When considering the impact of coronavirus on various sectors around the world, one industry that will undoubtedly face some tough challenges is public transportation. A mainstay of cities worldwide, public transit experienced a dizzying ridership plunge as countries locked down. But this lull has also been a good time to speed up infrastructure repairs in some cases and progress new plans for recovery in others.
One city making great strides to move new infrastructure forward is Auckland, New Zealand, whose largest and most densely populated urban area has a population of 1.5 million. Public transport is becoming more popular with Auckland commuters, with the city reaching 100 million public transport trips in June 2019—a number last seen in the early 1950s when trams were at their prime in the city; about 20% of these trips are made by train. Meanwhile, Auckland’s population is estimated to grow to 2 million (PDF, p. 9) residents by 2033.
To handle future public transport, Auckland is developing its most ambitious transport infrastructure endeavour to date: the City Rail Link (CRL) project. This 3.45-kilometre (2.14-mile) twin-tunnel underground railway will link to existing lines on the city’s rail network, doubling its capacity and connecting more areas to cut travel times, ease congestion on roads, and reduce pressure on an overloaded bus system.
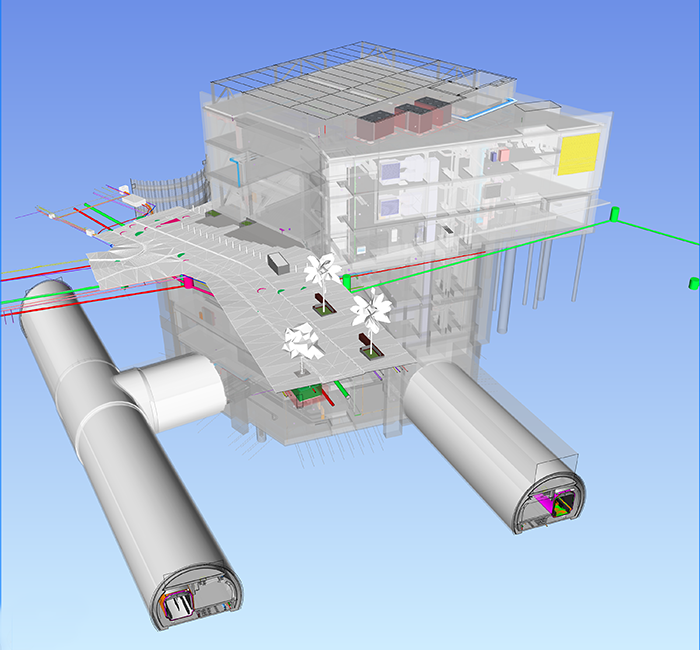
A concept 100 years in the making
The idea for an underground railway in Auckland dates back to the 1920s, but formal work on the project began in 2012. Construction is progressing on two new stations: Aotea at Albert Street and Karangahape at Karangahape Road. Redevelopment is planned for Mount Eden station to connect the Western Line with the CRL and Britomart Station, converting the dead-end station to a two-way through station for faster travel between the city’s eastern, western, and southern areas.
“This is the largest, most complicated infrastructure project New Zealand has ever attempted,” says Daniel Jurgens, digital engineering manager at the Link Alliance.
“The sheer volume of people working on it and the very nature of completing the project and figuring out problems is creating a groundbreaking shift that will change the New Zealand architecture, engineering, and construction industry.”
Leading the design and construction of the main CRL tunnels and station contract is the Link Alliance, a consortium of local and international companies with a wealth of experience in delivering large-scale infrastructure projects. The Alliance includes French construction firm Vinci Construction Grands Projets S.A.; Soletanche Bachy, a French geotechnical infrastructure firm with offices in New Zealand; integrated services company Downer; infrastructure firms WSP; AECOM New Zealand; New Zealand environmental and engineering consultancy Tonkin + Taylor; and City Rail Link Limited (CRLL).
“It’s the first time I’m working in an alliance, but I believe it’s the correct contract model for such a large project because it enhances collaboration to a point I’ve never seen before,” says Brice Gaudin, BIM (Building Information Modeling) manager at the Link Alliance. “We’re all working together on the same objectives and the same requirements, with a huge amount of learning in between.”
Driven by teamwork and digital workflows
The underground railway includes tunnels as far as 42 meters (138 feet) below the city centre, and the alignment of these tunnels follows the lines and curves of the roads above. Allowing space for trains to safely traverse curved tunnels is challenging, so the design team developed computational design scripts in Autodesk Dynamo for the complex geometry.
