Three engineers explain how foamed bitumen could be an environmentally friendly and cost-effective alternative to regular materials — and could help fortify roads against flooding.
How is foamed bitumen created?
Foamed bitumen is produced by injecting a small quantity of pressurised air and water into hot bitumen, creating a low-viscosity and high-volume expanded foam.
When hot bitumen is injected with cold water, it expands to over 10 times its initial volume and then gradually decays. In its expanded state, the foam is thoroughly mixed with cold aggregate, secondary binder (either cement or hydrated lime) and water to produce the foamed bitumen stabilised (FBS) material.
The foam primarily coats the fine particles in the aggregate, creating a bitumen mastic. A foaming agent is generally used to enhance the foaming characteristics of the foamed bitumen.
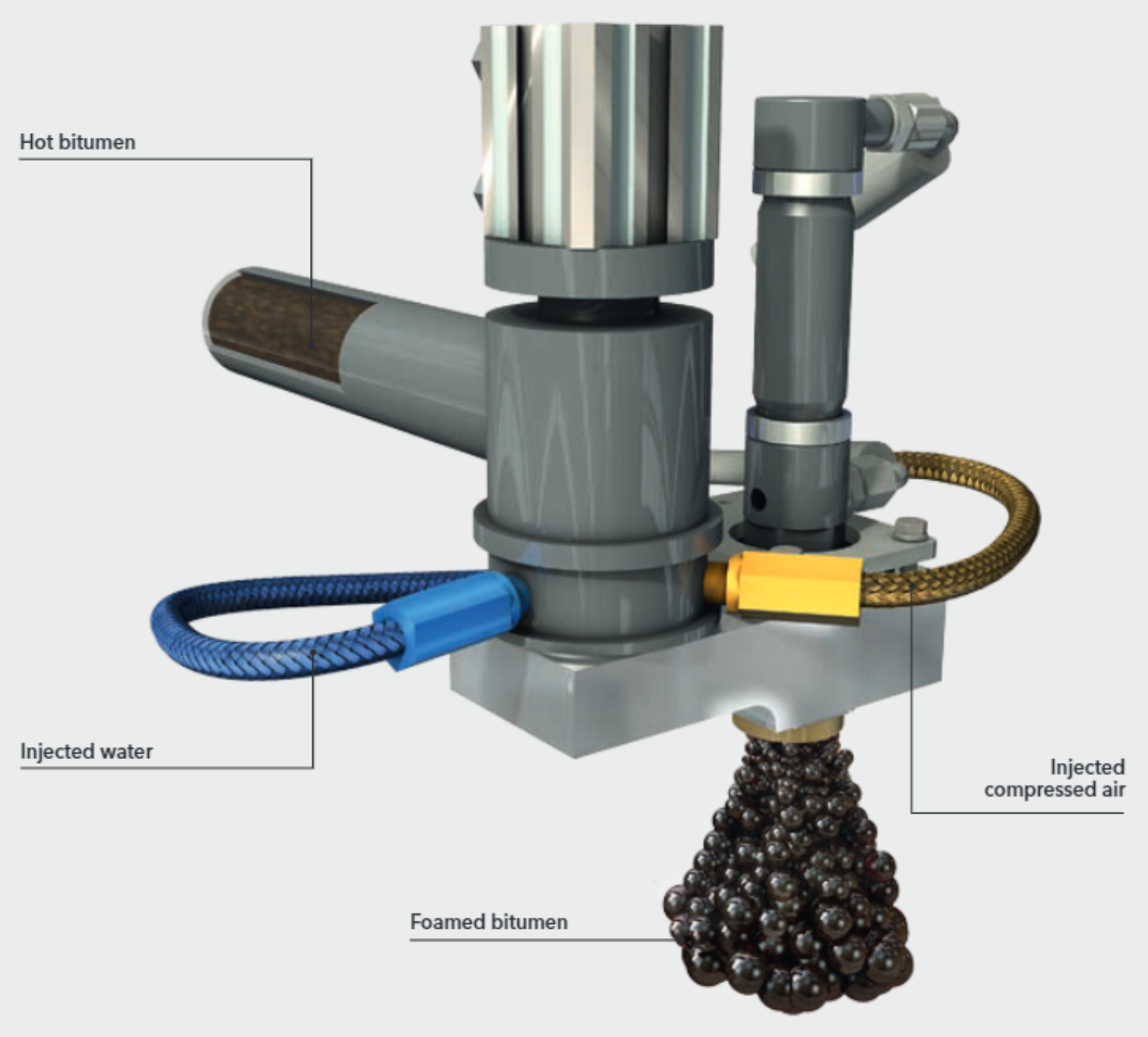
How can foamed bitumen be used?
