The future of robotics is collaborative, according to one researcher hoping to help machines and humans work in harmony.
As robots multiply, advance and increasingly make their way into workplaces, their ability to respond to our cues will only become more important.
Dr Marc Carmichael, Lecturer at the University of Technology Sydney’s Centre for Autonomous Systems (CAS), is one researcher who is trying to help robots and people work together seamlessly. His work, which earned him a spot on create’s 2018 list of Australia’s Most Innovative Engineers, includes a long-running effort to take the physical stress out of abrasive blasting.
It began in 2013 when Carmichael took concepts for controlling robotic exoskeletons from his PhD and used them to help workers wield abrasive blasting tools.
“It’s a philosophy of having a robot able to know what the capabilities of the user are, what are the requirements for the task they’re about to do, and how much assistance they should provide. And in some applications — robotic rehabilitation is a big one — that’s critical,” he told create.
“We are taking that philosophy and applying it to more industrial activities.”
Abrasive blasting is a strong candidate for automation. The process produces hazardous and inhalable material. It can be dull. It might require workers to hold awkward poses for long periods of time. And the reaction forces created can be powerful — up to 400 newtons.
After phase one of the project with Burwell Technologies, Carmichael abandoned his first approach, using a wearable robotic exoskeleton, in favour of a Universal Robots UR10 arm. Work with Burwell Technologies continued from 2014 to 2017 via an ARC Linkage Project.
Carmichael said the interaction with the arm, the implementation, and the control algorithms involved wasn’t too different between the exoskeleton and the robot.
“The main difference is that one you wear on your body and the other one is planted on the floor,” he said.
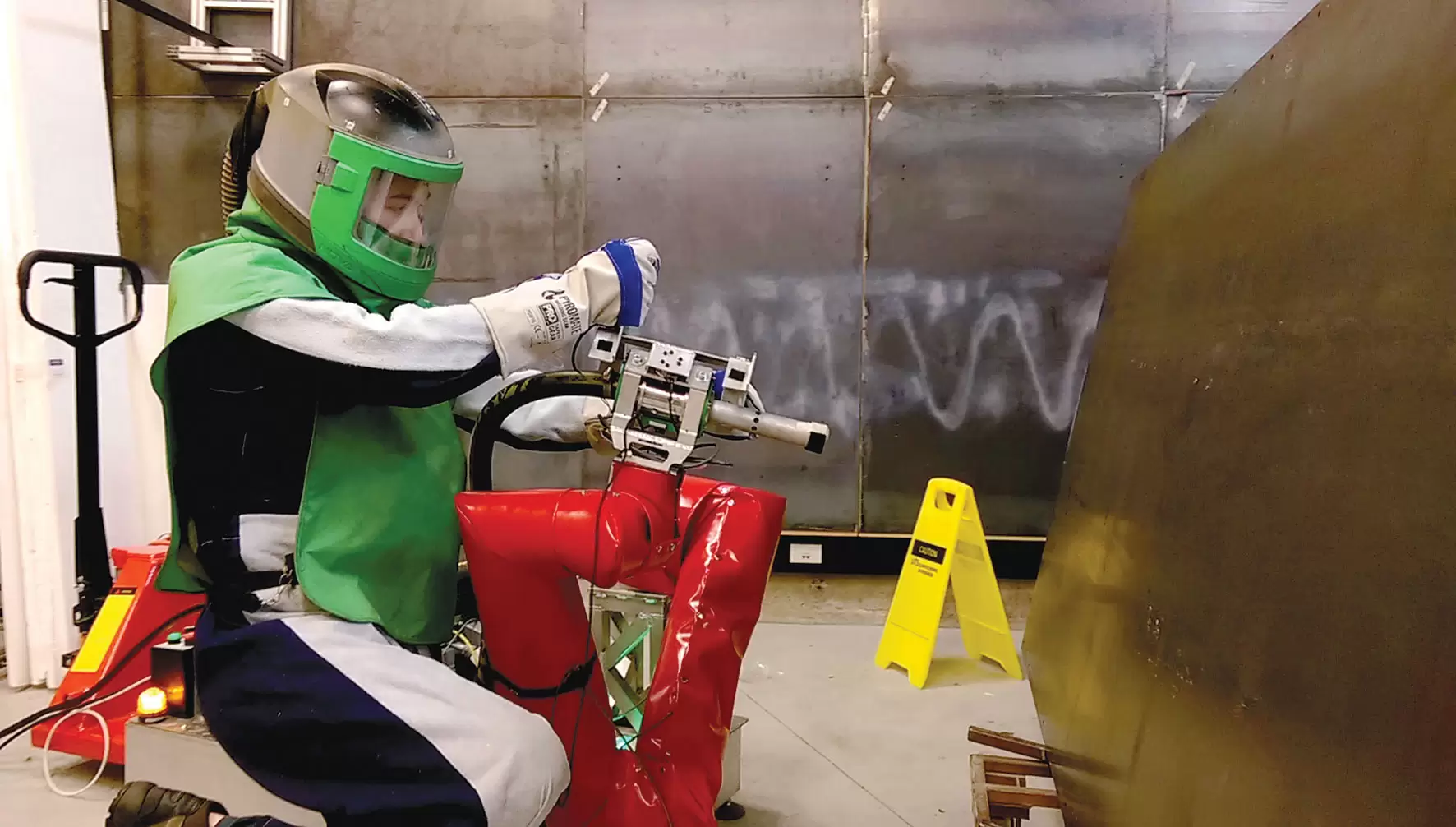
Assistance as needed
There have been numerous challenges to tackle with the ANBOT (Assistance as Needed roBOT). Research papers from CAS summarise these concerns as: “How much assistance is needed for an individual worker, how to provide the required assistance to a worker, what are the strategies for intuitive human-robot interaction, and how to ensure safety of human workers when they are in physical contact with robots?”
A challenge addressed early on was the reachable workspace. The robot and the user could only cooperate where their workspaces overlapped. But how should the robot behave when a person was taking the blaster to the edge of a workspace? How should the system discourage being moved into kinematic singularity, a problem when joints are asked to achieve impossible movements? A sudden stop would be unpleasant for the worker.
