University of Queensland researchers have developed a super-thin cathode coating that can significantly extend the life span of high-voltage lithium-ion batteries.
Much of modern life runs thanks to rechargeable lithium-ion batteries — they’re in our smartphones, laptops, electric vehicles, and are important for renewable energy storage.
But they still have limitations. Depending on their chemistry, li-ion batteries can have safety issues, and they can feature cobalt, a costly and toxic material, which has been used for decades.
A team of nanotech researchers led by the University of Queensland (UQ) recently published work that describes a new super-thin protective coating, which can potentially solve some big li-ion battery issues.
Published in Nature Communications, the research outlines how this layer can “more than double” the life span of high-voltage li-ion batteries to more than 1000 charge/discharge cycles, up from a typical average of several hundred.
Senior author Professor Lianzhou Wang of UQ’s Australian Institute for Bioengineering and Nanotechnology and School of Chemical Engineering, said the team chose to focus on improving the cathode, the positive side of the battery.
“If you look at a battery, there are two key components: a cathode and an anode, and in between there’s a membrane and also there are some electrolytes,” Wang told create.
“The cathode is about 40% of all the costs in the battery system — and it’s also the bottleneck,” he said.
“If you look at the current state-of-the-art cathode material in commercial products, the specific capacity that cathode can deliver is about 150 to 200 milliampere hour per gram (mA h g), but the very common anode materials — like graphite, for example — can deliver more than 300 to 370 mA h g,” he said.
“So, one side’s capacity is much higher than the other side.”
