The energy-to-weight ratio that makes for efficient air travel means aviation is one of the hardest-to-abate sectors. So how does the sector reduce its reliance on jet fuel and decarbonise?
This article was originally published in the August 2024 issue of create with the headline ‘Ready for take-off?’.
Perched on its own continent, half composed of first- or second-generation migrants, Australia is hugely dependent on aviation, both economically and socially.
With Australians among the world’s most frequent long-haul fliers, we have a large stake in the success or otherwise of rapidly decarbonising aviation, one of the hardest industries to abate. The challenges are many, but so there are many engineering attempts to overcome them.
Already, aviation accounts for about four per cent of global warming. But that share is expected to swell rapidly as other sectors decarbonise. In fact, given projected growth in air travel, by 2050 aviation could represent up to 22 per cent of global emissions, according to Deloitte.
While the rise of battery-electric aircraft means the pathway to zero-emission short-haul commercial flights is visible, the unforgiving energy-to-weight ratios that long-haul passenger flight demands mean major engineering ingenuity is needed.
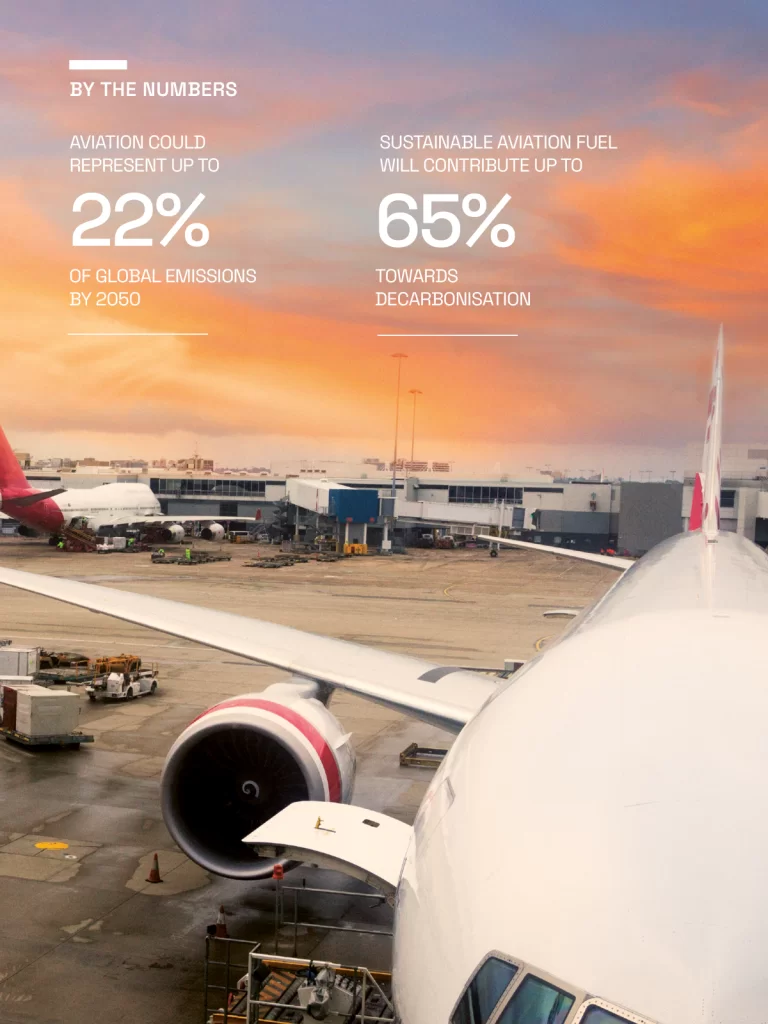
Global aviation decarbonisation efforts are guided by the International Air Transport Association (IATA) net zero roadmap, which lays out the critical actions needed across aircraft technology, energy infrastructure, operations, finance and policy.
Their current modelling suggests sustainable aviation fuel (SAF) will account for the lion’s share – two thirds – of the emissions cut. Offsets and carbon capture are predicted to account for a further 19 per cent, and new electric and hydrogen technologies 13 per cent, with savings from infrastructure and operational efficiencies.
The role of design
While it’s technically challenging, we’ll likely see engineers innovating in this space with new and inventive forms of transport such as electric vertical take-off and landing aircraft (eVOTLs), said Damian Ogden CompIEAust, pilot and Group Executive of Policy and Public Affairs at Engineers Australia, which this year made a submission to the Australian government’s Aviation White Paper.

“We can’t underestimate the importance of innovation in aircraft design, such as using lighter materials like composites and improving aerodynamics, to reduce fuel burn and support sustainable aviation goals,” Ogden told create.
Decarbonising aviation will require significant innovation and retooling of fuel sources, engine technology and aircraft, particularly when it comes to long-haul flights and freight aviation where weight, fuel volume and engine power are critical factors.
“It will take a multi-faceted approach that needs policy advocacy, government, technological advancements and collaboration between industry leaders, government agencies and the community.”
Non-petroleum fuels
SAF is a non-petroleum fuel derived from alternative feedstock such as cooking oil, plant oils, municipal waste, waste gases and agricultural residues. To be sustainable, it needs to use raw materials to avoid depleting natural resources, although not all of the relevant feedstock sources are available in abundance.
SAF offers enormous economic potential to Australian industry, given the country’s agricultural strengths and proximity to major transport hubs. However, it is still prohibitively expensive compared to fossil fuels and consensus is needed on global sustainability standards for feedstocks.
It is produced through a number of different pathways such as converting woody biomass using gasification, hydroprocessing fatty acids in oil-based material or fermented sugars in cellulosic biomass, and processing other biomass or fats and oils.
SAF has lower carbon dioxide emissions across its lifespan than conventional jet fuel because the emissions produced when the fuel is burned in a combustion engine are offset by the carbon dioxide absorbed by plants during the growth of biomass.