The answer was a damping method, which a paper explains as increasing “damping for motions towards singularity more than motions away from singularity.”
Besides control problems, the robot needed to be protected from particles created by blasting.
“A lot of the engineering challenge is just getting the robot to work in that environment,” said Carmichael.
Metallic dust, for example, can get in the robot if it’s not properly protected, causing short circuits. The UR10 is only IP54-rated off the shelf, so protective systems had to be designed.
Changing roles
Recently the project has led to fundamental research on role change, an interesting topic in robotics at the moment, said Carmichael. This will become more important as robotic assistance is increasingly adopted at worksites and other places.
CAS doctoral student Antony Tran has been researching this notion of role change, focusing on confidence cues. A machine might be able to guide the worker with blasting, for example, and in some situations could take control if it detects the need.
“In the past, there’s been mostly a focus on what a human’s confidence is in a robot. He’s been looking at the robot’s confidence in the human worker,” Carmichael said.
“What happens if the robot loses confidence and said, ‘Okay, I can see that you’re performing poorly or you’re doing the wrong thing’? Should the robot take over the task?”
Carmichael has been a lecturer at CAS since 2016 and has seen significant shifts in robotics research, even at this early stage in his career.
When he began his undergraduate study in 2002, UTS did not yet offer the mechatronics degree with which he ended up graduating. His PhD examined musculoskeletal models for assistance-as-needed robotics, work which overcomes a machine’s lack of empathy and allows it to provide the required amount of help to a person.
Carmichael sees a future of ubiquitous collaborative robots taking away an ever-larger share of repetitive tasks and working alongside us, ready to offer a helping end-effector. The world of human work will increasingly look to robots, and the world of robotic research will increasingly look to humans.
“One of the main contributions of my PhD work was using models of the human body instead of observing the performance of someone to then sort of predict beforehand how much assistance someone needs to do an activity,” he said.
“And this very much led me down the path of biomechanical engineering, musculo-skeletal models, very much non-robotic stuff which I wasn’t really prepared for, but I now find really fascinating. And, I mean, they’re becoming quite merged — as humans and robots operate more closely together, the robotic theory and theory about the human body are starting to become merged as well.”
Marc Carmichael was named one of create‘s Most Innovative Engineers for 2018. To register your interest in nominating yourself or someone else for 2019, click here.