Until April 2023, structural engineer Fiona Zhang had spent 13 years designing and consulting across a wide range of construction projects.
But then her creative flair and impressive building design skills brought her to the attention of a company that would radically change her outlook and require her to learn a whole new set of skills.
She had joined XLam, and suddenly had to get up to speed on buildings made from engineered timber panels – cross-laminated timber, or CLT.
“I’d always worked with steel and concrete,” she said, “so it took some time for me to get my head around using wood. I was a little apprehensive at first, but the more I looked into it, the more pleasantly surprised I became.”
Strength and versatility
Zhang’s hesitancy was understandable as timber buildings are less common in Australia than in Europe and North America. Many building owners and construction professionals have never used it, and they may have developed preconceptions about its qualities and suitability for certain projects.
“I was impressed by what I found out,” she said. “I had no idea CLT is so versatile. I wish now I’d made that discovery sooner.”
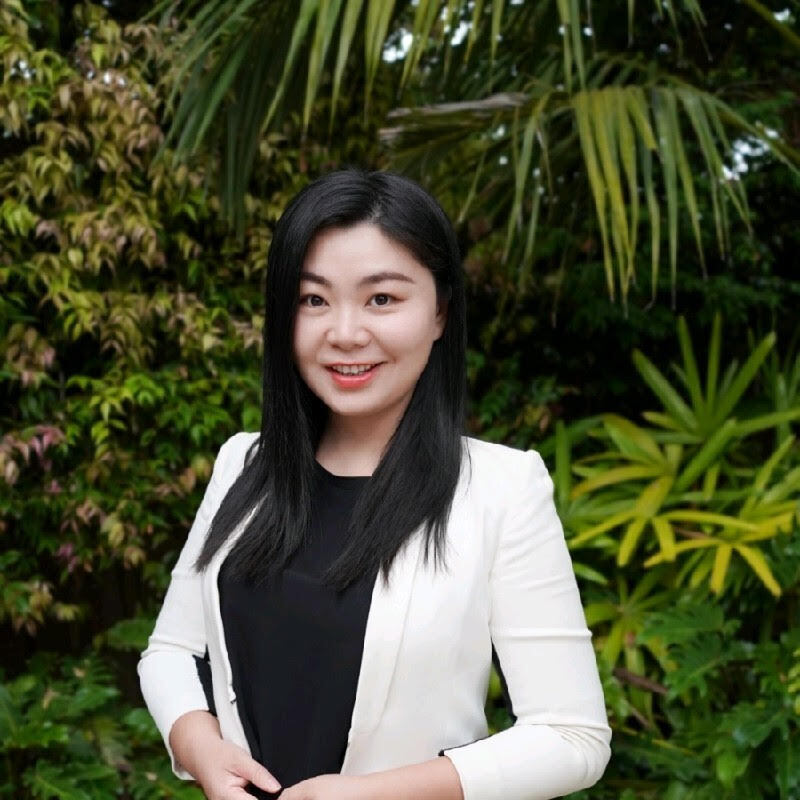
XLam was the first company to manufacture CLT in Australia. As an engineered wood product, CLT has superior strength, stiffness and dimensional stability when compared to solid wood.
The wide range of available panel sizes makes it suitable for use as wall, floor, stair and roof elements in a range of building classes. There has also been extensive local fire testing carried out over the last decade, meaning projects can be designed to be compliant with project fire resistance requirements.
Zhang said there are five key lessons that she’s learned over her first 12 months at XLam.
1. On-site simplicity and time savings
“Timber builds can be a lot quicker than concrete,” Zhang said. “You don’t have to wait weeks for laying reinforcement and concrete to cure before installing the next floor. Formwork is not required when CLT replaces concrete on site.
“Plus, for large multi-storey buildings, using XLam CLT in construction is more efficient because it allows access to the floor directly after assembly. This enables pre-loading of materials so the building can be made watertight more quickly, which, in turn, has flow-on time savings for a faster fit-out.”
