Nothing lasts forever, even in construction. When a building is torn down, the result is usually a lot of rubble sent to landfill. This expert says it doesn’t have to be that way.
Joe Karten, Head of Sustainability and Social Impact at construction firm Built, wants engineers to begin planning a project’s afterlife from the moment of its conception.
“We design buildings to be put up once and stay there forever, but we know buildings don’t last forever,” he told create.

“However, their components can have a much longer useful life than the buildings themselves if they’re designed properly and if you know that consideration for disassembly is taken at the very beginning.”
Designing for disassembly delivers circular economy gains that boost the sustainability of often carbon-intensive construction projects, but it also provides financial benefits.
“We’re going to spend $200 million on a building,” Karten marvelled, “then we’re going to pay somebody money to smash it up and get rid of it?”
Buildings should be seen, he said, as if they were one of Swedish furniture retailer Ikea’s dressers or shelf units, which are made from standardised parts and can be disassembled and reassembled at will.
Read more: Circular construction involves designing for multiple lifetimes
Step 1: Involve clients and contractors
With this in mind, Karten decided to collaborate with circular economy consultant Coreo and produce what he described as “an Ikea manual in reverse”: a template engineers can use to create building disassembly plans of their own.
“We want our competitors, our clients, our subcontractors, our supply chain partners – everyone – to take these documents, put their logos on them, adjust them, modify them and use them,” he said.
The template was inspired by a Built client who wanted a site office that would only be used for five years. That presented an opportunity for Karten’s team to think about what needed to go into a design-for-disassembly plan.
Karten advises first looking at each of the components to be delivered by each contractor – the structure, the facade, the internal finishes, the services – and understanding how those fit into the disassembly process.
“For each of them, there are considerations around the materials they’re using, how those materials connect into each other, and how they’ve been designed to enable future disassembly and reuse elsewhere,” Karten said.
“Each of those subcontractors got a questionnaire. They would comment on things to be aware of for second-life reuse: how to store the materials to prevent damage after disassembling; the electrical scope had information around looking for frayed wires and not using them [and to] get the wiring or cabling tested and tagged again before reusing.”
Step 2: Start as soon as possible
When designing for disassembly, Karten cautioned, it’s best to begin the process early. At the typical point a consultant might start pricing a job, complexities could already have been introduced that will make the process harder.
Engineers should look at such aspects as using mechanical reversible connectors, modular design, layer separation, avoiding toxic materials and using homogenous materials in favour of composites.
“A key consideration would be designing access for disassembly. We can disassemble an element within the building, but if the element is so big that it doesn’t fit in a lift or even a goods lift, how do we get it out of the building? You might have to design a whole column of facade panels to pop out so that you can remove components of the building through the facade at a later stage.”
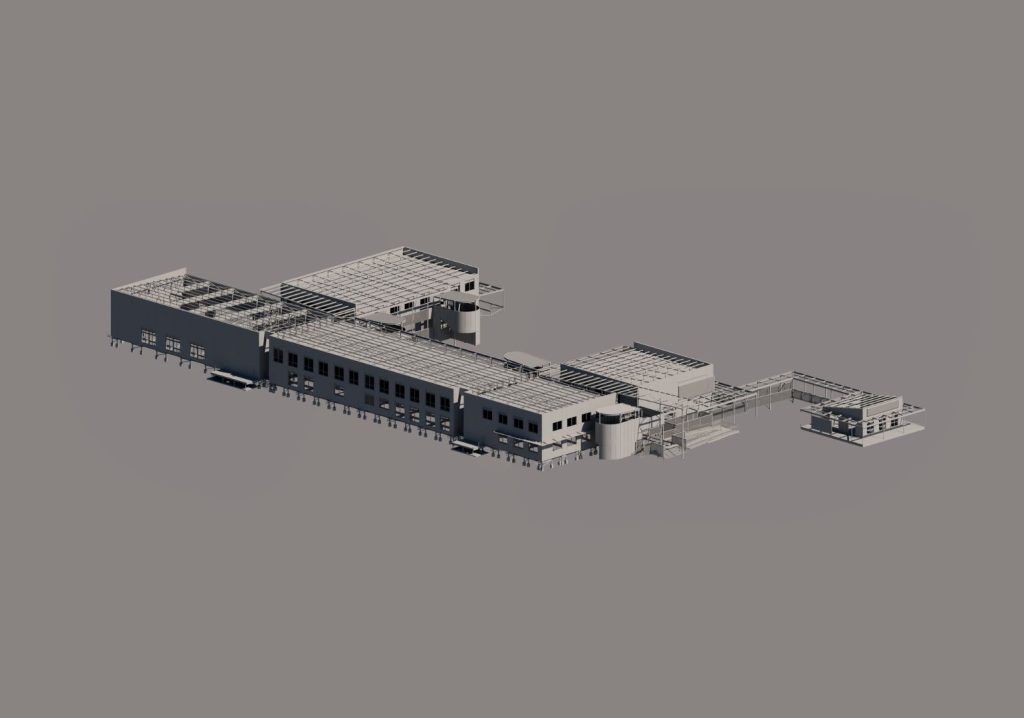
When Karten applies his template, he incorporates it into a digital twin.
