The circular economy has become more than a concept. A number of innovative Australian companies are showing how the principle will play out in real life.
The term ‘circular economy’ is often thought to mean better management of waste streams, but that’s only one part of true circularity.
A central tenet of circularity is designing out waste. Products and materials are created so they can be repurposed either through reuse or recycling — including composting — to minimise the need to extract virgin resources to make new items or add to landfill.
There are also economic benefits. Circular Australia Hub estimates there is more than $200 billion in economic opportunity in circular solutions and the potential for 17,000 new jobs.
And with about 35 per cent of Australian waste currently going to landfill, disposal costs could be reduced.
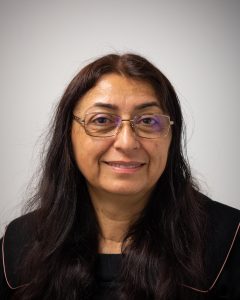
The opportunity with the most potential from an engineering perspective is in process engineering — manufacturing — as this contributes about $100 billion to Australian GDP annually, according to Lucy Baker, Chair of Engineers Australia’s Environmental College.
“There is also potential for increased recycling using waste [or] demolition products from the construction sector,” she said.
“The biggest challenge is in the implementation, to ensure that the products meet all the respective standards, so that they are functional and fit for purpose.
“If recycled products do not meet the same standards of new products, implementation in construction can be more difficult.”
But as the circular economy becomes more established, a range of innovative recycling companies are finding success in viewing waste as a resource.
Great Wrap
Australian households throw out more than 300 kg of food waste each year. Great Wrap has found a way to convert this waste into a plastic-film alternative.
“Currently, we are using an imported potato waste-derived bioplastic, compounding it with other biomaterials to produce our compostable home wrap and our compostable pallet wrap,” said Martin Markotsis, Great Wrap’s Materials Innovation Manager.
“We have in-house extrusion compounding capabilities to compound our film material, which we then process into cast stretch film in our factory in Tullamarine in Victoria.
“Our vision for further food waste valorisation over the coming two years includes using Australian potato waste to produce polyhydroxyalkanoates (PHAs) in biorefineries built here in Australia. We would then compound the locally produced PHA material in-house and then produce film on our cast film lines.”
Markotsis said the company is looking to optimise processes to produce bioplastics such as PHA in a sustainable and economical way, so final products can compete on performance and pricing with petrochemical plastic wrap, which ends up in landfill.
Logan Water Biosolids Gasification Facility
The population of the Queensland city of Logan, south of Brisbane, is growing fast, with 150,000 more people predicted to move to the area by 2030. That means a lot of sewerage to process.
The solution developed by Logan City Council and Logan Water was a $28 million gasification facility, which was completed last year.
The facility sees waste-activated sludge pumped to centrifuges, where biosolids are dewatered to 22 per cent dry solids, then transferred to 34 t, 18 m industrial-grade belt dryers that dry the biosolids to 90 per cent dry solids.
The dried biosolids move to the gasification phase where they are processed in a hearth at 650°C for about 100 seconds to create a charcoal-like product called biochar.
“Biochar contains nutrients like those found in commercial slow-release fertilisers and can also be added to soil, asphalt, concrete and bricks to sequester carbon for thousands of years,” Mike Basterfield, Group Manager of Logan Water, said. “It also has potential to be used in industrial combustors as fuel and feedstock, and as activated carbon.
“The hearth also produces a syngas that combusts in an oxidiser that is set to around 850°C for a two-second retention time, which destroys persistent organic pollutants such as PFAS.
“The heat produced is recovered from heat exchangers and the air is treated through a wet scrubber and electrostatic precipitator to ensure emissions meet environmental requirements. The facility reuses the heat energy to dry the biosolids in the belt dryers.”
Basterfield said that prior to the gasification facility, gravity drainage decks and belt filter presses were used to dewater the biosolids to around 14 per cent dry solids.
Every day, four truckloads of biosolids would be transported 300 km to the Darling Downs region to be applied to land — a process that accounted for 30 per cent of the total wastewater treatment plant operating costs.
“Now, the gasification process reduces carbon emissions by about 6000 t a year, operational cost savings and carbon credits will return almost one million dollars a year, and a new revenue stream is being created from biochar sales,” Basterfield said.
But it’s not only the council’s budget that benefits. The innovation has identified a role for biosolids in the circular economy: a community-created resource can return nutrients to the earth and sequester carbon for thousands of years.
Planet Protector
Until 2016, the underbelly wool of sheep generally ended up in landfill. Meanwhile, approximately 30 per cent of global landfill is polystyrene. A single solution exists for both waste problems.
“We’ve used waste wool unsuitable for the textile industry , given it a second life and commercialised it into a product that is insulated packaging to replace polystyrene in cold supply chains,” said Planet Protector founder Joanne Howarth.
The wool used in Planet Protector “goes through a very rigorous washing process — which involves six baths of boiling hot water — and then it’s felted to our specifications”.
It is then sealed with recyclable or compostable food-grade wrap.
“We have multiple clients who have set up a closed-loop recycling program and they are able to use the product multiple times,” Howarth said.
The wool can be composted when it can no longer be reused. In addition to providing a new revenue stream to sheep farmers, the company said it has so far prevented approximately 40 Olympic-sized swimming pools of polystyrene from going to landfill.
Sustainable Salons
Human hair has a remarkable composition: it is one of the highest organic sources of nitrogen and contains 20 other elements such as sulfur and carbon.
“We’re the world’s biggest collector of human hair but we don’t just collect it — we study it and turn it into products such as hair booms that clean up oil spills,” Paul Frasca, founder of Sustainable Salons, said.
The organisation has collected 80 t of hair from Australian and New Zealand hairdressers and pet groomers since its inception in 2015, and one kilogram of hair can remove 840 g of spilled oil from seawater.
“We have another product coming out later this year: hair fertiliser,” Frasca said, adding that the company also produces Refoil, made from aluminium collected from salons.
Sustainable Salons is also investigating how human hair can replace heavy metals in flexible organic light-emitting diode, or OLED, displays and solar panels.
Hair is 45 per cent carbon and experiments have shown that exposing hair to extreme temperatures can extract carbon dots, which can then be blended with other agents to make them luminescent.
The road ahead
Baker said the engineering profession is developing good processes for plastics, tyres, glass and paper.
However, Australia has set itself an ambitious target of recycling or reusing 80 per cent of its waste by 2030. That figure currently stands at about 63 per cent.
“Engineers need to work closely with investors and government to [find] a solution that works for us. We are missing a national recycling framework … integrated across Australia,” Baker said.
Across the profession, she said, engineers should emphasise the potential and importance of the circular economy in Australia’s sustainable future, and encourage further exploration and adoption of circular economy practices.