“To accurately know how trains move along the alignment, around curves and slopes throughout the tunnel, is complex,” says Dean Burke, digital engineering lead at the Link Alliance. “The structure and services within the tunnel move and switch sides to accommodate the trains’ kinematic envelope. With 2D-based drawings, we would have just allowed more space to accommodate for these complexities. Using computational design, accurate 3D models, and spatial coordination, we can drive tighter tolerances and optimise designs.”
Employing computational design also worked in the team’s favour when the project scope expanded to accommodate longer, nine-car trains that could transport up to 54,000 passengers during peak hours instead of the original six-car trains with a capacity of 36,000 people. Rather than starting from scratch or making manual modifications, Burke and his team were able to rerun computational design scripts and parametrically update the 3D models to allow the new design criteria with minimal rework.
Cesare Caoduro, digital engineering manager for tunnels at Link Alliance, says that the CRL project is allowing the team to explore more efficient ways to use computational and generative design to reduce the time to produce updated models based on design changes.
“Some examples include the use of generative design to produce an accurate design model of the tunnel-boring machine based on both the contractor and the design requirements,” Caoduro says.
“The model will include the optimisation of the segmental lining elements based on the track geometry, providing at any step the element that minimises the deviation from the design intention. A further development, under piloting, will introduce design and construction goals like maximising the rock excavation and a form-finding algorithm to optimise the spatial placement of elements based on ground constraints.”
Meanwhile, BIM 360 Design is helping the CRL project achieve sustainability—a core objective for building Auckland’s underground railway. “We’re pushing materials information into our 3D models, which then come out with the cost, quantities, and sustainability effects,” Jurgens says.
Connecting data, from visualisation to virtual reality
The Link Alliance turned to digital engineering to address many of the challenges that come with building an underground railway. The Alliance uses virtual reality for many aspects of the project, from design reviews to site safety trainings. This reduces costs by visualising how production will play out on-site, in the context of both design realisation and work safety. The team is also developing a driving simulator to help railway operators better understand the new systems.
The Alliance depends on point-cloud data to capture site information, combining terrestrial LIDAR scans and drone survey information. Surveyors conduct monthly drone flights on-site to assess construction progress; that information is directly linked to design and constructability models.
“Making data available on-site is a game changer for the people actually building; updating the digital model with accurate site information is crucial in that regard,” Gaudin says.
The Alliance is developing temporary-works design models and construction-sequence animations to confirm buildability; asset-management information is being integrated in BIM while design and construction are ongoing.
Tying all these technologies together is a common-data environment in SharePoint, Microsoft’s cloud-based collaborative platform. This environment serves as a central hub for teams to find the information they need, along with links to their software packages, including Autodesk Civil 3D, InfraWorks, Navisworks, ReCap, and Revit.
“We also have to store minutes of meetings or decisions about design,” Gaudin says. “So we’re not only talking about data but also communications and other ways of sharing. It’s really about managing this as a whole.”
This common-data environment proved especially beneficial when COVID-19 restrictions were enforced and all teams had to work remotely.
“When COVID-19 came along, we just carried on — it was business as usual for us,” Jurgens says. “If we didn’t have this common-data environment, the project would have stopped.”
Upskilling workers through targeted training
Nearly 1,200 people are working on the $4.42 billion New Zealand dollar ($2.86 billion) project, due for completion in 2024. Finding enough people with the requisite skills and knowledge was a huge undertaking, so the Link Alliance devised an ongoing training program with targeted training for different roles—from digital design tools for architects to tunnel excavation methods for construction and engineering teams. Training sessions were also extended to external suppliers and subcontractors.
“We’re upgrading the skill set of everyone on this project, especially in the digital space, and that’s where I see this project transforming the industry,” Burke says. “We’ll be able to deliver not only on the extensive requirements for this project but also for future projects.”
Beyond upskilling, the CRL project is paving the way for the digital future of architecture, engineering, and construction in New Zealand. “We’re laying down a digital foundation that other projects can build upon,” Jurgens says. “Once we start to get these digital representations of our built environment, it’s going to be groundbreaking. It will completely change how we do everything, which is the first step in the journey.
“With the Alliance, we are all in this together, literally sharing an office as a collective and working on live information across all of the stakeholders,” he continues. “We embrace the notion of being temporary custodians of knowledge, with 3D models passing through their lifecycle stages from design to asset management. This requires additional due diligence to allow everyone to confidently pass on the 3D digital representations to the next part of the supply chain—a legacy that is captured in our alliance objectives. Using digital workflows enables best outcomes throughout the entire lifecycle and ultimately contributes to the greater good of New Zealand.”
This article originally appeared on Autodesk’s Redshift, a site dedicated to inspiring designers, engineers, builders, and makers.