One technique for treating effluent produced by the meat industry turns a dirty problem into a green solution.
Using bacteria to treat agricultural waste is not new or uncommon. Lagoons and tanks have been used for decades to digest effluent with the help of microorganisms.
However, covered anaerobic lagoons — where methane that has been produced by reactions under a sheet is trapped — are “once again being investigated” by the meat industry, according to a 2017 fact sheet from the Australian Meat Processor Corporation and Meat and Livestock Australia.
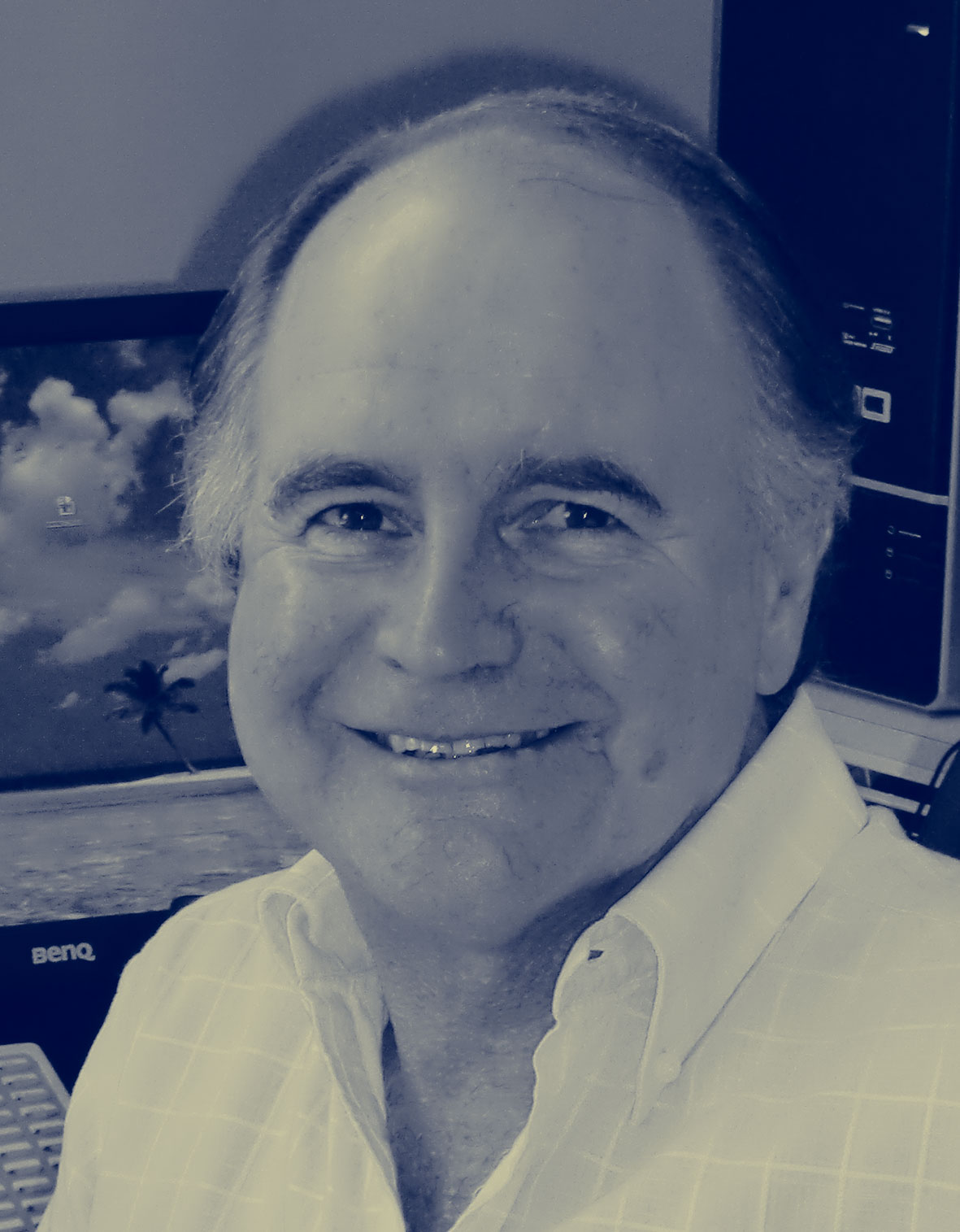
Mike Bambridge, a chemical engineer and owner of CST Wastewater Solutions, has been designing and installing systems for anaerobic — meaning ‘without oxygen’ — bacteria digestion for more than a quarter of a century.
In 2014, his company installed a covered anaerobic lagoon at Oakey Beef Exports, an abattoir owned by Japan’s NH Foods, in Queensland’s Darling Downs.
“That’s been the one and only for us in Australia,” he told create.
“There’s been a couple done overseas, but most of the anaerobic plants are done in above-ground tank systems.
The Oakey reactor has been able to scrub between 75 and 99 per cent of biochemical energy demand (BOD) value from effluent, with minimal intervention by its owners, and regularly produces between 3000 and 4000 m3 of biogas per day.
Pre-treatment involves screening out particles bigger than a half-millimetre, and limiting fat, oil and grease (FOG) to under 500 mg per litre.
This helps avoid blockages in pipe diffusers and build-up of sludge under the cover, both common issues with these systems.
“Because you’ve got a gas involved in the lagoon, you can get a flotation effect if you’ve got a lot of free oil and grease,” Bambridge said.
“The grease will come to the surface and not stay in the main liquid, and so it doesn’t break down as easily and you end up with crust.”
Asked about innovations in this particular installation, he cites the design of the distribution system for effluent across the bottom of the lagoon.
A manifold spreads wastewater throughout the pond instead of piping it in at two or three places.
The result is a better mixing pattern and better loading rates.
“It spreads the gas production over the whole lagoon,” he said.
“The more of the wastewater that comes in contact with the bacteria, the more efficient the breakdown of the wastewater.”
Gas produced rises to the underside of the cover and is sucked up by low-pressure fans.
This biogas is stored in a 26-m-tall, double-membraned, PVC-coated polyester fibre tank. The methane is used by the plant’s boilers after it has been dried and sulphides have been removed.
The plant will come up to its fifth anniversary late this year, at roughly the same time its owners will have achieved payback on their investment through savings from producing their own natural gas.
It is uncertain if covered anaerobic lagoons are the way of the future for abattoirs, food processors and others.
However, if the east coast’s gas difficulties continue, and if a price on carbon is introduced in the future, then the case would not be weakened.
Hands-off solution
CST Wastewater Solutions’ anaerobic pond has been self-regulating and relatively maintenance-free, said Bambridge, save for routine pump and instrumentation checking, and one occasion on which pH had to be adjusted to ensure that the bacteria were operating optimally.
“The anaerobic lagoon reactor itself has not been touched since it was installed, so the cover and the distribution system, etc., are as per original,” he said.
No extra bacteria have been added since the original colony was seeded using sludge from a nearby sewage plant.