When Genoa’s Morandi Bridge tragically collapsed in 2018, a replacement bridge was needed as quickly as possible to reconnect a city that found itself divided in half. Not only that, the bridge would need to avoid falling victim to the same issues that investigators suspect spelled Morandi’s demise.
As an alarm rang out across the construction site, the last span of the 1062-metre-long steel deck of Genoa’s new bridge was hoisted into place. The celebration was part of an event this past April marking the bridge’s completion in record time: a mere 10 months from start to finish about half the time it would have normally taken.
Such was the excitement of the bridge’s imminent opening that ships at the major Italian port nearby added the sound of their horns to the triumphant clamour.
When the Morandi Bridge tragically collapsed in 2018, it left Genoa with limited connections to the region and nearby France. Detours for trucks and other vehicles led to unwieldy bottlenecks, and the economy has suffered as a result.
A replacement bridge was needed as quickly as possible to reconnect a city that found itself divided in half after the collapse. Not only that, the bridge would need to avoid falling victim to the corrosion that investigators suspect spelled Morandi’s demise.
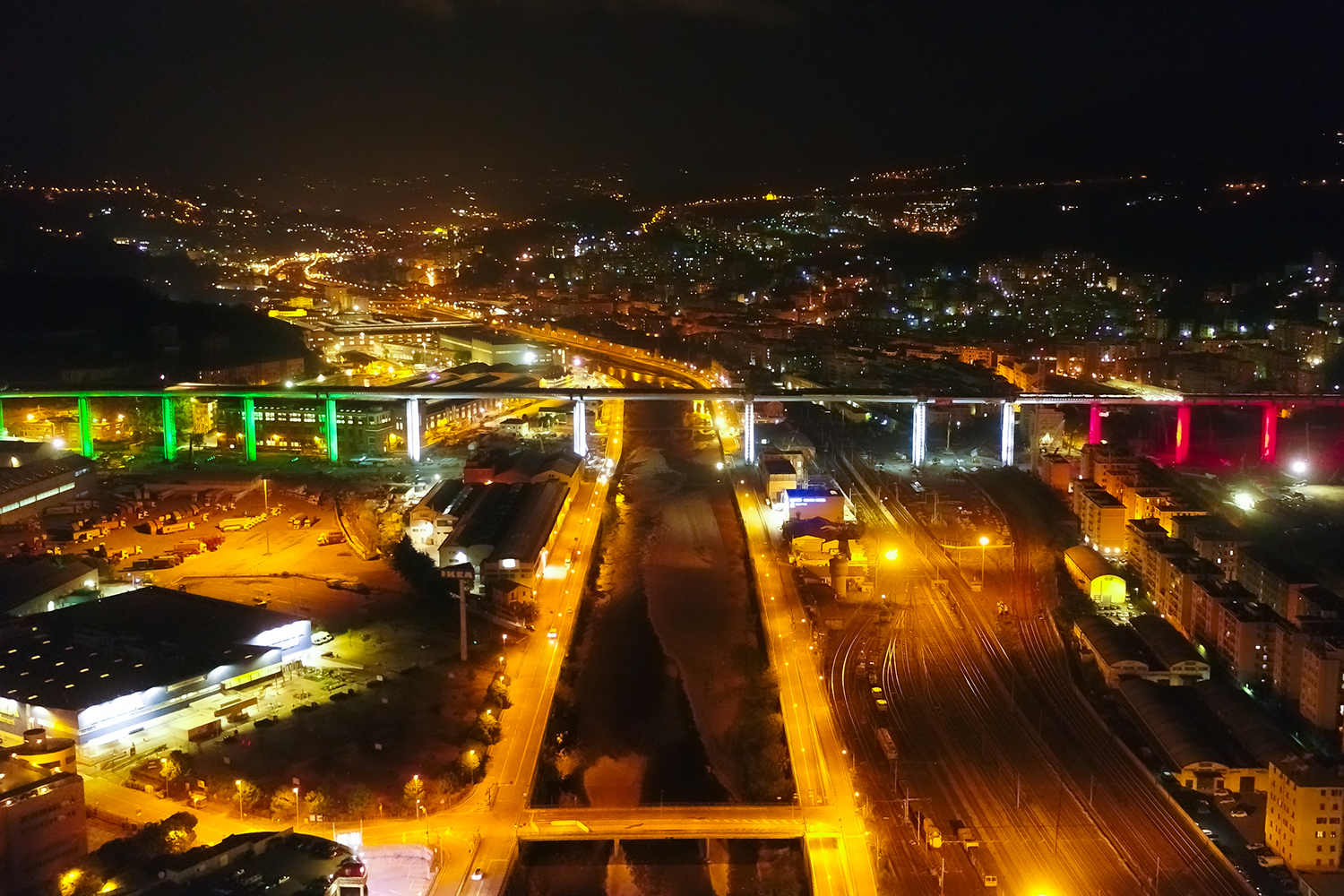
Although the bridge still needs to be paved and tricked out with the latest smart technology, the main structure is complete. It came into being as the strand jacks lifted the span into place about 45 metres above ground between two piers on the east side of the Polcevera riverbed, which the bridge straddles. At 44 metres in length, the span weighs 900 tonnes.
