An engineer at the University of Melbourne is driving research into sustainable, low-carbon alternatives to traditional concrete – here’s why that could prove revolutionary.
If calcined clay becomes a substitute for cement in concrete, as Dr Rackel San Nicolas believes it will, Australia will find itself blessed with over 500 years of raw materials.
“I strongly believe that in the near future, both Australia and the rest of the world will extensively adopt calcined clay as a substitute for cement,” San Nicolas, engineer and Senior Lecturer and Academic Leader of the Geopolymer and Minerals Processing Group at the University of Melbourne, told create.
Knowing that most of the carbon footprint of concrete comes from the manufacture of limestone-based cement, San Nicolas is currently driving research into what she refers to as the “greening of the concrete jungle” by creating better concrete.
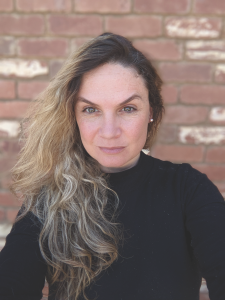
“This emerging calcined clay trend is not limited to developed regions like Europe and the United States,” she said. “Even developing countries such India and Africa are eager for a locally available alternative to cement.
“The widespread support from numerous researchers further reinforces the potential of calcined clay. And considering that clay is found abundantly worldwide and can be calcined with minimal CO2 impact, it presents a remarkable opportunity to create concrete.”
With the ongoing advancements in renewable energy sources, San Nicolas said, we may soon achieve zero emissions in the concrete production process as we remove limestone-based cement.
“The concept of excavating soil for building foundations and utilising that same soil to produce concrete for the construction is truly captivating to me.”
Coal industry waste
Just as spent brewers’ yeast is regularly recycled into another product of value – Vegemite – so too can coal industry waste be utilised as a vital ingredient in the production of concrete.
The research San Nicolas has been conducting is looking into how fly ash can not only be recycled into concrete as a cement alternative, but can also replace concrete’s most environmentally dangerous ingredient.
“Cement represents eight per cent of global carbon emissions,” San Nicolas said. “You can make sustainable concrete in different ways, but at the core it’s about reducing the amount of Portland cement used.
“The main approach I’ve been using is to utilise different waste materials like fly ash or slag, or different processed material like calcined clay, that have a much lower CO2 footprint.”
A transition to what is known as geopolymer concrete, San Nicolas said, would be relatively simple in Australia as there is already a stockpile of over 400 million tonnes of fly ash from Australia’s coal industry. Around 30 per cent of this stockpile is of appropriate quality for use in concrete.
However, as the coal industry is wound down and cleaner energy generation methods are adopted, the supply of fly ash will not be constant. But in the ground we have over 500 years supply of clay that can be calcined, San Nicolas explained.
The big hurdle
Cement-free concrete, and concrete with 50 per cent cement, is available in the market right now. It might be used for retaining walls or other less structurally important projects. But confidence is yet to be built in products engineers can design with.
“It’s a very big hurdle for engineers and project designers to build confidence in these materials,” San Nicolas said.
“But more suppliers are saying that by the end of this year they will have concrete we can design with, and we will have more full-scale trials and data around their durability.”
It’s those trials, and the possibilities they will create, that truly excite San Nicolas. Excavated foundation clay being used to create cement for concrete for the building that then sits on that foundation is the ultimate goal. It’s one that could revolutionise construction and engineering around the globe, and particularly in Australia.
“Finding greener, more sustainable solutions to make our most common building material has the potential to immensely reduce global emissions,” San Nicolas said. “It is important that engineers, designers and researchers work together to prioritise low-emission, locally sourced feedstock and waste materials to be used in current concrete applications.”
Great subject would love to hear more