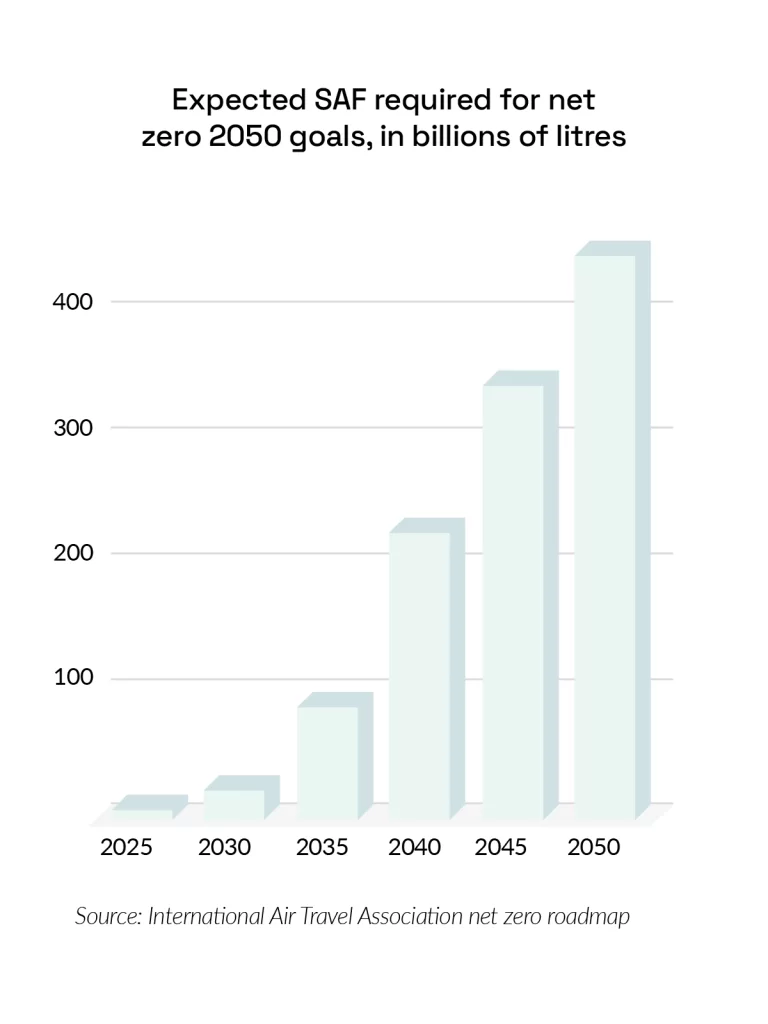
Although there are emissions from producing SAF, depending on feedstock and production, carbon dioxide emissions can be up to 94 per cent lower overall using this alternative fuel source. However, there is a range of challenges involved in scaling SAF production.
The cost to stand up each new production facility is prohibitively high and SAF is currently two to five times more expensive than jet fuel. Worldwide production needs to scale and requires a greater diversity of feedstock to meet future demand.
“There is a limit to how much can be produced from used cooking oil and tallow, so more research is needed into sustainable oil crops,” said Heidi Hauf, Chair of GreenSkies and former Asia-Pacific Sustainability Lead at Boeing.
While each production pathway needs to be certified under the International Fuel Standard, it opens up more avenues for feedstock options, and this is where Australia is looking to join the global efforts to ramp up SAF production.

New pathways allow regionally specific feedstocks to be converted to SAF, which would benefit Australian production as it can account for our unique conditions, according to Hauf.
“International alignment on sustainability standards is important, but Australian conditions need consideration due to our different farming practises,” she said. “We have had to work on our water consumption more than other parts of the world so we often have crops that are much lower in water usage.”
Australia also needs to consider the available bioresources, and weigh up the potential of synthetic fuels and how these resources are allocated to other industries. Bioresources are used to create renewable energy, but there are alternatives to make renewable energy, and we don’t have alternatives to make renewable liquid fuels, Hauf noted.
“We can’t meet all our jet fuel needs this way, but feedstocks should be prioritised for highest-need applications such as liquid fuels over uses like energy generation,” she said.
The bigger challenge might be the scale of current jet fuel appetites. SAF consumption rose from approximately 19 million L in 2021 to 93 million L in 2023, according to the Environmental Protection Agency.
To reach net zero by 2050, the IATA estimates the aviation industry would need 449 billion L of SAF – meaning production needs to scale more than 4800-fold within 25 years.
A report earlier this year from the UK’s Royal Society estimated that fuelling all UK-based airliners with SAF derived from locally grown rapeseed, for example, would require more than two-thirds of the country’s agricultural land to be converted into feedstock production.