FBS materials are cost-effective, eco-friendly, often more economical than cement-based alternatives, less susceptible to moisture, and immediately trafficable upon road construction.
FBS roads have also demonstrated remarkable resilience against flooding. These roads were able to reopen to traffic shortly after the floodwaters subsided, as reported by the Queensland Department of Transport and Main Roads.
The existing unbound granular pavements with a relatively thin seal, which account for over 90 per cent of the Australian sealed road network, can be strengthened using in-situ stabilisation with foamed bitumen, and new road bases can be constructed using plant-mixed FBS manufacturing.
What challenges exist in current practice?
Fatigue cracking (bottom-up cracking) is the primary failure mechanism for FBS road bases under repeated heavy traffic loading.
Although foamed bitumen stabilisation has been used for decades, the absence of a dedicated fatigue relationship for FBS materials means the current Australian pavement practice must rely on directly applying the asphalt laboratory fatigue relationship to estimate the design life of FBS road bases.
Experimental investigation
In collaboration with the Australian Road Research Board, we conducted a meticulous laboratory investigation and analysis into the flexural behaviour of FBS materials under various conditions, including different binder contents, temperatures and immersion in water.
Bitumen supplied by Puma Energy was used to manufacture foamed bitumen. The foaming agent HiFOAM-B was selected for its enhanced foaming characteristics. The bitumen temperature was maintained at 180°C, and the optimum foaming water content was set at 4.2 per cent for foamed bitumen preparation.
To produce the FBS mix, a granite aggregate from Lysterfield Quarry in Victoria was mixed with predetermined quantities of foamed bitumen, a secondary binder (either cement or hydrated lime) and water. This mixing process was undertaken at the optimum moisture content of the selected FBS mix.
The mix was then compacted in rectangular steel moulds to manufacture beam samples for flexural testing under different conditions. To replicate field conditions, the beam samples were initially cured at 40℃ for two days and subsequently cured for an additional 90 days at room temperature before the laboratory experiments.
Key findings
The flexural fatigue experiments, conducted using a four-point bending apparatus, revealed that FBS specimens, even after soaking in water for 48 hours, exhibit a similar fatigue life to unsoaked specimens at operational flexural stress levels. This aligns with the field performance of FBS road bases following flooding incidents.
The experimental results showed that the flexural fatigue life of FBS beams increases with increasing bitumen content at high flexural stress levels, and this increase diminishes as the applied flexural stress level decreases, as shown in the diagram below.
