Tools that have been printed using lasers could be just the ticket for tough machining jobs in defence, aerospace, and other industries.
A young engineer’s research on additively manufactured end-mills has earned him the Young Defence Innovator Award at this year’s Australian International Airshow.
The work has been carried out in collaboration with Sutton Tools, and supported by the Defence Materials Technology Centre.
Jimmy Toton, a PhD candidate in Mechanical and Manufacturing Engineering at RMIT University, believes there is a lot of potential in such tools for high-value, low batch applications where metals such as titanium and nickel-based alloys are involved.
To prove it, Toton headed back to university after two years as an R&D Test Engineer at Sutton Tools.
“During my time as an R&D Test Engineer — and like some engineers — I fell in love with the idea of additive manufacturing” he told create.
“I saw an opportunity to apply metal additive manufacturing specifically to custom cutting tool manufacture, for advanced manufacturing. Obviously, it’s not going to [pass] a cost-benefit analysis for DIY work and things like that, but [could] for your difficult-to-machine materials used for complex components in automotive, aerospace, defence and power generation.”
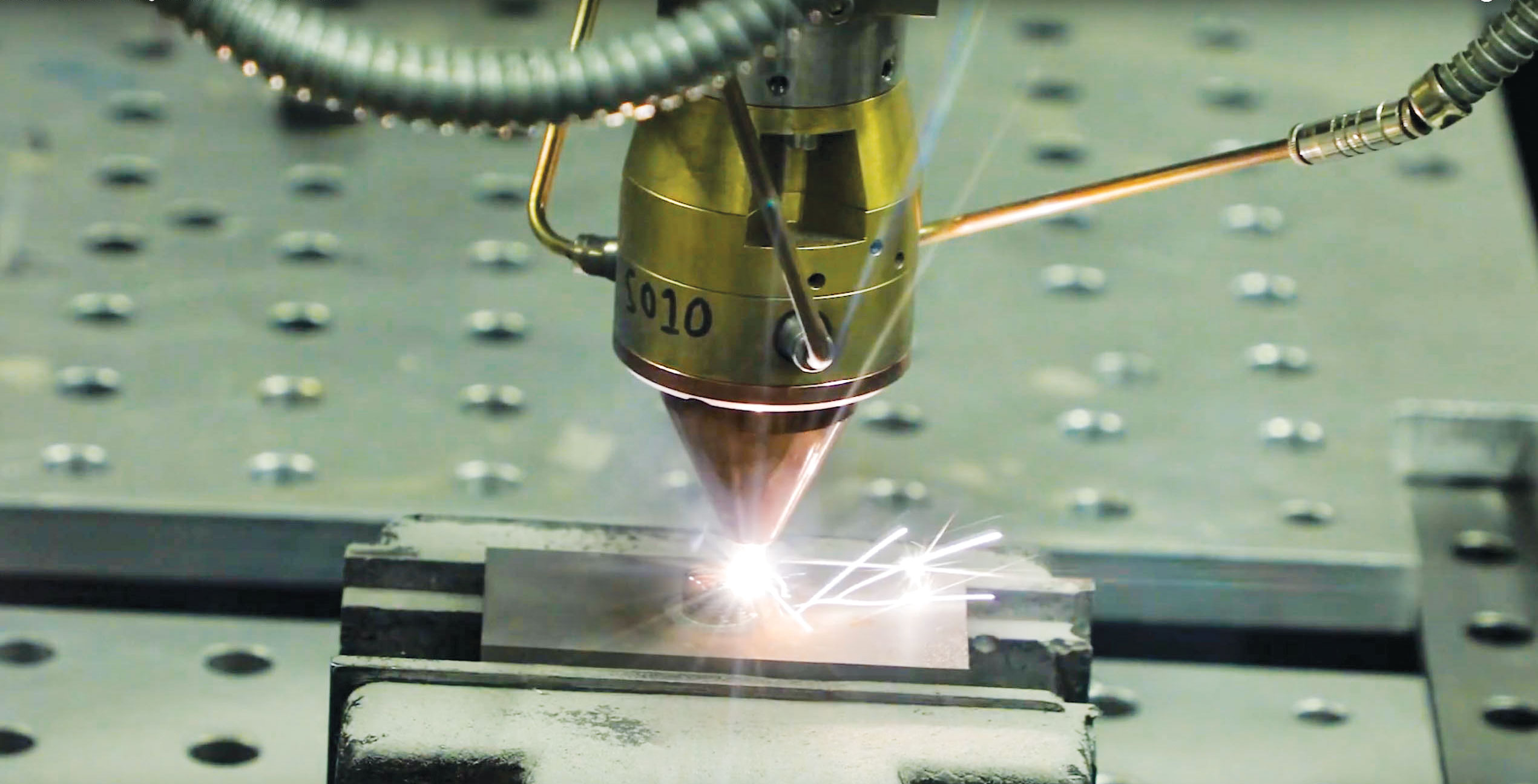
Toton started looking for alloys that would bridge the gap between high speed steel and tungsten carbide. They needed to have high hot hardness and good resistance to thermal softening.