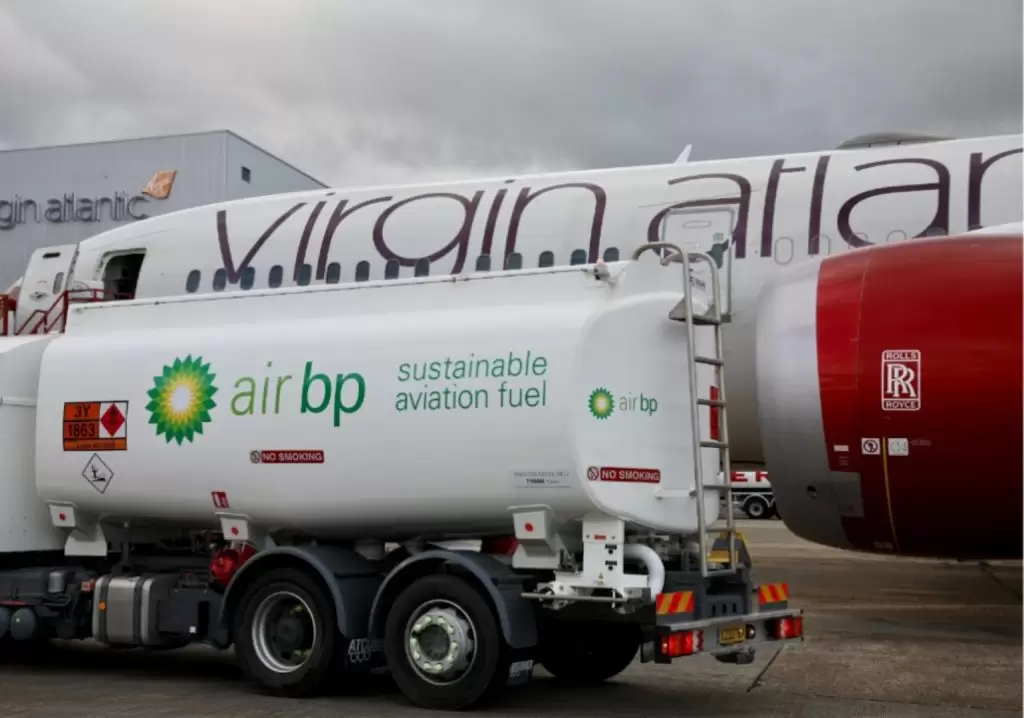
Battery-electric
Battery-electric aircraft are operating today thanks to advancements in battery technology and electric propulsion, making them viable for short flights. There are fixed-wing planes and eVTOL aircraft, which are suited to flights within and between cities because they can operate in confined spaces such as rooftops or dedicated vertiports.

But there are significant challenges, with energy density and weight limitations for long-haul passenger aviation because a suitable battery to power aircraft across those distances would be prohibitively heavy. Battery technology