The lead engineer on the Umbagong District Park bridges project explains how to build a durable, low-impact structure that blends seamlessly into the natural environment.
Not so long ago, the three pedestrian bridges in Canberra’s picturesque Umbagong District Park, built in 1986, had fallen into disrepair.
The walkways were falling apart, with residents taking it upon themselves to implement solutions, according to Nicholas Borner, Structural Engineer at Sellick Consultants.
“Because it was such a useful route across the length of the park, they started removing planks that had fallen down and putting in new ones,” Borner told create.
For safety reasons, bridges 1193, 1194 and 1195 were condemned and closed to the public in April 2021. While plans were in place for an upgrade to the bridges, they were slow moving.
After residents formed an action group to get the ball rolling on the repairs, engineering firm Sellick Consultants, landscape architecture and urban design practice Taylor Cullity Lethlean (TCL), and head contractor Complex Construction was engaged to redesign the bridges to modern standards.
While bridges 1194 and 1195 are relatively low level, bridge 1193 was built into a 60° rock face. Reopening for public use in September 2023, the innovative design and construction of the bridges was recently recognised with the Small Project Steel Sustainability Award.
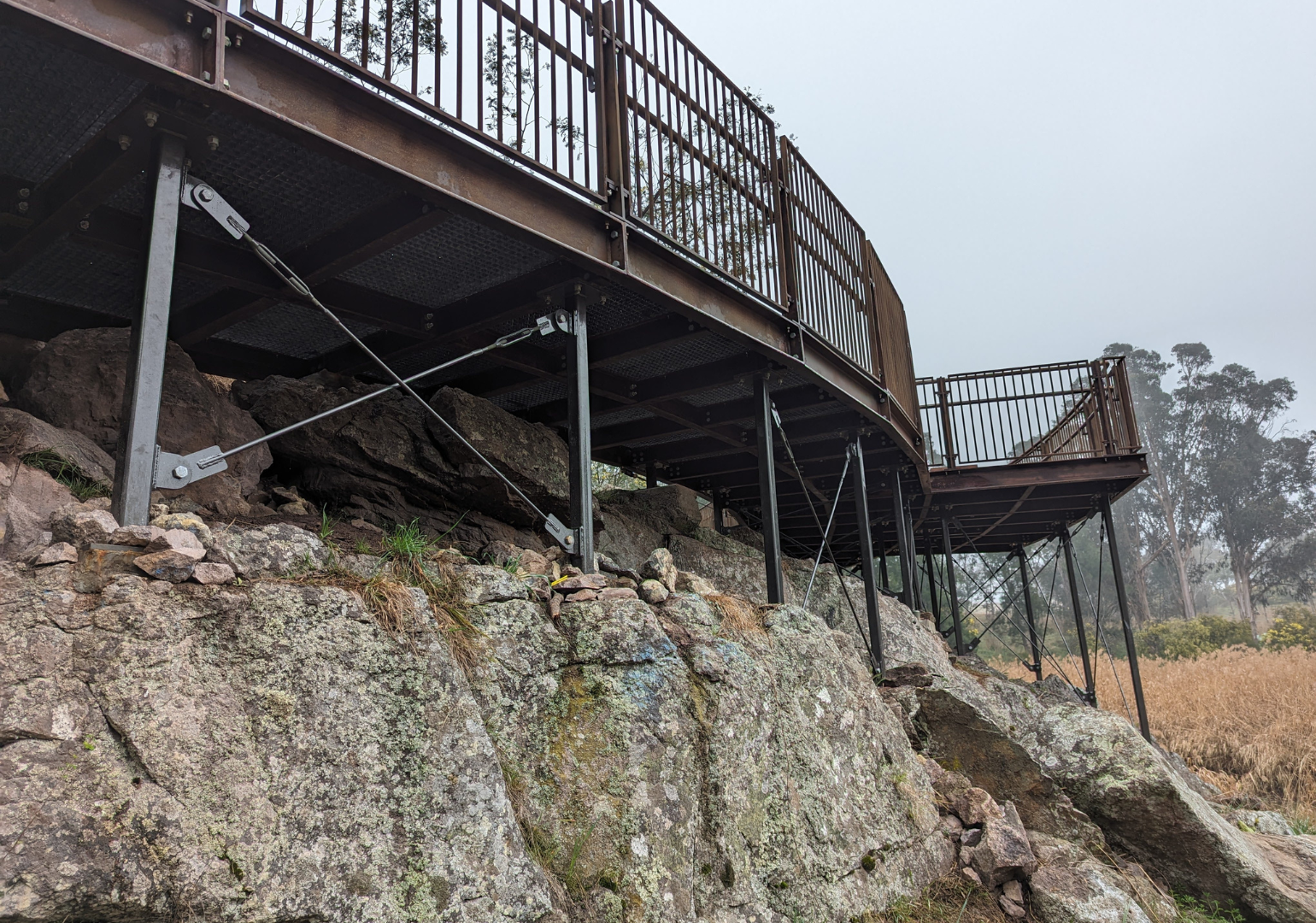
Making it modular
Given the bridge upgrade works were taking place in a park spanning over 50 ha, site access was tricky, Borner said.
