Prosthetic limbs are often weighed down by heavy actuators required to move joints. Materials science researchers have been inspired by the humble cucumber plant to develop fibres that could lighten the load.
A research team from Massachusetts Institute of Technology (MIT) has produced a single fibre that can coil tightly and exert a pulling motion up to 650 times its own weight when stimulated by heat. This is similar to the “coiling and pulling” action displayed by the team’s muse: cucumber plant tendrils that lift the main stalk up towards the sunlight.
The researchers said these fibres, made from two polymers with very different thermal expansion rates, could be combined in bundles – like muscle fibres in the body – to create artificial muscles for prosthetic limbs or robots. In these applications, the low weight and fast response times would give the new material an edge on the pneumatic or hydraulic systems that currently perform the function.
“We have activation times [in] the order of tens of milliseconds to seconds,” said Associate Professor Polina Anikeeva, adding that the reaction time depended on the fibre dimensions, which can range from a few micrometres to a few millimetres.
Anikeeva also suggested that the fibres could be used in tiny biomedical robots to perform pre-programed functions inside tight spaces such as arteries.
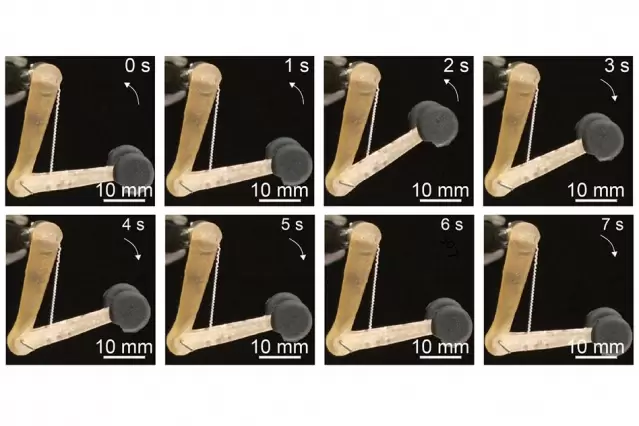
Strength in simplicity
This isn’t the first time researchers have developed a light and economical material that could be used to imitate the bending motion of human joints. In 2016, a study by the Mechanical Engineering Department at MIT developed a nylon fibre-based system that bent in response to heat.
According to researcher and postdoctoral student Mehmet Kanik, the strength of the current research is in its simplicity. He added that there are “virtually limitless” possibilities for similar materials because a similar effect could be achieved with “almost any combination” of two polymers with different expansion rates.
In the MIT study, recently published in Science, the research team combined a stretchy cyclic copolymer elastomer with a less pliable thermoplastic polyethylene material. When stretched, the combined fibre formed a tight coil, similar to the tendril of a climbing plant.
Then “serendipity” stepped in. When Kanik first held the fibre in his hand, his body heat caused it to coil even more tightly. On further investigation, Kanik discovered that it only took a small heat increase (1°C) to trigger the coiling and pulling action. During testing, the researchers reported that a single strand of material could lift up to 650 times its own weight. They also found that the fibres could expand and contract over 10,000 times.
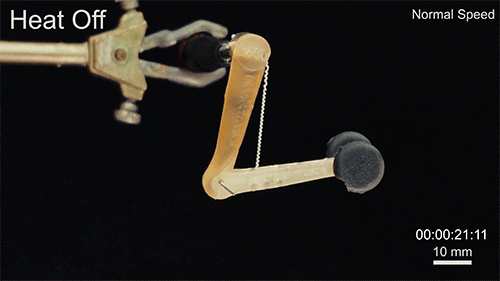
The researchers also bundled fibres to increase their pulling strength. Bundles of up to 100 fibres were tested during the study.
The fibres were manufactured using a fibre-drawing system that allowed other elements to be incorporated. To measure the tension exerted and experienced by each fibre, Kanik coated them in nanowire meshes, which acted as sensors. In the future, the researchers said that heating elements could be included to remove the need for external heat sources to trigger contraction.
To take this “simple” concept further, the researchers have suggested that incorporated sensors could be used to provide feedback from prosthetic limbs, and fibre bundles equipped with a closed-loop feedback system could provide robots with automated and precise control of arms, legs and gripping tools.