Engineers from the University of New South Wales (UNSW) have successfully converted a diesel engine to run as a hydrogen-diesel hybrid engine – reducing CO2 emissions by more than 85 per cent in the process.
The Hydrogen-Diesel Direct Injection Dual-Fuel System developed by the team enables a traditional diesel engine to be retrofitted.
The team, led by Professor Shawn Kook from the School of Mechanical and Manufacturing Engineering, spent around 18 months developing the system that allows existing diesel engines to run using 90 per cent hydrogen as fuel.
In a paper published in the International Journal of Hydrogen Energy, Professor Kook’s team show that using their patented hydrogen injection system reduces CO2 emissions to just 90 g/kWh – 85.9 per cent below the amount produced by the diesel-powered engine.
“This new technology significantly reduces CO2 emissions from existing diesel engines, so it could play a big part in making our carbon footprint much smaller, especially in Australia with all our mining, agriculture and other heavy industries where diesel engines are widely used,” says Professor Kook.
“Being able to retrofit diesel engines that are already out there is much quicker than waiting for the development of completely new fuel cell systems that might not be commercially available at a larger scale for at least a decade.
“With the problem of carbon emissions and climate change, we need some more immediate solutions to deal with the issue of these many diesel engines currently in use,” he said.
How the tech works
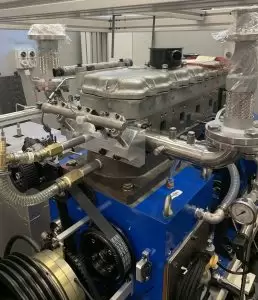
The UNSW team’s solution to the problem maintains the original diesel injection into the engine but adds a hydrogen fuel injection directly into the cylinder.
The collaborative research, performed with Dr Shaun Chan and Professor Evatt Hawkes, found that specifically timed hydrogen direct injection controls the mixture condition inside the cylinder of the engine, which resolves harmful nitrogen oxide emissions that have been a major hurdle for the commercialisation of hydrogen engines.
“If you just put hydrogen into the engine and let it all mix together you will get a lot of nitrogen oxide (NOx) emissions, which is a significant cause of air pollution and acid rain,” Professor Kook said.
“But we have shown in our system if you make it stratified – that is in some areas there is more hydrogen and in others there is less hydrogen – then we can reduce the NOx emissions below that of a purely diesel engine.”
Importantly, the new Hydrogen-Diesel Direct Injection Dual-Fuel System does not require extremely high-purity hydrogen which must be used in alternative hydrogen fuel cell systems and is more expensive to produce.
And compared to existing diesel engines, an efficiency improvement of more than 26 per cent has been shown in the diesel-hydrogen hybrid.
That improved efficiency is achieved by independent control of hydrogen direct injection timing, as well as diesel injection timing, enabling full control of combustion modes – premixed or mixing-controlled hydrogen combustion.
What were the challenges?
Professor Kook says that challenges were scientific rather than engineering.
“As mechanical engineers, we found the challenge was in the science, specifically with the understanding of the burning of hydrogen.
“When we started our work, we found that there was limited information about hydrogen combustion in the way we were planning to utilise it. There was very little research about mixture distribution and burning hydrogen, so we had to undertake it ourselves. We needed to understand the fundamental science before we could bring it to reality,” said Professor Kook.
“It took us three years to get a clear understanding of the science because there wasn’t much existing research on this topic. Once we had that in place it took just six months to implement the project. It was quite straightforward for our team of highly trained mechanical engineers once we understood the science,” he added.
Potential uses
The team says that any diesel engine used in trucks and power equipment in the transportation, agriculture, and mining industries could ultimately be retrofitted to the new hybrid system in just a couple of months.
“The most immediate potential use for the new technology is in industrial locations where permanent hydrogen fuel supply lines are already in place like mining sites. At these sites, where hydrogen is piped in, we can convert the existing diesel engines that are used to generate power,” said Professor Kook.
Back-up power generators are also a major application of this technology. The Australian market for diesel-only power generators is currently estimated to be worth around $765 million.
Green hydrogen, which is produced using clean renewable energy sources such as wind and solar, is much more environmentally friendly than diesel.
“One of the key issues holding our innovation back is the supply and transportation of hydrogen. We need to rely on others to solve these challenges before the benefits of this can be fully realised,” he added.
“In terms of applications where the hydrogen fuel would need to be stored and moved around, for example in a truck engine that currently runs purely on diesel, then we would also need to implement a hydrogen storage system to be integrated into our injection system. The ultimate use would be in marine propulsion but that is a long way off,” said Professor Kook.
Next steps towards commercialisation
Professor Kook sees multiple pathways for the next steps toward commercialising his team’s technology.
“There is definitely more scientific research required to look at things like other possible mixtures. It is unlikely that we’ve already found the ultimate solution. We also need a pilot project to bring it to the field where our field engineers can show off the technology. And of course, we need investors and we’re already talking to some people,” concluded Professor Kook.