A team from UNSW Sydney’s Graduate School of Biomedical Engineering, and Tyree Foundation Institute of Health Engineering (Tyree iHealthE), led by Dr Thanh Nho Do, has created a smart textile that can move like a robot.
Using a new class of soft hydraulic artificial muscle that can be extended and contracted under applied hydraulic pressures, the team has created a textile that can respond to commands. These muscles, which are as little as 1 mm in diameter, are integrated into the material itself, creating an active fabric that can be used in a range of applications.
The soft muscle consists of an inner silicone tube inserted into an outer helical coil, which acts as a constraining layer. Without this constraint, the silicone muscle would simply expand like a balloon – by adding the constricting layer, expansion can be limited to axial elongation.
By applying hydraulic pressure into the inner channel of the silicone tube, Do and his team can program a wide range of motion.
“A unique feature of our textiles is that we can tune their generated motion or force,” says Do. “We do this by varying the stretch ratio of the inner silicone tube within the soft artificial muscle fibres at the time they are fabricated, which provide high flexibility for use in specific applications.”
“We can turn any passive textile or fabric into an active one by directly embedding our soft artificial muscles into its structure,” he says.
Building on ancient technology
“Textiles are one of humankind’s oldest technologies,” says Do. “They have amazing mechanical characteristics, including flexibility, conformability, stretchability, and breathability, making them extremely popular in every aspect of human life.”
Do saw room for improvement: “In contrast to passive textiles, smart textiles use active yarns or stimuli-responsive fibres in traditional textile-making techniques, such as braiding, knitting, and weaving,” he explains.
“Depending on their composition, these active yarns can induce shape-change when triggered by electrical, thermal, or pressure inputs, resulting in textile deformation. In this approach, the shape-change of smart textiles happens at the interior level, rather than the exterior level as happens when integrating conventional passive textiles into robotic systems.”
Smart textiles, smart clothing
These smart textiles have potential use for many applications ranging from compression garments for athletes, wearable assistive devices for rehabilitation and human augmentation, wearable haptics, and even fashion.
Do has even suggested that there is potential to use soft assistive robots to treat failing hearts.
Smart compression garments
Athletes also use compression garments to recover at a faster rate and reduce muscle soreness after training. Compression devices made from smart textiles could be low-profile, easy to apply, and more user-friendly for patients.
“Smart garments could also be developed for patients suffering from poor circulation; active textiles could selectively apply pressure to veins to assist blood transport back to the heart,” says Do.
Augmenting human performance
Do suggests that his smart textiles can be also used to develop soft exoskeletons, which could enable people with disabilities to walk again.
“Despite enormous and impressive advances, existing technologies in this field are mostly associated with rigid robotic suits,” he says.
“It is our hope that we can create lightweight and soft exoskeletons similar to leggings or tights that can be worn as normal clothes. This kind of exoskeleton could make it easier for older people, and those with impaired mobility, to walk.”
“Right now, we can induce smooth bending motion in a textile sheet that can enclose and then grow along the human finger,” continues Do. “Such technology, one day, could be used to develop smart wearable suits that can automatically adapt to the wearer, similar to an ‘Iron Man suit’.”
