From Melbourne’s North East Link to Queensland’s doomed Paradise Dam, we outline why many megaprojects have blown their budgets – and how cost engineers can help keep them down.
Massive budget blowouts in major Australian public infrastructure projects are cropping up left and right.
As revealed last week by Victoria’s auditor-general, the North East Link road project is now costing taxpayers $26.2 billion, up 67.6 per cent on its 2017-18 costing.
In Queensland, January saw the announcement that the Paradise Dam will cost at least $4.4 billion to rebuild, after safety work begun in 2020 to rebuild the flood-damaged dam wall was declared a failure.
Early this month, Transgrid announced its Project EnergyConnect, a 900-km electricity transmission connection between South Australia, Victoria and NSW, had blown out from an estimated cost of $2.28 billion to $4.1 billion.
To cost engineers, these figures represent avoidable scenarios.
Abhijnan Datta CPEng, Project Director, Infrastructure at Turner and Townsend and National Chair of the Australian Cost Engineering Society, said cost engineers are concerned with three major goalposts: cost, time and scope.
“A lot of people confuse cost engineering with project accounting, or financial accounting,” he told create. “The best way to put it is: a cost engineer is like the navigator in the car rally. They are providing insights to the driver along the way. They are doing all the calculations; they need to understand the scope of work.
“Unless you understand all of it together, it’s very hard for you to be a functioning project controls engineer or cost engineer.”
It’s all in the planning
A common denominator in trouble-plagued projects is a lack of thorough early planning. It’s a truism, but planning is key. Spending more time on the drawing board before tools are picked up will save time and money down the track.
“On a lot of the projects you hear about the overrun, but the first step is to say, what is it overrunning? So, the first step is understanding the scope and having a thorough estimate.”
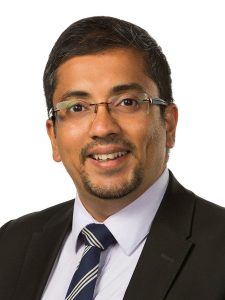
The political element attending major infrastructure works is another curveball that can wrong-foot a project from the start.
“I always say that it’s a politician’s dream to get the shovel on the ground at the earliest and a cost engineer’s nightmare. Major projects are a big political opportunity and there can be pressures to hasten the process. But these kinds of projects are large and complex and typically, when it goes wrong, it goes horribly wrong.
“It’s the job of the cost engineer to invest in the basics of data, capture lessons learned and leverage the data to gain insights from it. It’s about spending time on the boring stuff.”
Inland Rail
A massive infrastructure rail project linking freight between Melbourne and Brisbane, Inland Rail has doubled its original cost estimate from $16.4 billion in 2020 to $31.4 billion. It will have run four years over time if it meets its 2030 completion date.
As a logistics project, Inland Rail is relatively straightforward in engineering terms, Datta said. The major issue has been the lack of appreciation for risks in mega projects and approval timelines. Dr Kerry Schott’s review of the project outlined 19 recommendations; one of them was reviewing the Australian Rail Track Corporation’s risk management and reporting systems, with a view to addressing issues experienced with the approval process.
Running through three states and jurisdictions adds complexity to the project.
“A lot of these mega projects suffer from a gross underestimation of risks. Half of the challenges for Inland Rail are hardly technical. These are stakeholder challenges.”
Projects such as this can have their detailed upfront construction programs undermined by the technicalities of the upfront work such as environmental approvals, legislation and land acquisition.
“Engineers know how to build but they are not traditionally good at communicating and navigating stakeholders,” Datta said. “Project organisation needs to understand those complexities.”
Snowy Hydro
Set to pump water through 27 km of tunnels between two dams in the heart of Kosciuszko National Park in NSW, Snowy Hydro 2.0 has grown from an initial cost of $2 billion to an estimated $12 billion.
The project took a turn when its tunnel boring machine, dubbed Florence, became stuck in soft ground for the better part of 2023.
“It was a huge celebration when it got launched, and then it got stuck in the sludge,” Datta said. “It’s a technically complex project, but a cost engineer is there to think of risks: what’s the uncertainty in this project with respect to ground conditions?”
In a project such as this, Datta said, reference class forecasting is a useful tool. Looking at similar projects and drawing references can help form a reliable estimate.
“You do a bottom-up estimate, but you also look at reference classes – you take that data where it has been done a number of times. Those things come naturally to cost engineers. They have the understanding of engineering, but also the understanding of project management, stakeholder management, data, decision making, communication. They have ownership of that almost single source of truth for the project.”
North East Link
Victoria’s major road project has had a budget blow-out to $26.2 billion. Statistically, however, road projects have the least chances of going wrong.
“Like transmission-line projects, a road project is linear and repetitive,” Datta said. “Technically, they’re quite simple.”
They might be a civil engineer’s dream, but it’s crucial to get things right on paper before getting people mobilised on the project.
Planning for change
Scope creep – where a project’s parameters gradually expand due to added features, requirements or changes requested by stakeholders – is a common occurrence on major projects. By investing in proper change control with the help of cost engineers, anything that changes from the original scope can be monitored and allowed for.
“My message is, don’t get down to building something unless the requirements are clear, unless you have a proper understanding of the project, investing enough time on your drawing board before just going gung-ho and going out to the site,” Datta said.
“Projects don’t go wrong – they literally start wrong. A lot of times it’s a vision or aspiration, which is great – that’s how humanity functions, but you can’t start building something just based on vision or aspiration. It has to have that deeply researched, thoroughly tested program before you start getting boots on the ground.”