The UQ team set about developing a unique cathode layer that could withstand corrosion and boost battery life span.

Atomic-thin crystal coating
There are alternatives like nickel and manganese, but these can have problems with stability; over time, the nickel and manganese can dissolve into the electrolyte and damage the battery system.
Working with a lithium, nickel and manganese-based cathode material, Wang and his team developed a coating using a technique called epitaxy. This works by growing a layer of crystal just one-atom thick, made of lanthanum, nickel, manganese, and oxygen, onto the cathode particles.
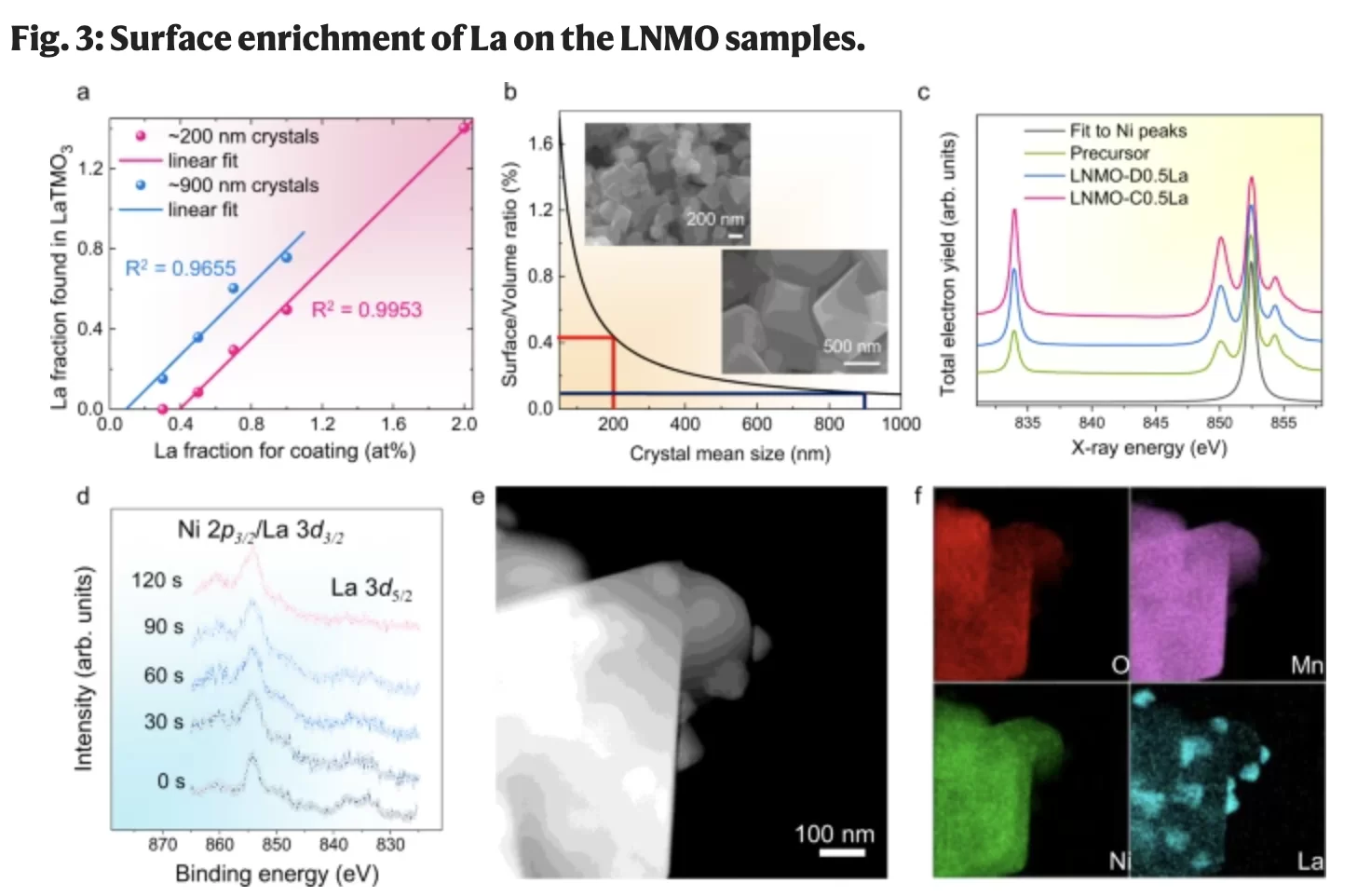
This protective layer enables a high-voltage battery — about 4.5V — and helps reduce cathode corrosion.
“This is the key innovation of work, with this mono-layer protection, the dissolution of the nickel and manganese become more difficult,” Wang said.
In a testing facility, the team ran batteries for a few months at a time to monitor performance and determined a capacity retention of about 77% after 1000 cycles when tested in combination with a graphitic carbon anode and a non-aqueous electrolyte solution.
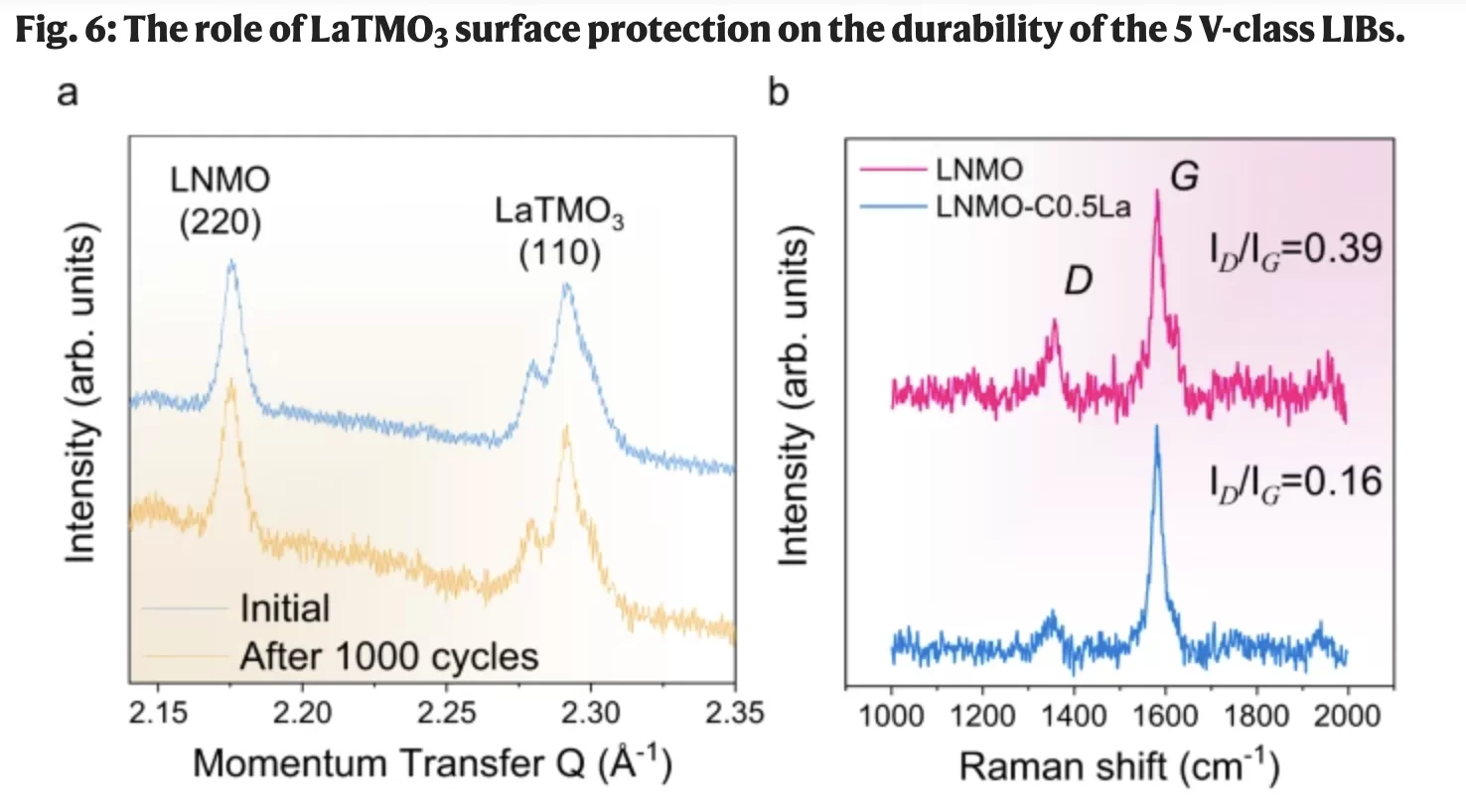
Scaling up and commercialising
Wang said the protective material could be commercialised within two to three years – but there is still work to do. The next step is to scale up – moving from testing batteries the size of a coin to medium and larger-scale – in partnership with industry and the CSIRO.
A recently launched $242.7 million federal government program, Trailblazer, is hoping to accelerate the commercialisation of research such as this.
It was announced in April that Curtin University will lead the Resources and Critical Minerals stream of the program, in partnership with UQ and James Cook University.
