As parts of Australia swelter through another summer, firefighters rely on engineered solutions such as drones to keep them safe in an inferno.
Jeremy Stubbs from Fire and Rescue New South Wales had just got off the phone to a couple of local commanders.
He’s been briefing them on the actions being taken around a silo fire in rural NSW, one still burning while he spoke to create.
When a silo burns, it is quite literally an explosive situation. Gases from stored grains can turn what appears to be a manageable fire into a very serious one in the blink of an eye.
Fortunately, Stubbs, who is Chief Superintendent Technical Capability, along with other Fire and Rescue NSW commanders use technology to minimise life risk.
Rather than sending firefighters in to investigate the situation, Fire and Rescue NSW has the option to instead send drones.
“In the past, we’d deploy ladder platforms to analyse the situation, to get eyes in the sky, or hypothesise from a distance,” said Stubbs.
A drone is known in the fire service as an RPAS, or remote piloted aircraft system, and doesn’t just represent eyes in the sky. Drones used by Fire and Rescue NSW also test the surrounding air for hazardous gases.
“A nine-head gas detector is on the drone, and we can monitor the atmosphere remotely,” Stubbs said.
“We’re not just receiving a live video feed; we have options to measure flammability, toxic gases, thermal imagery – and we’re doing it without sending anybody in.”
One of the biggest advantages of firefighting technology including trucks, aircraft and analytics software, Stubbs said, is that it can keep firefighters at a safe distance – or at least in a safer place – while providing time-critical data to enable informed decisions.
Protecting the troops
During recent fires, some of the most frightening news stories have been about firefighters forced to retreat to their truck as they have been flanked by walls of flame.
During a bushfire, charity organisation the Bushfire Foundation said, flame temperatures can reach up to 1100 °C.
What hope do firefighters have hiding within a fire truck against such heat? Thanks to modern engineering, they’re now relatively safe.
A vital capability of rural fire trucks is the protection of occupants during burn-over moments. This has become increasingly important as firefighters tackle larger and faster-moving fires.
“Ensuring the safety of firefighting crews requires a comprehensive safe system of work, which encompasses not only vehicle design but also training in fire behaviour and firefighting tactics, entrapment drills, dynamic risk assessments and hazardous tree awareness, doctrine and personal protective equipment and clothing,” said Danny Jones, Head of Fleet and Protective Equipment at Country Fire Authority (CFA) Victoria.
CFA’s crew-protection system has been tested in laboratories and in the field, including in forest and grassland environments.
A video of this testing shows a truck in a forest-fire situation, with external temperatures reaching 610 °C while the internal temperature remained at 38 °C.
This is possible thanks to a combination of solutions:
- External water deluge operable from within the cabin
- External heat shielding panels
- External critical component protection – that is, lagging of brake and fuel lines
- Internal radiant heat protective curtains to all glass window surfaces
- Replacement of vulnerable external plastic components with alternatives such as aluminium
- Installation of non-combustible air-cleaner elements
- Internal and external alarming for audible and visual crew safety water levels
More than 1000 existing CFA vehicles have been retrofitted with these systems. The typical life cycle of a vehicle in a firefighting fleet is around 30 years, but that’s not the end of their lives.
“Once decommissioned, these vehicles are sold and may end up being purchased for private firefighting in farming areas, or the body removed and cab chassis repurposed,” Jones said.
Great decisions, faster
Often, engineers are distanced from the space for which they are designing.
Not so Dr James Mullins. He’s a third-generation volunteer firefighter and, when he’s in the office, a robotics engineer.
Most of the engineering involved in designing and developing FLAIM Systems, Mullins’s virtual reality-based firefighter training platform, has involved hiding the technology to enable greater human integration.
“We try and hide away all of the foibles, challenges and problems associated with virtual reality and the Windows operating system,” said Mullins. “We hide it behind a piece of middleware that attempts to understand what a user is trying to do.
“We try to take that away to make it useable for people … so the technology disappears, and the learning outcomes come to the [fore]front.”
Doing so required a systems engineering approach.
“We look at breaking down a fairly complex system that needs a lot of different moving parts into fairly common blocks,” Mullins said. “That makes it a scalable platform for us.
“It’s about using the right tools and understanding the upgrade paths and the pain points for customers. Then, we abstract the learning software away from the hardware abstraction layers, or what we call the FLAIM Core.
“This is basically a hardware abstraction layer that talks to the hardware so that we become relatively platform agnostic.”
That design has come in handy over the past few years as supply chain issues have meant the business cannot afford to be fussy about hardware choices.
“We’ve had to be a little bit agile and change some of our hardware on the fly,” he said. “Effectively, our middleware detects what kind of hardware it’s connecting to. Then, the learning content sits on top and doesn’t know the difference.”
Technology is also now vital in the management of uniforms worn by Fire and Rescue NSW firefighters, Stubbs said.
Over the years, fire services have become increasingly aware of contaminants picked up in clothing during a fire. Now, after every event, firefighters remove their uniforms and pass through a decontamination area before getting into the truck.
At the station, they will scan out another clean, decontaminated uniform, using an app on their smartphone.
The app automatically updates the local launderer, who restocks the station with relevant sizes within 24 hours. The system dramatically reduces human contact with contaminants, Stubbs said.
The air force
Fire and Rescue NSW maintains a fleet of 75 RPAS platforms and 200 trained pilots. Within regional NSW it has 25 RPAS stations for rapid deployment. It adopts a centralised approach to mobilise more specialised capabilities.
With the service using drones more often, it has begun to recognise entirely new uses for the technology.
The agency deploys drones to give firefighters and other agencies accurate situational awareness, to enhance critical decision-making during operations including structure fires, bushfires, hazmat incidents and fire investigation.