A running start
The speed at which the €202 million bridge has been built by Webuild (formerly Salini Impregilo, a global infrastructure group based in Italy) and its partners has become a source of inspiration for a country where projects are usually stuck in bureaucratic paralysis for years.
It has come to be known as the Genoa Model, and the government is thinking of applying it to other projects as it looks at using infrastructure investment to revive an economy laid low by the COVID-19 lockdown.
And it is all thanks to an innovative approach adopted by all parties involved.
“With the construction of the new Genoa bridge, we have shown that in Italy, quality infrastructure can be done,” Webuild Chief Executive Pietro Salini told attendees at the April event, which included Italy’s prime minister, Giuseppe Conte.
“All that is needed is the right companies with the right expertise and the willingness to build public works quickly.”
Webuild’s expertise was also behind the construction of the Skytrain bridge, the landmark structure of Sydney Metro Northwest that is the first cable-stayed curved railway bridge built in the country.
The mayor of Genoa acted as the project’s commissioner, which helped remove some of the adversarial rapport that can develop between client and contractor. Since the objective was shared, it was in everyone’s interest to work together.
It was also agreed to push the project forward on multiple fronts and abandon the linear approach usually applied to building infrastructure. In so doing, the construction site at one time played host to more than 40 companies working on approximately 20 tasks contemporaneously.
At the peak of the bridge’s construction, more than 1000 people worked on-site on any given day.
A quick pace was set from the get-go: a month after the tender was awarded in December 2018, all parties signed the contract before the technical designs were completed, and the necessary permits were given without delay.
During subsequent months, demolishers were still busy dismantling and removing the Morandi wreck as construction workers began driving piles for the new structure into the ground. As soon as the first piers were erected, they set about installing the spans.
The simplicity of the design by Renzo Piano, the famous Italian architect behind the One Sydney Harbour project, made the work easier as well. Reflecting the trend towards modular construction, the bridge’s parts including the spans were prefabricated, adopting the same shape and size, in many cases.
As for the piers, they too are identical in size, sharing the same external dimensions of 9.5 metres by 4 metres. This facilitated the use of a single type of external formwork for their erection.
The piers also reflect Piano’s sense of the aesthetic: they are the same colour and texture because they are made with a concrete whose aggregates come from the same quarry.
Forward thinking
In addition to the construction methods, the bridge distinguishes itself by the level of technology it will contain.
Robots will do the upkeep, carrying out structural inspections as well as cleaning and maintaining the solar panels and wind barriers fitted along the entire length of the deck.
The solar panels will not only power the night lights along the bridge, but also the cameras and sensors like accelerometers and extensometers that will monitor the bridge’s soundness. The information, transmitted in real time to a database, will be offered for the future design of bridges of this type.
Inside the bridge’s steel structure will be a system that dehumidifies the air to avoid corrosion caused by the sea air.
There will also be a drainage system to channel rainwater for treatment before releasing it into the river, increasing the bridge’s credentials as a sustainable piece of infrastructure.
The pace to complete this project has been relentless, with the site remaining open 24 hours a day, seven days a week. Workers downed their tools for only one day – Christmas.
Nor have things slowed during the lockdown, as the government has deemed the project too strategic to halt. During this time, additional safety measures have been adopted to safeguard the health and safety of the workers.
What has kept everyone working at this level of productivity has been a shared sense of duty towards Genoa and its people, a commitment to close the wound suffered from the Morandi tragedy.
In his praise of the accomplishments made along the riverbed traversing an industrial park, Prime Minister Conte emphasised the project’s wider meaning.
“This is a construction site that belongs to Genoa as much as it does to Italy… (a country) where everyone does his or her part with a sense of duty and responsibility,” he said.