A solution to a pressing environmental problem has been found by researchers who were looking for something quite different.
Solar panel manufacturing is energy intensive on many fronts, but one process in particular — annealing the silicon in ovens — is also time-consuming.
A team from Macquarie University, led by senior lecturer Dr Binesh Puthen Veettil of the School of Engineering, has found that microwave radiation can replace the high temperatures traditionally used for annealing, bringing a host of advantages.
Not only is the microwave approach faster — taking just a few seconds instead of approximately half an hour — but it uses significantly less energy, allows for more focused heating and is a cleaner process.
As promising as this result is for potentially reducing solar panel manufacturing’s large carbon footprint, the research team also made another useful discovery, using microwaves to enhance the recyclability of solar panels.
Veettil’s team found that being able to selectively heat silicon meant the plastic (ethylene vinyl acetate) coating that protects the silicon plate from moisture and contamination could be softened to the point where it can be peeled off mechanically, while the other components of the solar panel such as glass and aluminium remained at room temperature, minimising damage.
“In the experiment we manually peeled it off, but it would be possible to do it using a mechanical arm or a robot in situ while it is being heated to make the best use of it,” Veettil said.
Retrieving value from waste
This means other elements within the solar panel can be retrieved more easily. Currently, if a panel is recycled, the aluminium frame and junction box are removed, and the rest is crushed, heated to around 1400 degrees and washed in toxic chemicals to remove the plastic and glass. It’s generally viewed as not worth the effort.
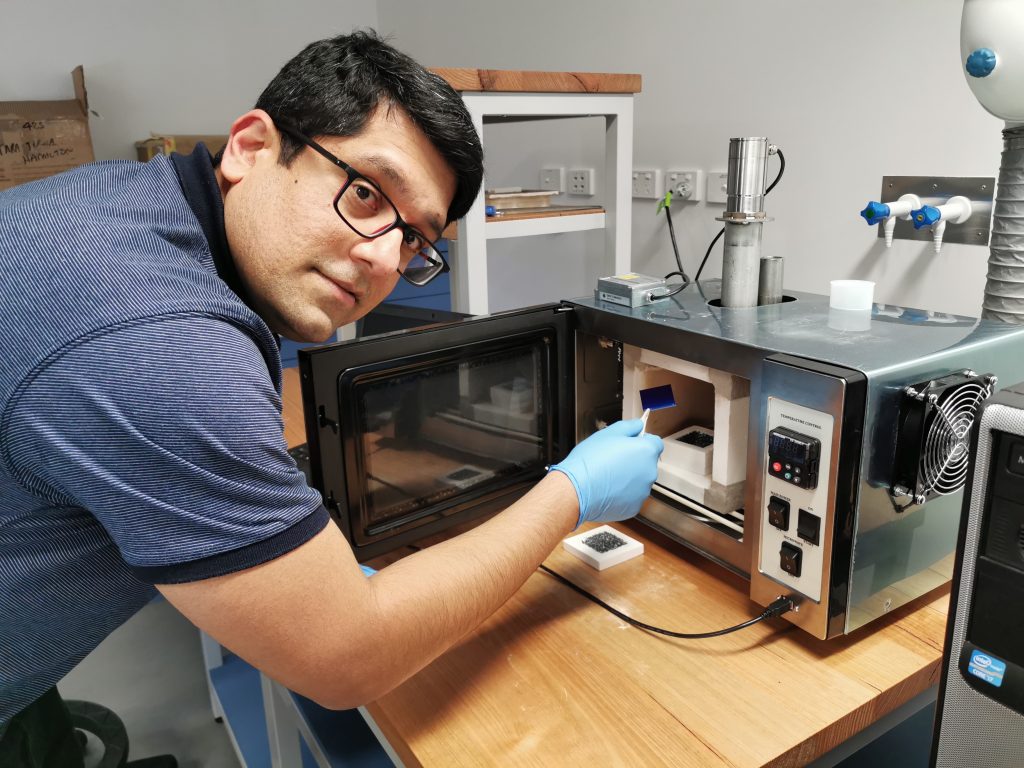
An estimated one million solar panels will reach the end of their photovoltaic life over the next 20 years in Australia.
The new process opens the way to retrieve more value from the used panel, such as silver, using a method that is more environmentally friendly. “Here we are using very little energy just to soften the plastic,” Veettill said, adding the team is yet to calculate the difference in energy consumption between the two methods.
“At the moment about 50% of the value of recycling a solar panel comes from the silver content. The glass is not regarded as valuable because it’s crushed, and then when you try to extract the silver, it comes to around 0.06% by weight.
“But if you are able to remove the glass intact, which is about 12 kilograms, the silver content in the remaining materials is 1.46%. That’s about 25 times more than we get now.”
This provides two benefits. The unbroken glass pane has many potential reuse options, including for new solar panels, while the increased silver content helps to make the previously unprofitable recycling process more appealing.
Turning concept to reality
The next step for Veettil’s team is to optimise the process so it is faster and more attractive to industry.
“We also want to develop a tool that is compatible with other inline tools so the panels can be pulled in one after the other, around one panel per minute,” he said.
“The third step is to develop a robot or a mechanical system that will separate the glass from the solar cells while the microwave is working. At the moment we separate it after the microwave radiation, but we want to do it in situ.
“This will also take a bit more R&D and more funding, probably in collaboration with industry.”
Veettil said industrial belt-driven microwaves exist in the food industry, for example, but they are working on a more compact design similar to an offset printer where the solar panel would be fed through one end, the microwave would be along the width of the panel and it would come out separated.
“We have a patent pending now. I’m hoping that this is going to be a big, big thing. We’ve been in the right place at the right time,” he said.
Meanwhile, the team is also continuing with the original aim of the research relating to solar panel construction, where they estimate microwave technology is about 40% more efficient than the current process.
“But we did not replace all the thermal processes. This was looking at just one, so it’s just the beginning of the study,” Veettil said.