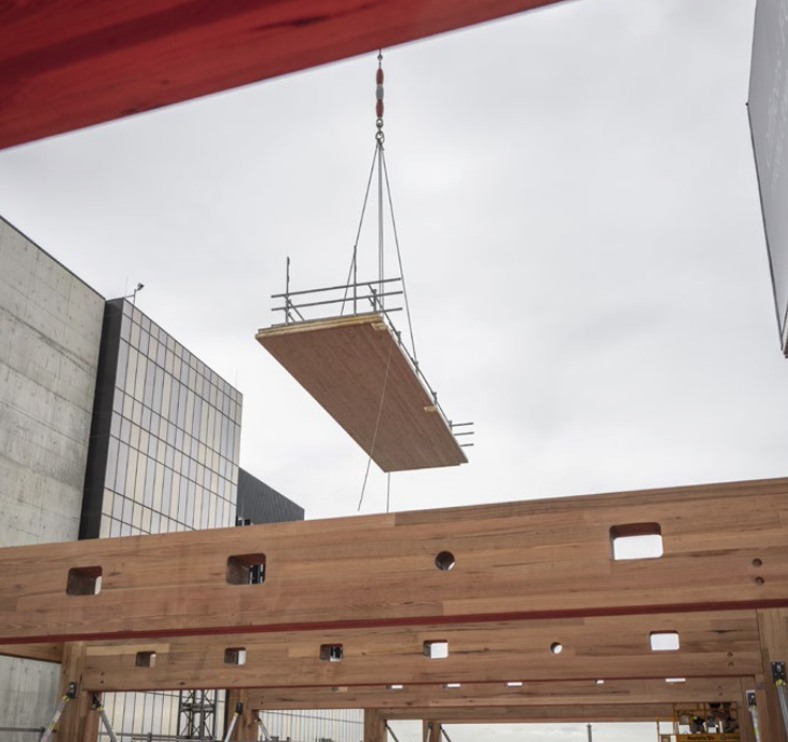
CLT is manufactured and machined to final dimensions in a controlled factory environment, allowing a highly consistent quality. The large format panels can be up to 16 m in length and 3.4 m wide so it takes less time to assemble a building. Additionally, the required checks of connections during structural inspections are usually simple and efficient to carry out.
“And it’s only 20 per cent of the density of concrete, so it’s much lighter. All the pieces are prefabricated and precision-cut to exact specifications and delivered ready for construction. There’s less noise, dust and waste on site so less pollution and disruption to neighbouring properties.”
Fewer people are required onsite and, with a carefully planned site assembly, erection of the structure can be achieved in 30 to 50 per cent less time compared to using more conventional systems.
2. Structural options
For developing designs of new timber buildings, CLT works very well when combined with a braced glulam post and beam frame. Full-timber buildings of six or more storeys are possible with an attractive, exposed mass timber structure.

Full CLT projects, sometimes referred to as ‘honeycomb construction’, are an effective option for low rise residential and dormitory style projects. Their construction and detailing can be very simple using off-the-shelf connection systems to simplify procurement.
While a full mass timber option may be the best solution on some projects, others may benefit from a hybrid approach using CLT as the floor plates, and steel or concrete as the primary beams, columns or bracing. This may be seen on projects that require very long spans and constrained on total floor depth.
“Extensions of existing buildings can benefit significantly from using CLT,” Zhang said. “For example, when looking to add additional levels onto an existing building, the lighter weight of CLT has the potential to reduce strengthening work significantly compared to concrete or steel structure or alternatively permit a greater number of additional floors.”
3. Enhanced sustainability
The four billion t of cement produced around the world each year contributes over eight per cent of global carbon emissions. The steel industry isn’t far behind, accounting for a further six per cent.
By comparison, because the timber used in the manufacturing of CLT retains the carbon absorbed by oxygen-producing trees, it has a significantly reduced carbon footprint.
