Robotics teams are using Darwinian theory to develop the next generation of artificial intelligence.
Charles Darwin’s theory of evolution proposed that physical or behavioural traits that benefit a species would be passed on to the next generation in a survival of the fittest.
While this theory has widely been applied to humans and animals, researchers now believe a level-based approach that lets them use materials and 3D printing to its fullest effect could be used to develop next-generation robots.
In a paper published in Nature Machine Intelligence, CSIRO’s Active Integrated Matter Future Science Platform said that more effective designs could be achieved if robots took their engineering cues from evolution.
This concept, known as multi-level evolution, responds to the struggle experienced in unstructured, complex environments by robots that aren’t specialised enough. If the robots emulated the evolutionary adaptations of animals and plants, they could survive better in their environment.
David Howard, lead author of the paper and senior research scientist in the Robotics and Autonomous Systems Group, said that technologies such as high-throughput materials discovery and characterisation, advanced manufacturing, or artificial intelligence could allow robots to be designed from the material level up.
This would let them perform in extremely challenging situations, like space or the deep sea.
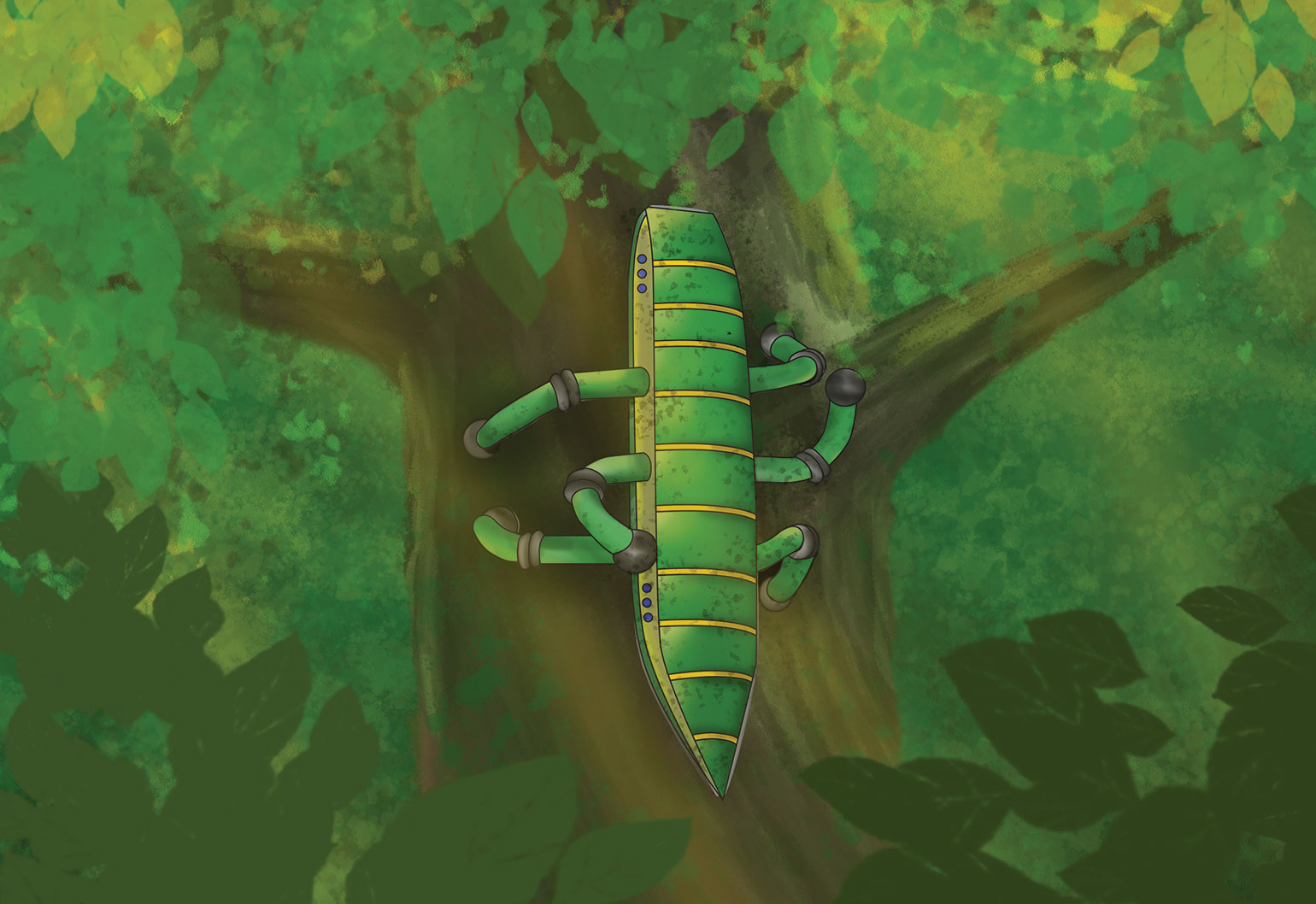
“We can effectively design an entire robot — its shape, the type of sensors that it has, the types of actuators that it has and how they’re placed, and even down to the materials that the robot’s made from,” Howard said.
An evolutionary approach would allow the robot to be designed automatically by combining materials, components, sensors and behaviours.
“The idea is that we can employ algorithms inspired by evolution to help engineers and designers to search what we call high-dimensional search problems where we’re looking at an entire robot and its performance in the environment,” Howard said.
The team hopes that, one day, a press of a button would start a multi-level evolution algorithm designing tailor-made robots.
Highly evolved
Howard said it would take about five years for a bare-bones instantiation that proves all of the concepts, and, in about a decade, multi-level evolution (MLE) systems would be able to generate robots for a constrained real-world mission.
“But to create a fully autonomous MLE system, we’d be looking at in excess of maybe 20 years where the algorithms are smart enough that they know how to constrain themselves properly,” he said.
This article originally appeared as “Unnatural selection” in the June 2019 issue of create magazine.