“There are footpaths leading to the bridge and nothing else,” he said. “While there’s an access path directly above bridge 1193 to get to a water main checking station, the power line above it meant there was no potential for craning in materials.”
All bridge parts therefore had to be transportable along a footpath – with a maximum length of 2.4 m – to preserve the surrounding protected native grasses, a key priority for the local landcare group who were part of the design consultation.
Modular assembly limited the need for large construction vehicles, with a view to using quad-bike sized machines. With bridges 1194 and 1195 following a similar curve, the same toolkit could be used to produce repeatable metal pieces.
“We limited it all to off-the-shelf steel sizes,” Borner said. “And we didn’t need any massive custom beams. It was all parallel flange channels and small structural beams.”
The team opted for steel over concrete, partly due to the access requirements but also for its lightweight, recyclable properties.
“Because we used weather-sealed steel, the bridges should last for a long time, with the maintenance on the steel also very low,” he said.
Building into rock
To further reduce environmental impacts, the existing rock outcrops were used as structural foundations for bridge 1193.
While this approach minimised the need for extensive civil works and limited use of materials – the team was initially concerned it would in fact “make everything much worse”.
“Rock is an irregular surface to sit on, so we assumed we would need bespoke footing designs and custom faceplates,” Borner said.
After conducting geotechnical surveys to determine the quality of the rock and where the different parts would sit, the footing design had to wait until the rest of the design was finalised.
“When we knew exactly where all the footings were going to go, we discovered we mostly needed two types of footings – standard path footings that sit in soil, and footings that sit directly on rock,” he said.
With a uniaxial compressive strength of 100 MPa, the structural rocks are stronger than concrete.
“We could slightly grind back the rocks and attach a base plate, or if the rocks were really uneven, a very small area was infilled with concrete to provide a flat surface which we could then drill straight through – saving us from using much concrete,” Borner said. “Everywhere we could connect to the rock, we did.”
Overcoming design challenges
It wasn’t all smooth sailing. Aside from the access challenges, some tweaks were needed to the original design of the bridges.
“Constructing 1193 from one end to the other for safety reasons meant some of the connections we designed weren’t possible,” Borner said. “We needed the support members to be bolted through to achieve torsion to connect the handrail at the top, otherwise it was going to wobble around.
“If you’re 10 m up a cliff face and the handrail wobbles, suddenly you don’t want to be on the bridge anymore.”
Working with the builder, the team redesigned the connections using TF (tension friction) bolts rather than standard bolts.
“That meant they could install it then use the bridge they were building for access to build the rest, so they could start dismantling the old one,” he said.
The height of the lower bridges was also called into question, after an early survey was unable to reveal the lowest point of the ground.
“We wanted to build the bridges a maximum of a metre off the ground so they didn’t need closed sides, but when the survey was conducted the river was higher,” Borner said.
“At the time of construction, it hadn’t rained for a while, so the bridges would have sat more than a metre above ground in accordance with the original design, meaning we’d need to put in fall protection relatively late in the piece.”
Jumping into solution mode, the team updated the structural steel shop drawings, opting to lower the entire bridge rather than adding ramps and barriers.
Building a bridge to modern standards these days also means taking climate change into account – including flood loading.
None of the bridges span over the river, but a flood study concluded that all three could nevertheless be underwater in the event of a one-in-500-year flood once potential climate risks were included.
“We therefore had to design all the bridges for a log impact, which meant calculating the loads and having a full finite element analysis model of each bridge,” he said.
Final touches
The original Umbagong bridges were painted white, contrasting strongly with the natural space. This time around, the aim was to fit in with the environment as much as possible, Borner said.
“We replaced the bright wooden bridges with a rusted steel look, which is a much more natural colour,” he said.
To get this look, a set of coatings, conceptualised by TCL, were applied to the mild steel handrails and structural elements – causing the steel to rust, while simultaneously sealing it.
“By starting rusty, as the bridges corrode a bit more over time, they will retain the same look,” Borner said. “And because it’s sealed, it won’t cause any structural issues.”
The bridges are also now bike friendly and disabled compliant, complete with a wider path and higher handrails.
“There’s a new viewing platform on the cliff where people can stop and look over the river at the surrounding reeds and lizards basking on the rocks,” he said. “It’s a really nice natural space that residents can once again enjoy.”