enabling high-energy density and fast recharging suitable for long flights is still some way off.
“Incremental improvements are needed to balance energy density, fast-recharging capability and lifespan,” said Andrew Moore, co-founder and Chief Engineering Officer of AMSL Aero, an Australian company pioneering hydrogen-powered electric aircraft.
There’s also the problem of preventing issues such as dendrite growth that degrade battery performance over time, and of optimising for aviation needs.
“A battery must combine high-energy density with high-power density to meet the power demands of take-off while also providing sufficient energy for long flights,” Moore said.
Hydrogen-powered
From the Wright brothers onwards, aviation has faced the challenge of delivering maximum energy from the least weight. To this end, hydrogen’s energy-per-unit mass – three times higher than traditional jet fuel – makes it an attractive alternative for decarbonising long-haul aviation.
It can be combusted through modified gas-turbine engines or converted into electrical power to complement the gas turbine via fuel cells. The two approaches can also be combined.
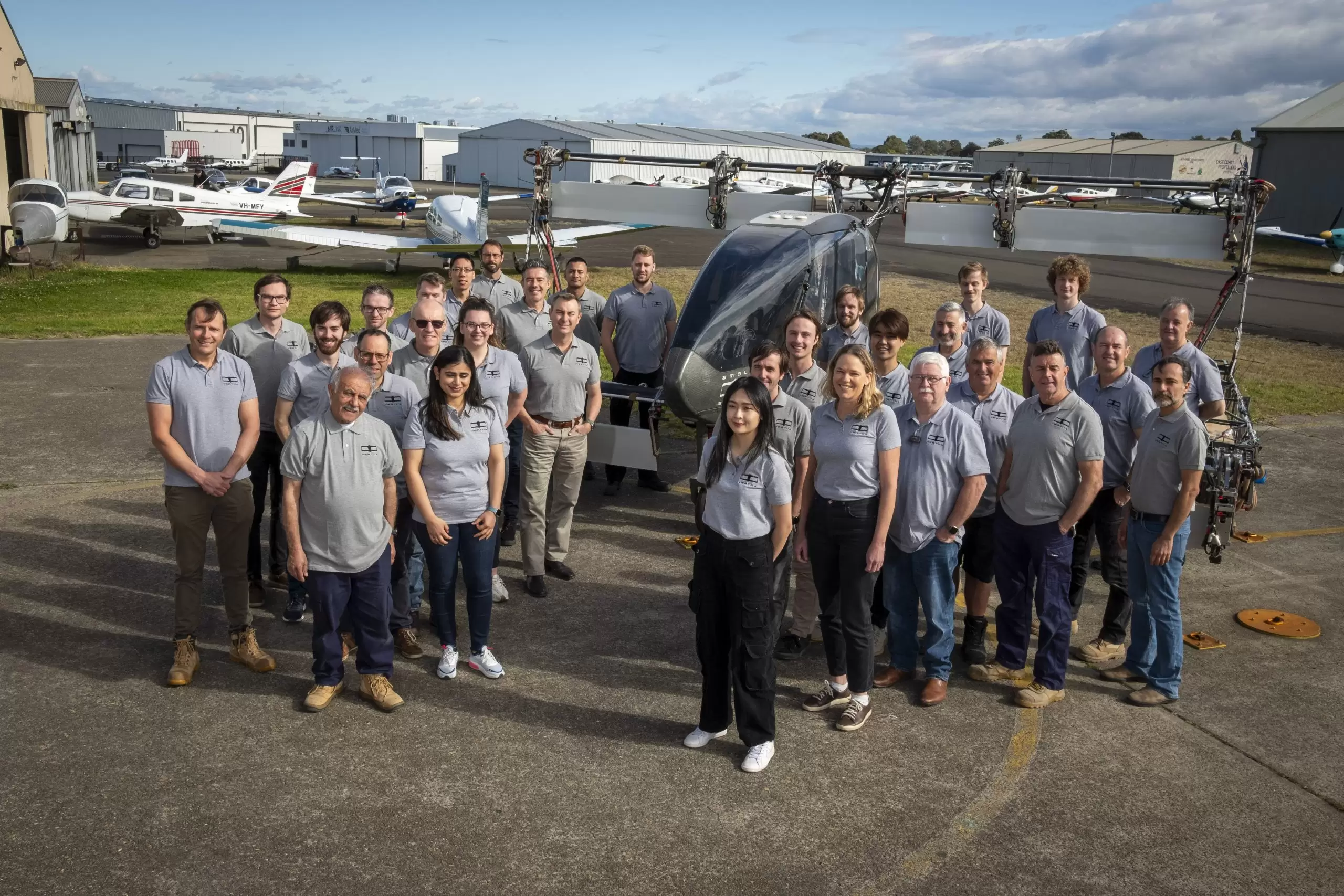
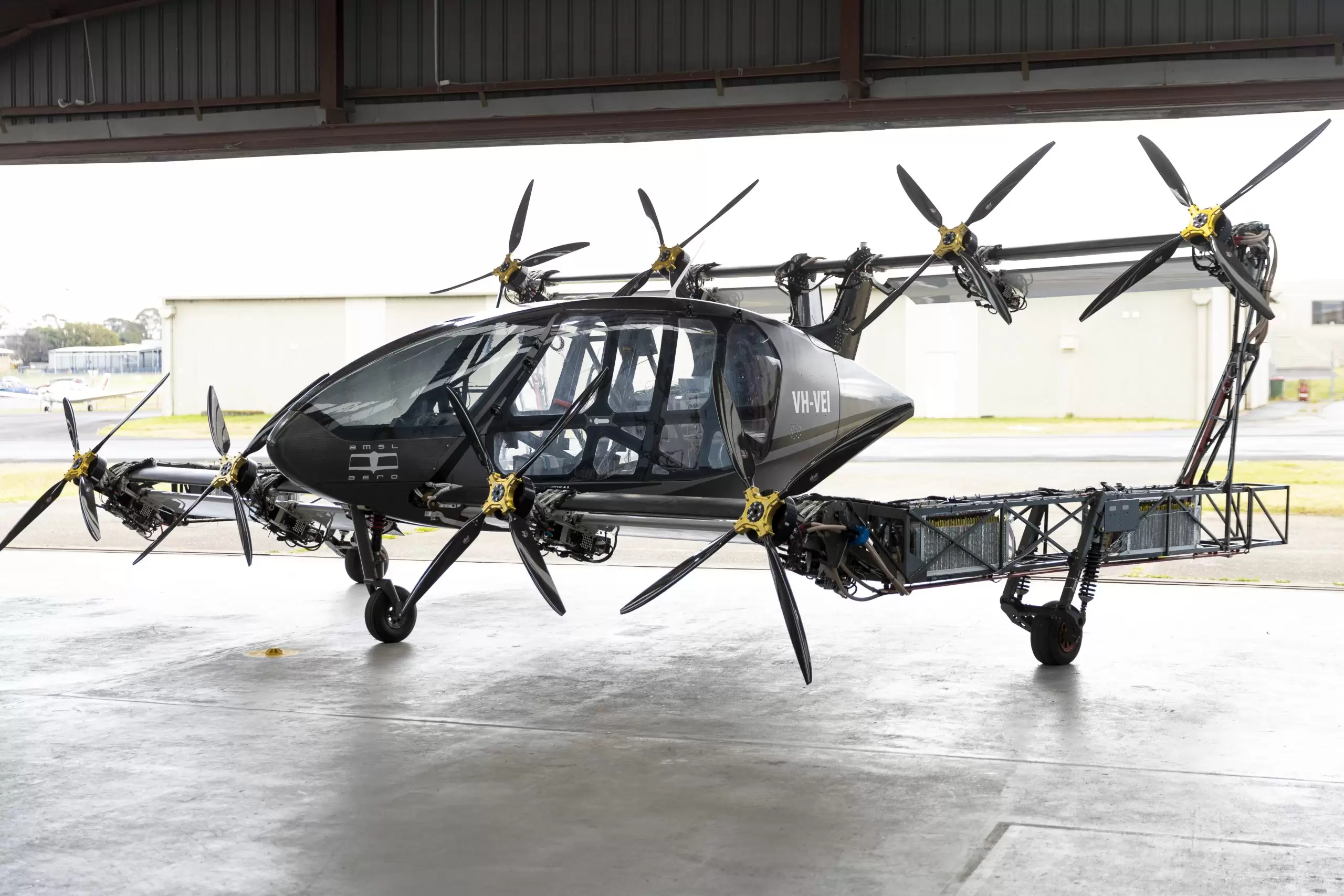