A building made from CLT can generate up to 75 per cent less embodied carbon emissions than its concrete equivalent. Put another way, a cubic metre of concrete produces 300 kg of CO2eq whereas the same volume of XLam’s CLT sequesters 492 kg of CO2eq.
The timber used in XLam CLT is sustainably sourced from PEFC certified softwood plantations in Southern New South Wales. That means that every time a tree is harvested to make CLT, a new tree is grown in its place.
4. Biophilic benefits
“One factor I hadn’t thought about before joining XLam was the positive effect a timber building has on those who work in it,” Zhang said. “A recent report by FWPA-funded study by Pollinate shows that it can have some startling effects.”
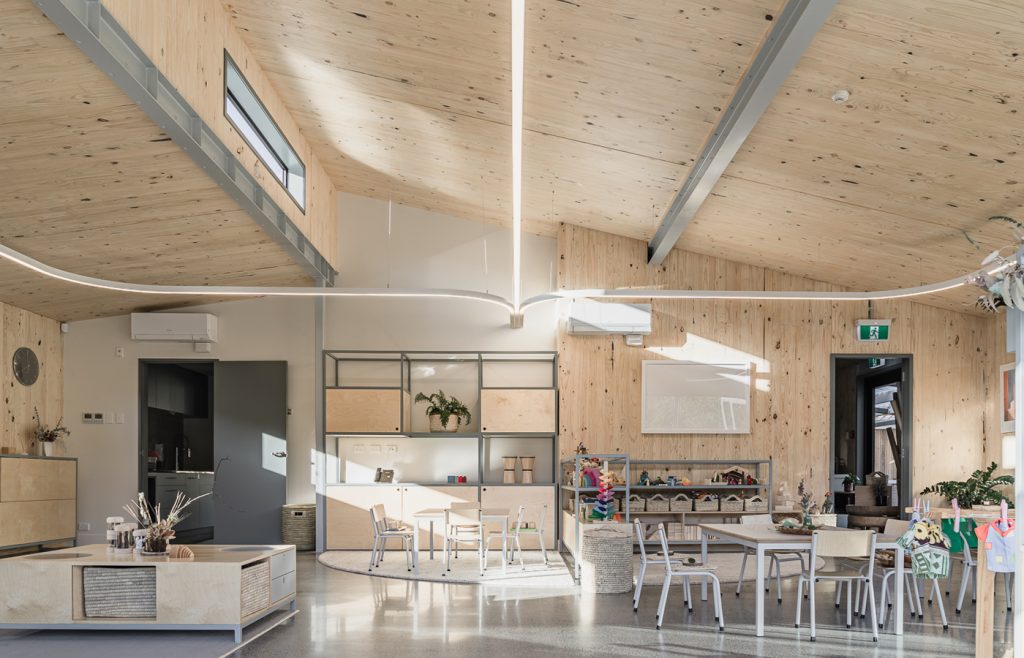
The study compared responses from people working in buildings with either a low or high proportion of exposed wood surfaces. Some of the results showed:
Low High
Physical workplace satisfaction 47 per cent 81 per cent
Ability to concentrate 65 per cent 83 per cent
Low stress levels 42 per cent 65 per cent
Satisfaction with working life 56 per cent 81 per cent
“I’ve always thought that exposed timber has a calming effect, and this survey certainly backs that up,” Zhang said.
5. Giving it a go
While CLT is not currently referenced within the Australian timber structures design standard (AS1720), there are Australian and international guidelines. Australia is also home to Wood Solutions, an initiative providing technical resources to designers.
“We also offer design services to our customers,” Zhang said. “This can be light-touch assistance or full structural design services. They give us a direct insight to the challenges they face and how we can provide better support.”
Zhang hopes that Australian engineers who have never tried using mass timber will give it a go.
“I’ve really grown to love working with it and I’m still learning new things about how it can be used,” she said. “It would be great to see more mass timber buildings with CLT as a building material here as they look amazing and they’re great for the planet.”