Cladding is a carbon-intensive material that has long been plagued by safety issues. By using recycled glass, a team of Australian-based researchers is aiming to introduce a sustainable and fireproof cladding material to the global market.
Every year, thousands of tonnes of glass are needlessly sent to landfills.
But this highly recyclable material could be put to better use, thought a team of RMIT University engineers.
Not only was the team aiming to create a circular-economy solution to address a major waste stream, they also sought to address issues with a problematic building material in the process.
Led by Associate Professor Dilan Robert, their idea to use recovered glass waste to produce a composite cladding alternative has since led to the production of a cost-effective, sustainable and fireproof material.
Multiple sustainability benefits
Aside from reuse, there are several sustainability benefits of using recycled materials in cladding.
Traditional cladding products use large amounts of natural materials such as aggregates, says Robert. But with construction in Australia continuing to boom, the local extractive industry produces more than 130 million tonnes of aggregates annually, which is expected to increase to 210 million tonnes by 2050.
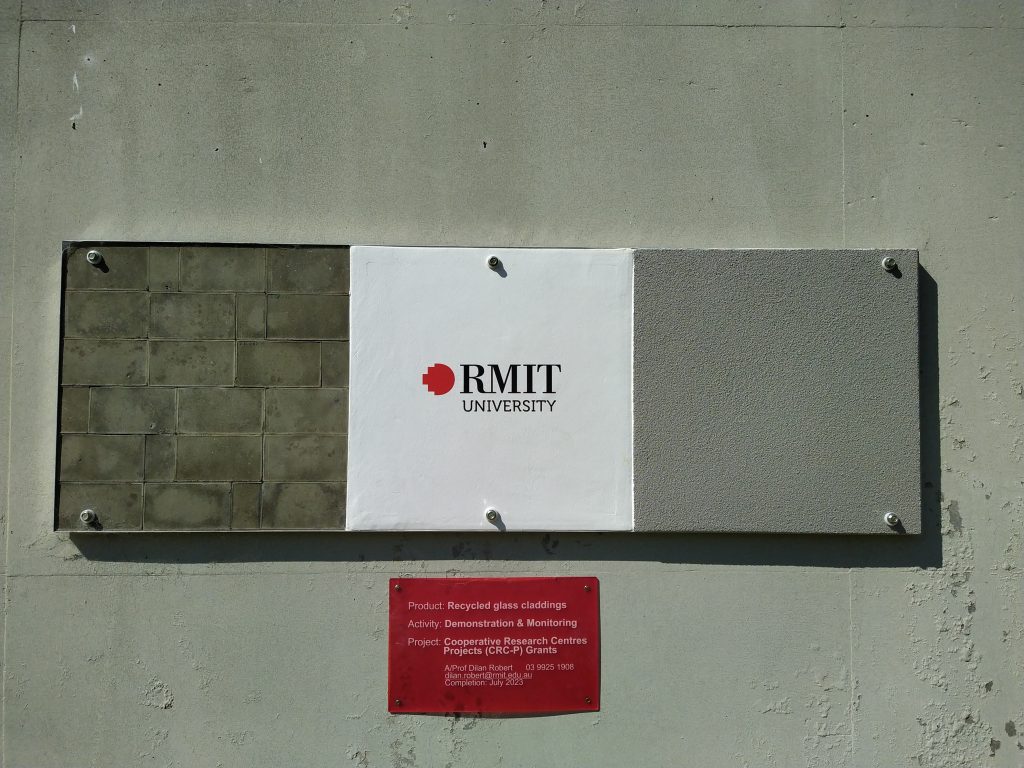
“It is not sustainable to keep using natural materials in construction,” says Robert. “Our product uses 83% recycled glass waste, 0% natural materials, and relatively low amounts of binders, which can therefore reduce the burden of extracting aggregates.”
Reducing emissions in the construction sector was another key driver for the team, with the industry currently responsible for 18% of Australia’s carbon footprint.
In the race to achieve net-zero emissions by 2050, the sector needs to come up with innovative ways to approach commercial practices that divert towards more sustainable methods, including replacing materials that are carbon intensive to produce, such as cement-based cladding.“Our product doesn’t contain any carbon-based additives or cement in the mix design,” says Robert. “This significantly reduces the carbon footprint of construction.”
The method also requires less carbon-intensive manufacturing conditions.
“For example, producing bricks requires a furnace with a temperature set at over 1000 degrees Celsius,” says Robert. “But our manufacturing method requires much less energy to produce the product.”
To determine just how energy-efficient the manufacturing method is, the project was recently expanded and extended to assess its environmental impact.
“We are now aiming to compute how much energy can be saved from this method,” he adds.
Fire-safety properties
In the last 25 years, there has been a substantial increase in building-fire incidents globally, says Robert, with most cases linked to the use of flammable cladding materials.
“If you analyse the statistical data of building fire incidents around the world in the last three decades, the severity has substantially increased due to the introduction of lightweight cladding materials in modern buildings incorporating flammable components,” he says.
You only have to look at the Grenfell Towers fire in 2017 to see the devastating impacts of poor fire-prevention performance of cladding materials, with the incident claiming 72 lives and injuring almost as many.
These tragic events highlight the importance of designing fire-resistant cladding materials and systems for the construction sector, said Robert.
“Claddings play a key role in preventing the spread of fire, particularly in high-rise buildings,” said Robert. “Building fires can happen anywhere at any time and cannot be predicted. Therefore, fire-safety requirements should be embedded in the design of buildings.”
As a risk mitigation strategy, stringent fire-resistance requirements have been mandated in building standards, including the rigorous requirement for non-combustibility (AS1530.1) set by Standards Australia.
However, this imposes significant challenges for research scientists looking to introduce new cladding materials to the market – including the RMIT team.
While glass has a high self-ignition point, maintaining the status quo when adding binders proved to be a challenge.
“We use certain types of binders and right-mix proportions in combination with recycled glass, along with an optimum manufacturing condition, to achieve a non-combustible product,” says Robert.
Robert said their special blend of materials and manufacturing conditions also overcame challenges to “improve the toughness” of glass claddings, which can be brittle and prone to fracture.
“Experiments have proven that our claddings are fire-safe, water-resistant, cheap, and meet structural and environmentally sustainable requirements,” adds Robert.
Upscaling the technology
To test the technology’s feasibility and serviceability as building claddings, the glass panels were installed at an external wall of RMIT’s Bundoora campus in December 2022.
“We are monitoring several different scenarios of the product at the moment,” says Robert.
“Our demonstration includes raw panels that do not have any rendering, as well as rendered panels with paint.
“We will continue to monitor them in the future to assess the behaviour under adverse weather conditions such as wind, rainfall, and temperature variations.”
The team is now working towards upscaling the manufacturing process to support the commercialisation of this novel recycled glass cladding, in collaboration with their industry partner, materials technology company Livefield.
“Through this process, we hope to increase the production efficiency of claddings in a commercial environment by fine tuning the mix and the manufacturing process,” says Robert.
The plan is to commercialise the product within the next two years, with further support from the government, RMIT and Livefield.
The team has also been backed by the Australian Research Council Industrial Transformation Research Hub TREMS to explore new ways of creating high-value materials from recycled waste for practical application, including composite panel science.
“Our technology has great versatility, so we hope to apply it to other areas in the near future,” says Robert.
[embedyt] https://www.youtube.com/watch?v=vNg8qNbbz6k[/embedyt]