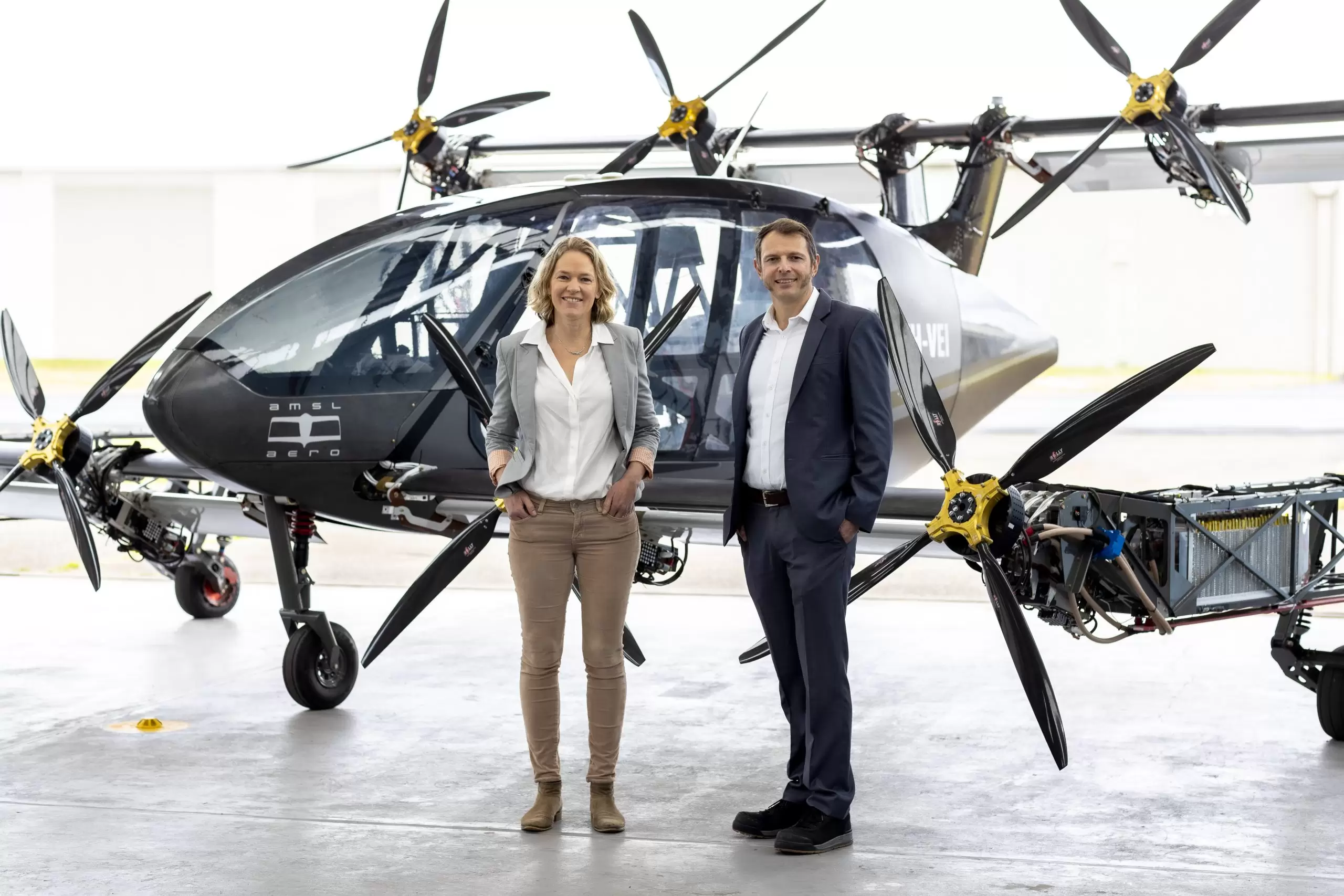
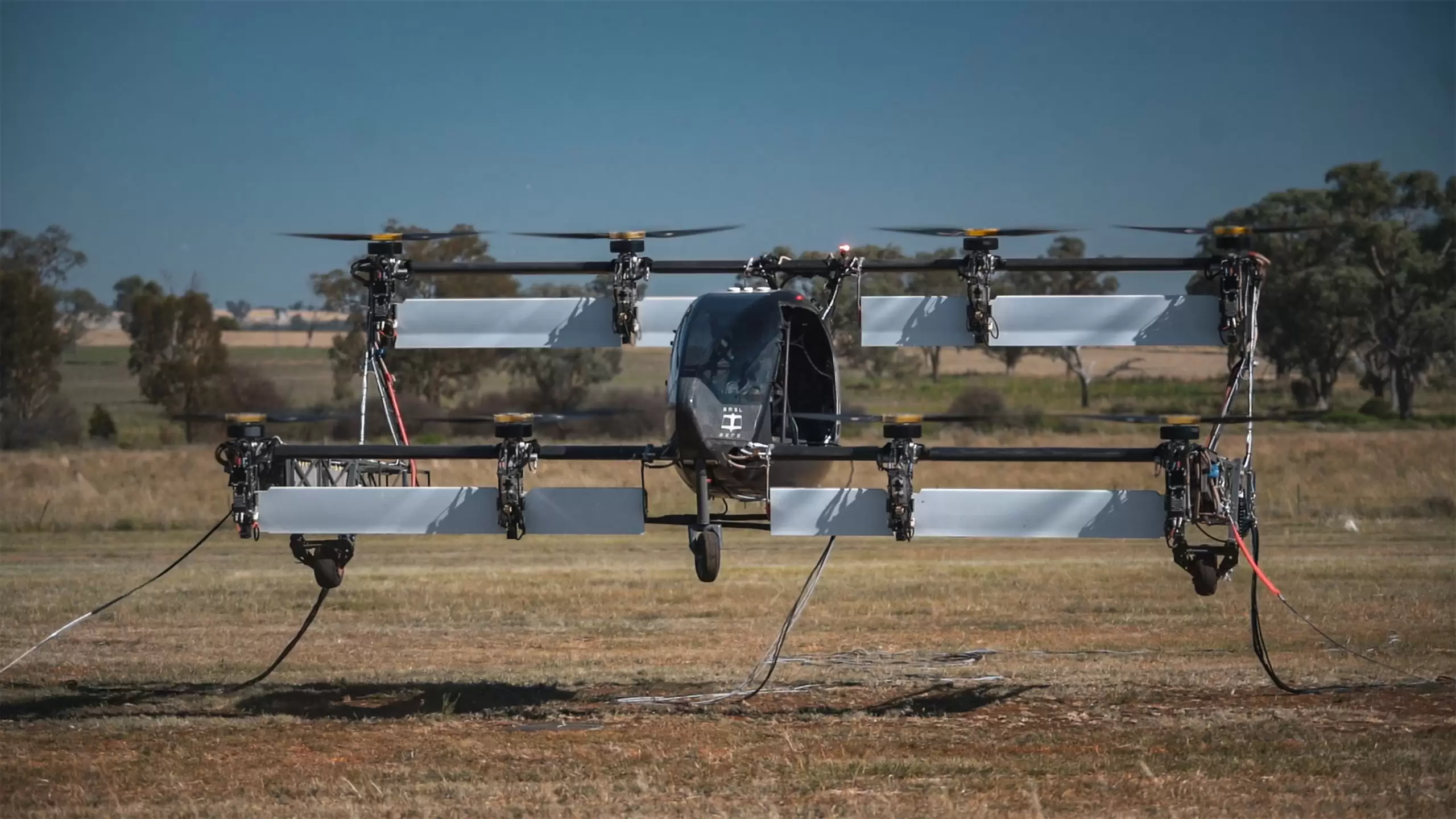
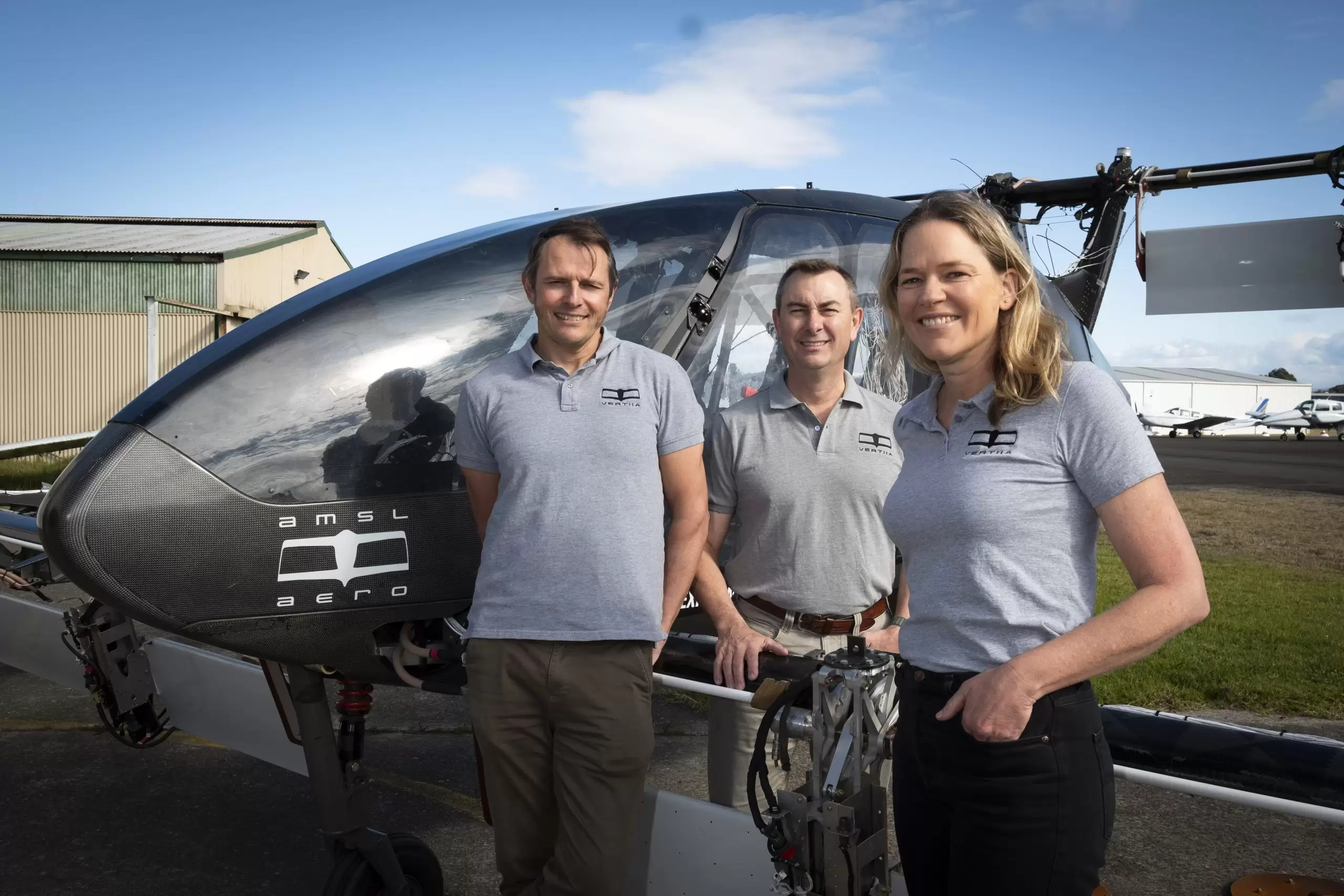
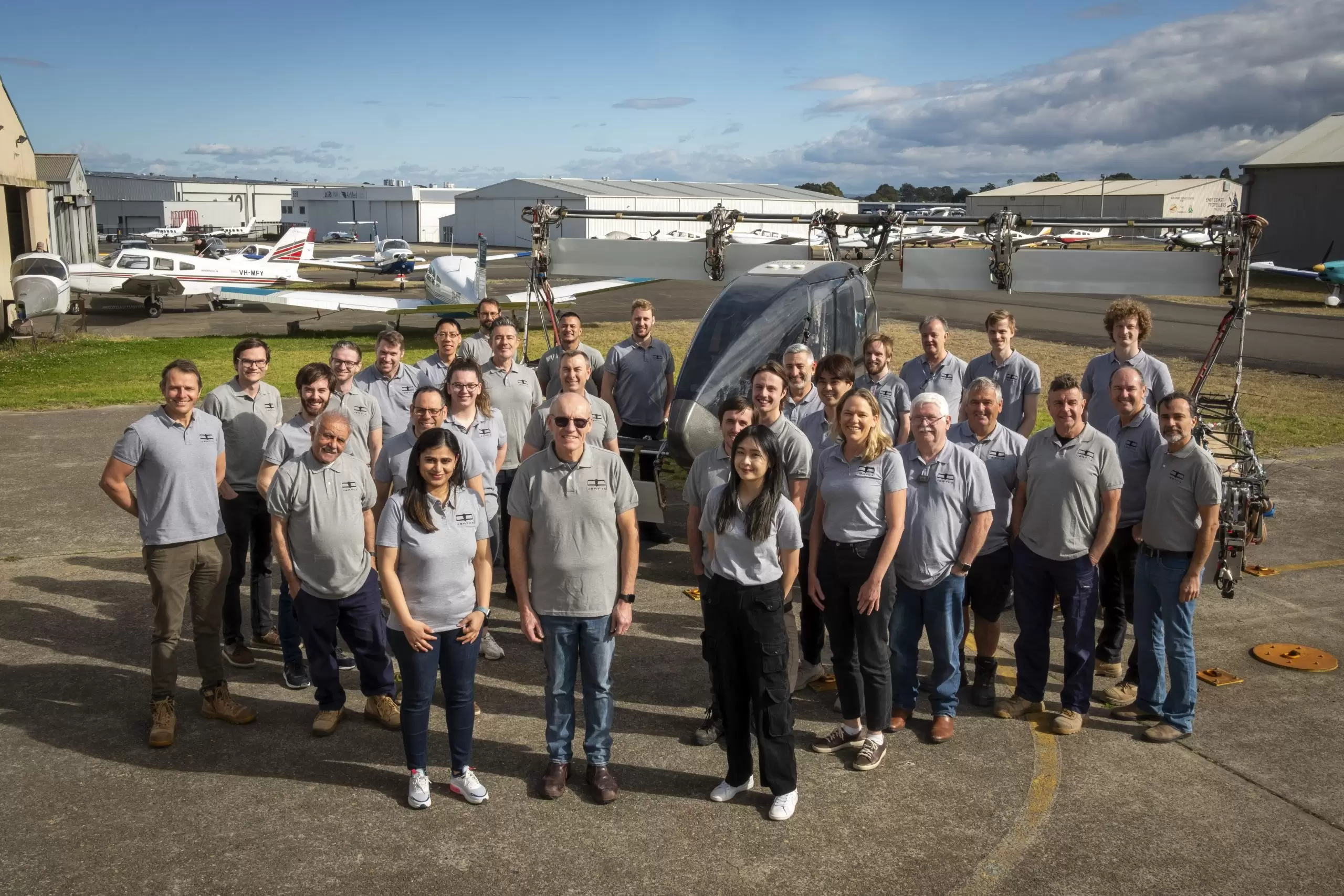
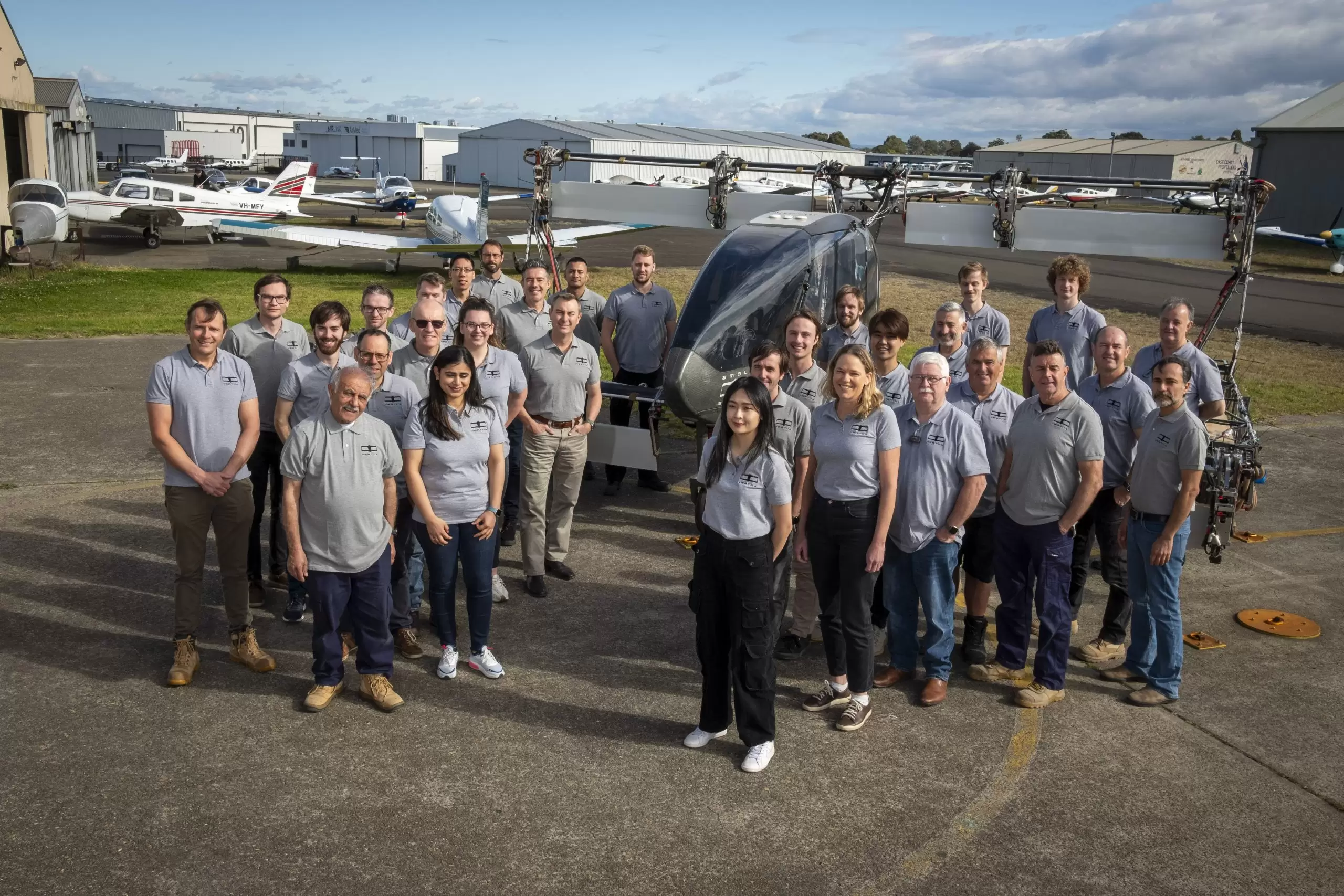
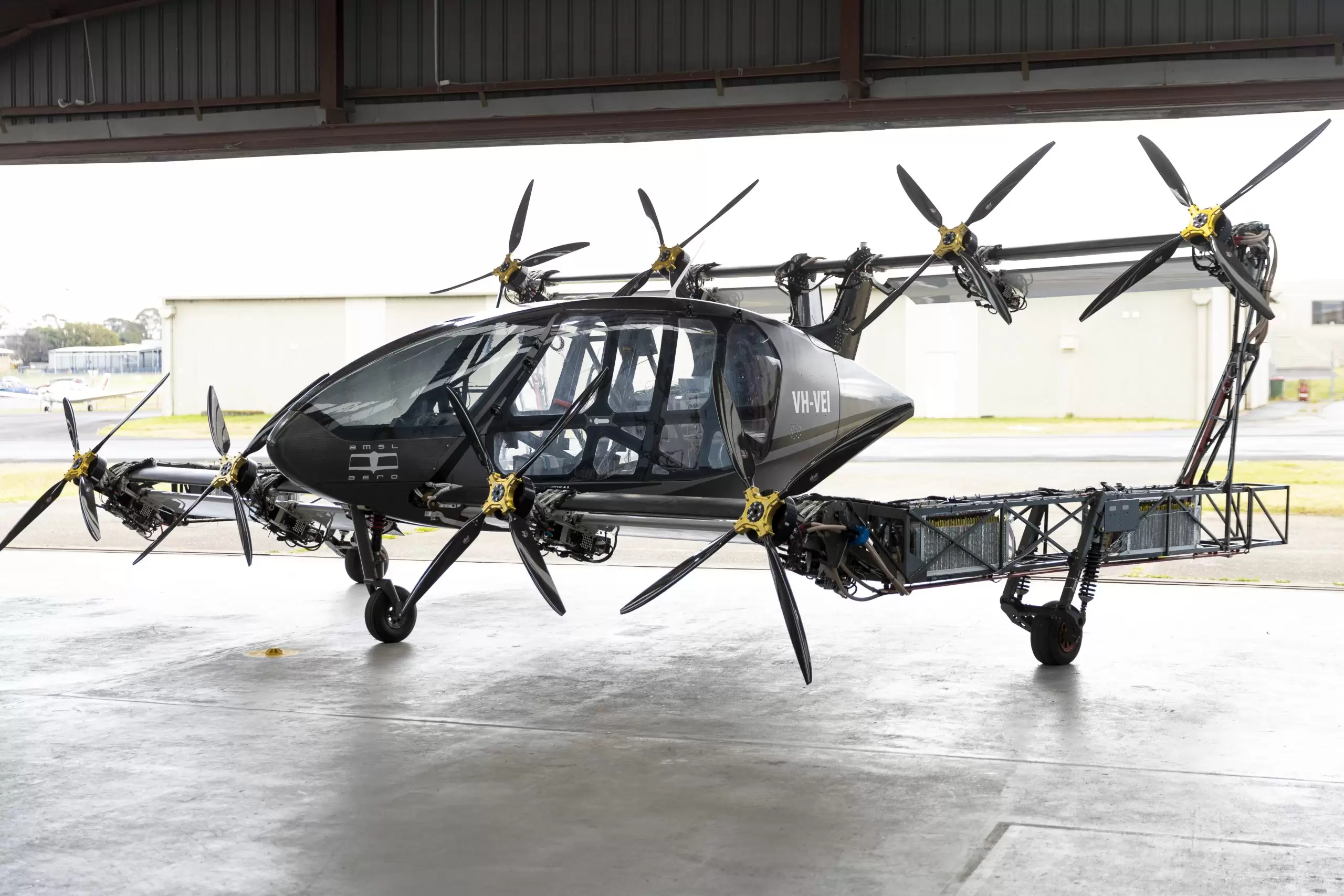
To be usable, the hydrogen must be compressed and stored in suitable high-pressure vessels, with compatible refuelling trucks handling the high-pressure refuelling of the aircraft.
“With gas hydrogen, it can be compressed to a high volume, however the mass of the tanks is very high and requires aircraft to be redesigned as it’s much harder to retrofit existing aircraft,” Moore said.
By contrast, liquid hydrogen has less volume and is lighter because it’s stored at lower pressures, but it requires very low temperatures and isn’t in abundance locally.
“In Australia, access to liquid hydrogen is one of the biggest challenges as there are only two hydrogen production plants in the country.”
Hydrogen fuel cells offer a viable technology for medium-range aircraft applications up to around 2000-3000 km in the near term. Progress has been made clearing some of the hurdles in bringing them to reality.
“There are still challenges with cryogenic storage of liquid hydrogen on aircraft and integration with fuel cells, but these issues are close to being solved,” Moore said.
As well as AMSL Aero, there are several local groups working on hydrogen-powered aircraft, such as Aviation H2, and Stralis Aircraft in partnership with the Queensland University of Technology and iMOVE CRC.

Watching the skies
The reality is that there will be no single solution for abating emissions from long-haul flights.
Instead, progress will come not just from breakthroughs and advances in engineering fields as diverse as aeronautical, chemical, electrical and agricultural, but from the ability of these fields to work together to craft new systems for long-haul aviation.