After a tsunami, a drone’s LIDAR capabilities can help identify potential dangers, such as disturbed asbestos. And after intense weather such as a major hailstorm, drones can identify the worst-hit areas so rapid damage assessment teams know where they are most needed.
As drones are increasingly in use for a number of tasks, engineers have been tasked with boosting their performance.
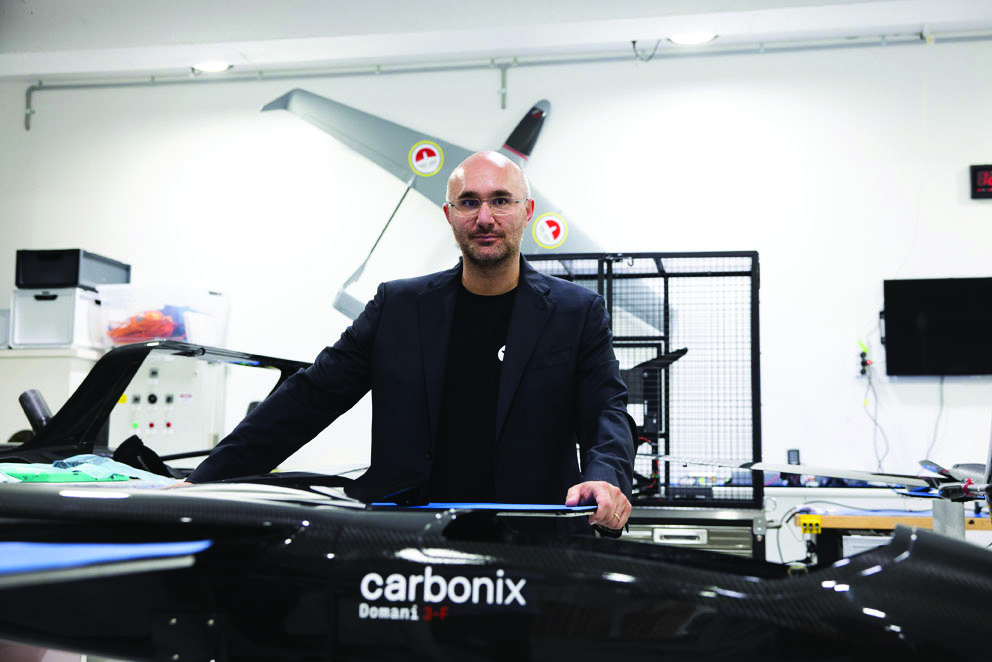
At the cutting edge is Carbonix, an Australian business that produces fixed-wing drones capable of vertical take-off and landing. Carbonix drones boast flight times of up to eight hours.
“We provide aerial data capture solutions at scale,” said Dario Valenza, founder of Carbonix.
“We’ve created this tool, this platform, that has unique flight time and payload carrying capacity. It can take off vertically and spend eight hours in the air, carrying a decent camera.”
The engineering challenges have been numerous, Valenza said.
There’s a payload challenge in getting the equipment in the air, on a vehicle that must ultimately be highly portable. There’s a performance challenge in developing a thrust system that can keep the drone in the air for hours.
And there’s an aeronautical engineering challenge in designing an aircraft that can fly using fixed wings, then decelerate and land using a quad propellor system.
“The problem we wanted to solve was the long range, so we started with the sensors it had to carry. The camera, LIDAR scanner and satcom link add up to about five kilos.” Valenza said.
“For the range, it has to be fixed wing, which requires a little bit of thrust to overcome drag, but otherwise [it] is energy efficient. But we’re using it in the field, in the middle of nowhere, with no runway. So how do we get it to take off and land?”
On the face of it, Valenza said, tilting multi-rotor configurations combined with the fixed wing appears attractive because the same thrust system can be used for the propulsion – both vertical and horizontal.
But the vertical thrust must be powerful enough for the weight of the aircraft, along with a margin for manoeuvring. That thrust is far more than what is needed for horizontal flight.
That can lead to too much power, delicate pitch issues with the propellers, a need for overly complex tilting mechanisms that require their own motors and add more weight, or a requirement for radical variation in the motor’s output.
So Carbonix has pioneered a “quad-plane” configuration, where four dedicated vertical lift motors are combined with an efficient single horizontal propulsion engine in a pusher arrangement.
The system required six years of design and testing, but now it’s flying high.
The future of firefighting
Five to ten years from now, Jones said, firefighters will likely have thermal imaging technology and automated water control available for use, all from the safety of the truck cabin.
In fact, some trucks in the CFA Victoria fleet already have a front-mounted water cannon, operable via an in-cabin, electronic joystick control.
The more that can be done to remove humans from the danger zone, the better the result.
Just as important, said mechanical engineer Dr Alexander Filkov, Senior Fire Behaviour Research Fellow at the University of Melbourne, is for communities built in potential fire zones to be designed for fire-resilience.
When we discuss fire-resilient buildings, Filkov said, we typically think about materials – and so we should. In fact, he said, standards for specific materials will have to be revisited to consider the effect of firebrands, or airborne embers.
Despite the fact that 50 to 90 per cent of house losses over recent fire events have been due to embers, he said, current standards typically ignore embers as a potential ignition source.
However, it’s even more important to consider the overall design of the neighbourhood. This matters particularly in terms of the distance between buildings.
“We need to design communities so that once a house is ignited, we don’t have this perfect house-to-house propagation,” Filkov said.
Houses are typically designed to survive, to an extent, exposure to bushfire. But bushfires don’t burn as hot or as long as housefires.
“Once a house is ignited, there is a domino effect,” he said. “One ignites another because they’re so close to each other.”