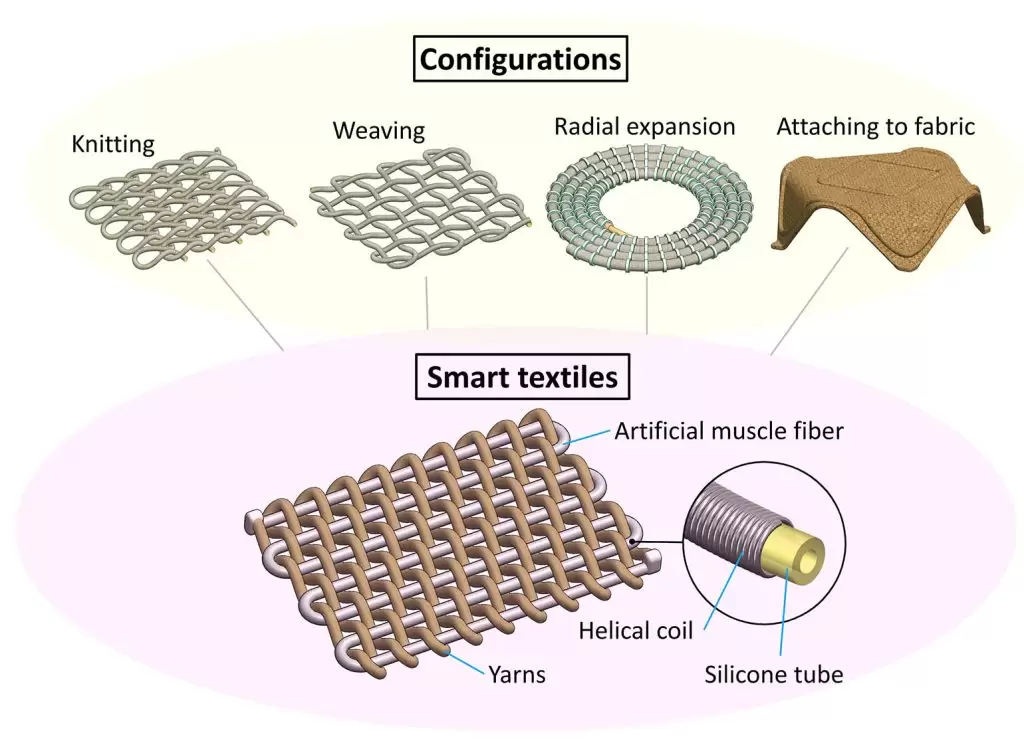
Smart textiles in industry
By using specific patterns of braiding and weaving, Do says that textile sheets can be programmed to produce multimodal motion, such as radial expansion, for optical lenses, haptics, or smart window blinds.
“We can directly embed the soft artificial muscles into any planar structure or passive fabrics to create shape-shifting robots and structures that can perform useful tasks,” he says.
“These structures and robots can be implemented as a lifting mechanism, or legs for robots. Soft robots are needed in various contexts, including rescue missions from bushfires, collapsed buildings, or hazardous environments.”
Do’s team has already been able to create soft robots capable of lifting objects around 346 times the material’s own weight.
Inspired by nature
“In nature as well as engineering applications, we can often find soft cylindrical and tubular shapes such as the oesophagus, colon, blood vessels, or the tube feet of the starfish,” says Do. “Our braided structure could be used to create bio-inspired soft tubular structures, such as medical stents or even artificial organs.”
“We are developing a new soft robotic skin using our smart textile to provide support for failing hearts,” continues Do. “Most existing approaches in this field use mechanical pumps that directly contact the patient’s blood, which can cause infection and other complications. Our approach is to wrap our robotic skin outside the heart surface and then control contraction to augment the heart pumping blood.”
The future of soft robotics
Do and his team are currently working on a prototype “soft syringe” that would allow them to integrate a pump into the design. Paired with wireless control, this would enable them to create an untethered system. This new technology will be available next year.
There are other developments on the cards too.
“We could use our technology to replace conventional cable mechanisms in existing surgical robots or medical devices,” says Do. “Or we can integrate our smart textiles into existing robots to provide real-time haptic sensations or smart compression garments to enhance blood circulation for massage therapy.”
“We can also use our technology as the main actuation source for 3D robots, such as a bio-inspired soft manta ray or octopus, where no skeleton would be needed.”
Do and his research team have published their latest findings in Scientific Reports and Soft Robotics journals.
For more of the latest engineering news sign up to create’s weekly newsletter.
Engineers of all areas never cease to amaze me. I am a simple retired civil engineer and am enthralled and excited by the skills of our new generations