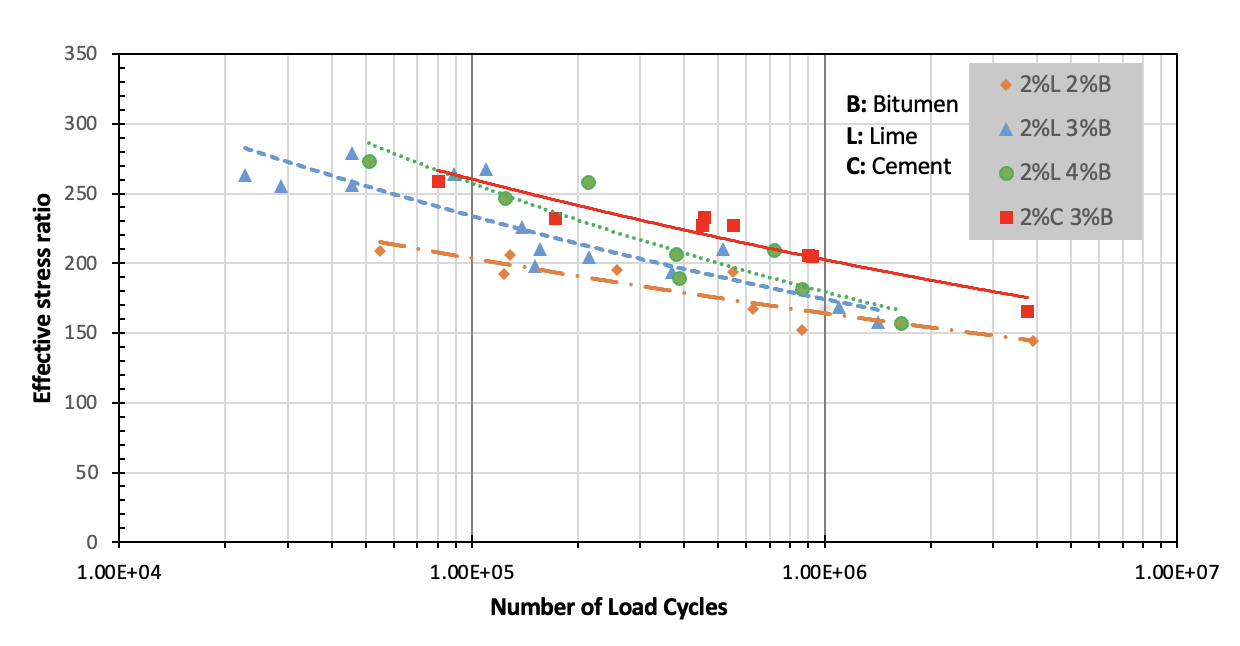
Furthermore, FBS mixtures with two per cent cement showed over three times higher flexural fatigue life than those prepared with two per cent hydrated lime. No noticeable difference was seen in the flexural fatigue life of FBS specimens when the hydrated lime content of the FBS mix was increased beyond two per cent.
The normalised modulus degradation master curve, where the current flexural modulus value is divided by the initial flexural modulus value and the current number of load cycles is divided by the number of load cycles to the flexural fatigue failure, appears to demonstrate a characteristic behaviour of FBS materials under stress-controlled cyclic fatigue loading.
Using this new concept and the laboratory test data, we developed suitable analytical models for predicting the flexural fatigue life of FBS mixtures under various conditions.
The recent Austroads publication on foamed bitumen material references the findings of our foamed bitumen research project.
Ideal for road construction
FBS materials consist of bitumen as the primary binder and cement or hydrated lime as the secondary binder. The bitumen content enhances moisture resistance and flexibility, fostering ductile behaviour — meaning an increase in strength, stiffness and failure strain.
Conversely, the cement/hydrated lime content bolsters strength and stiffness but reduces the failure strain, which is typical for most stabilised materials with cementitious additives.
This combination of increased strength, stiffness and ductility (i.e. failure strain) embodies the ideal material characteristics for road construction. This innovative concept paves the way for creating new resilient materials that incorporate blends of recycled materials such as crumb rubber, plastic, crushed glass and concrete.
Nonetheless, further work is necessary to fully harness the performance of foamed bitumen pavements and apply these insights to enhance other road construction materials.
About the authors
- Dr Arooran Rajah MIEAust CPEng is Chief Operating Officer of the Smart Pavements Australia Research Collaboration (SPARC) Hub.
- Dr Sameera Pitawala MIEAust CPEng is Senior Geotechnical and Pavement Engineer at Stantec.
- Professor Jayantha Kodikara is Professor and Director of the Smart Pavements Australia Research Collaboration (SPARC) Hub.
You made a good point when you discussed that the bitumen content brings an increase in strength, stiffness, and failure strain. My friend needs foamed bitumen stabilisation for their project. I should advise him to turn to provider that specialises in foamed bitumen stabilisation.