“Built uses the digital model throughout design to allow the project team to visualise the elements being assembled in three dimensions in order to detect clashes, streamline coordination, and have the opportunity to design with disassembly in mind,” he said.
“Before coming to a site to disassemble an element, a user will be able to use the model to check the connections and determine what tools would be needed to complete the task.”
By breaking down the building’s components in such a manner, engineers can understand exactly where the reusable elements need to go, which elements they don’t plan to reuse, and, if they have a product stewardship agreement with the manufacturer, which ones can be returned for refurbishment, reuse or recycling.
“Then it’s all about working out how you can minimise double handling. If we’re paying somebody to disassemble, warehouse and then reassemble, we’re potentially doubling up on costs.”
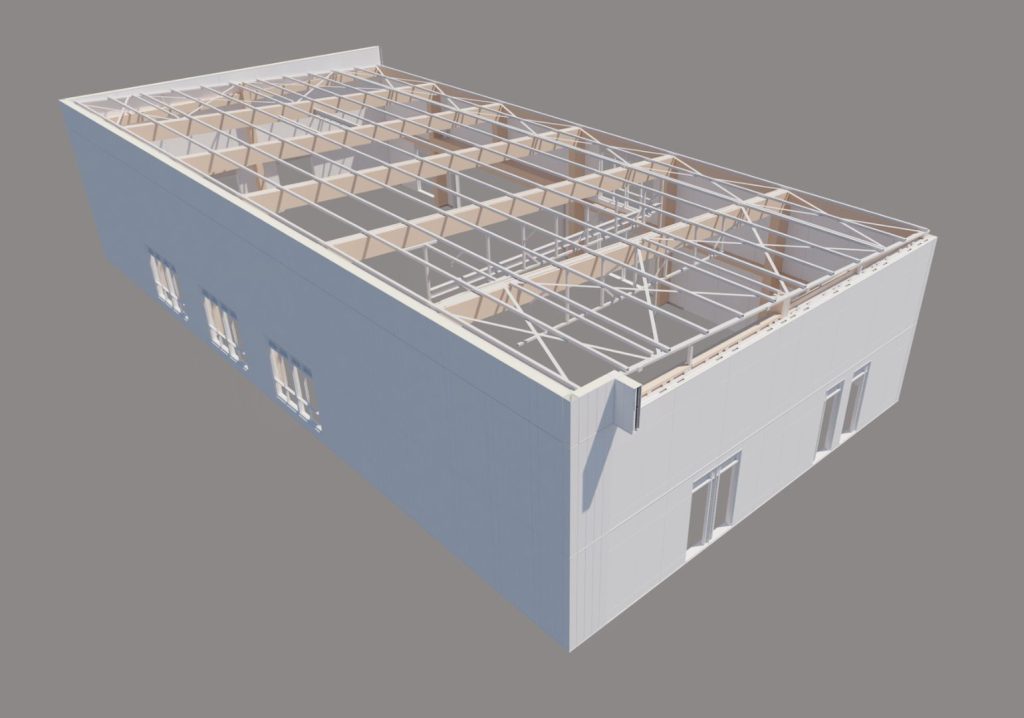
Step 3: It’s never too late
Even if a project hasn’t been designed for disassembly, Karten said it’s never too late to integrate an element of disassembly. Built’s Perth office is an example.
“The design manager on the job said they’ll look at the joinery – we can design that for disassembly. They used a screwed, not glued, methodology, and they put that together and got a cadet on the job to fill out a 60-page joinery disassembly plan.”
That took place well past the concept stage, Karten said.
“Any element that is delivered as modular, with reversible connections – a piece that can be extracted at the end-of-life – represents financial value for the owner. It represents an element of that building that can be on-sold or reused, rather than the owner having to pay to demolish it.”
Successfully completing projects starts with effective early project planning. Learn more at this Engineers Australia event.