Rohan McDougall, Director of Commercialisation at Curtin, told create 33 industry partners are on board.
“They range from companies that are looking at how to process and value-add to minerals, [such as] Linus, who are looking at collaborating on optimisation of processing rare earths in Australia and their processing facilities internationally,” he said.
“There are others that are looking at products ranging from processing of lithium, improving efficiency and extraction and processing of elements like nickel and cobalt, and then even looking at production of cathodes and anodes and battery cells.”
Wang said UQ is also partnering with industry as part of Trailblazer to improve battery materials.
McDougall said one aspect of Curtin’s Trailblazer approach will involve incentivising academics to work more closely with industry — such as via promotional schemes or revenue-sharing initiatives — to “make sure that they can share an upside if there’s any benefit that results from practical implementation of technology developed in those areas”.
Another aspect will include “working with industry on delivery of course content to give a more applied experience for students, so they understand what the career pathway looks like and can move more seamlessly into those career pathways”.
While the program will provide a significant financial boost to commercialisation efforts, McDougall said people power is also required.
“We certainly have high hopes that it will provide the resources that we need but one of the challenges we’re going to have will be recruitment of skilled people that are needed to provide a flow through of people from the university into industry,” he said.
He suggested people who are interested in the program should “get in touch with us, because we’re going to be looking for people”.