He narrowed his search down to two alloys, both already known but still reasonably exotic in terms of commercial use: Fe-C-Cr-Nb-B-Mo (FCCNBM) and Fe-Co-Mo (FCM).
“I was able to very quickly produce a product with the [FCCNBM], and yes, it worked, it did function and that was great, but it didn’t perform well,” Toton said.
“Conventional high-performance, high-speed steels were outperforming it.”
FCM, a maraging steel, was the winner of the two. It is manufactured using conventional powder metallurgy manufacturing. A custom supply had to be ordered from Höganäs in Sweden.
Toton used laser metal deposition (LMD), a blown powder approach that is used for applications including cladding and remanufacture as well as 3D printing, to build coupons before scaling this up to cylindrical bar.
RMIT’s Advanced Manufacturing Precinct boasts a Trumpf 5-axis laser-machining centre, which is able to cut and weld as well as print.
LMD is a mature technology and can produce parts with small amounts of powder. It’s a reason why researchers dealing with a new alloy design or an expensive material will start with LMD.
The approach requires heat treatment after printing but has the advantage of cutting out solution treatment, which is required in the powder metallurgy-produced steel, Toton said.
“That’s where you heat your samples high enough, for this particular material, in the gamma region, where the other crystal phase high in molybdenum will dissolve into the Fe-Co matrix, super-saturating it with molybdenum,” he explained.
“Once the matrix is saturated to a desired level you then rapidly cool, trapping the molybdenum in solid solution. The thing is, the additive manufacturing process naturally does that anyway as you build.”
This was followed by age hardening, where the steel reached its final hardness of between 850-950 Vickers, depending on the holding time and temperature.
After that, the bars were ground into end-mills, and slotted into the manufacturing process at Sutton Tools, which produces tonnes of products per year out of bars. This was the reason why it was chosen to print cylindrical bars.
End-mills were used as a testing vehicle to validate and characterise the performance in a machining laboratory setting.
TI64 (an alloy of titanium, aluminium and vanadium), the most common titanium-based alloy in industrial use, was used as the workpiece.
Compared to commercially available, powder metallurgy-based FCM end-mills, the printed variety performed equally as well in two tests and was superior in another.
The next steps are to determine process parameter ranges capable of producing the right microstructure in printed parts, then establish the right heat treatment process while simultaneously designing novel through coolant channel designs.
The powder is yours
Toton’s next step is to transfer the intellectual property developed for LMD to selective laser-melting additive manufacture, which is a ‘powder bed’ rather than ‘powder-fed’ approach.
The design complexity available through this type of laser melting will give productivity gains by designing optimised through-coolant channels for tools.
“I wasn’t focusing on design complexity in this project; I wanted to develop a process that is capable of producing a microstructure with the right mechanical and wear properties necessary in metal cutting,” Toton said.
This article originally appeared as “Additive precision” in the June 2019 issue of create magazine.