact, my name and Brad’s name appeared in the credits so we were really thrilled.”
He feels his biggest contribution to the design of the project was pushing for a distributed control system rather than a single CPU. This allowed them to work on it in a more modular way and made the finished product easier to disassemble and reassemble. However, the most challenging aspect was the synchronisation.
“There are six axes in the gimbal: three inner axes that stabilise the gimbal so the camera stays still, and three outer axes that take the force moment for the gimbal,” he said.
“So a person sitting in a helicopter uses a joystick to turn the gimbal in the direction they want, but then the coordination between the inner axis and outer axis was very challenging, getting the exact motion the way the camera operator wants it to. That involved a lot of mathematics, so software was very crucial.”
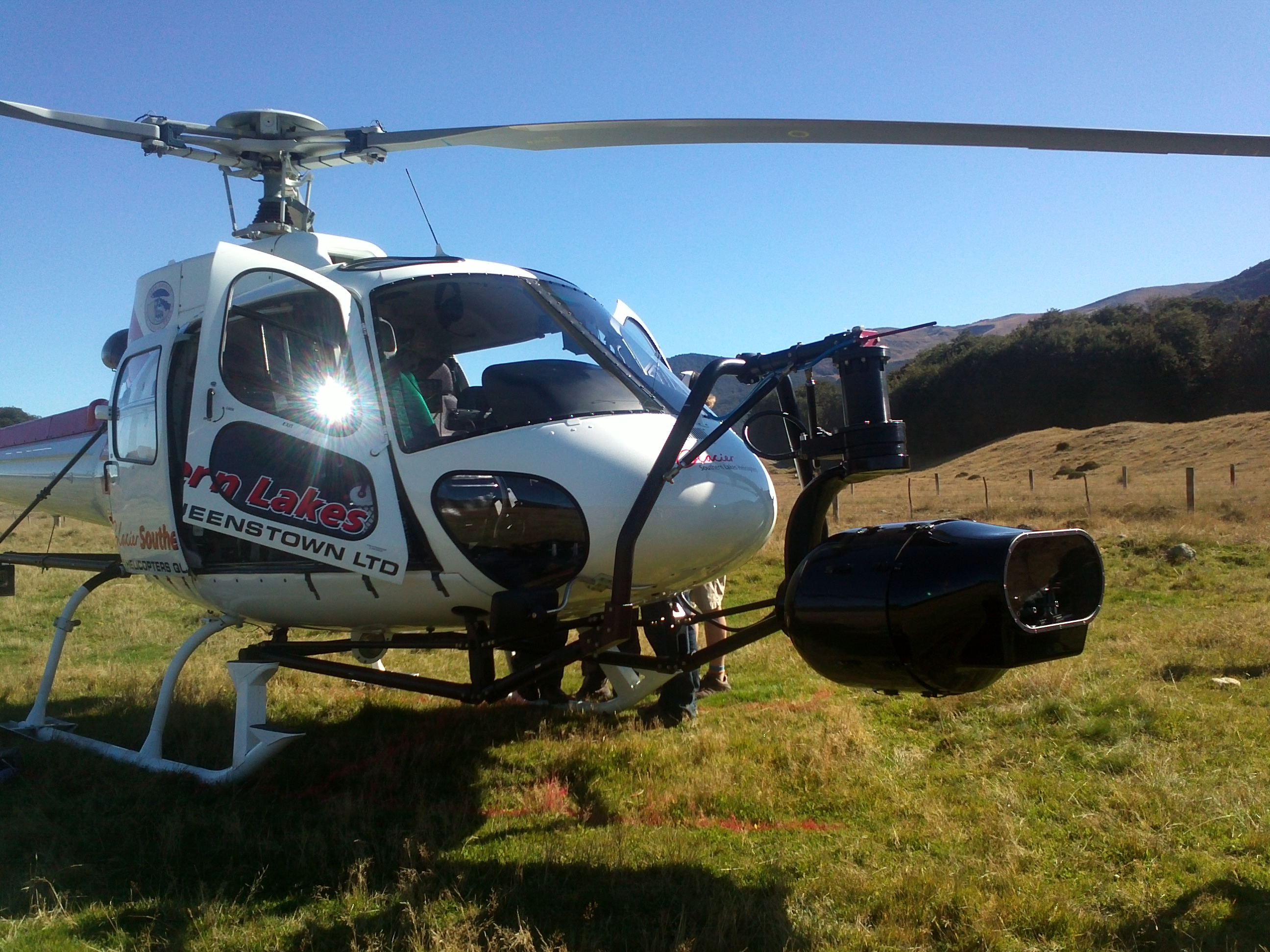
Expanding out
An unexpected benefit of the project was his daughter being impressed by all these elements of her father’s job, going on film sets and riding in helicopter – so much so that she is now studying engineering at the University of Adelaide.
The family relocated to Adelaide in 2012, and Sathaye now works at RF Industries developing firmware and graphical user interfaces for radio equipment being used for the public safety network. He might yet look for further work in the movie industry, as he said he was very interested in some of the things other engineers and inventors were working on when he went to the Oscars ceremony. But he’s also playing around with his own ideas.
“I love cooking and want to bring some of this automation into the food industry as well,” he said.
“So at the moment I am just trying to see if I can do something where I can do frying with minimum oil or some sort of automation where, if you want to make fried rice, you just press a button on the front of a microwave kind of an instrument and it will do it for you.”