Technologies such as robotics, artificial intelligence and 3D printing are rapidly changing the way humans create. Can Australia seize the upper hand in advanced manufacturing?
In a facility on the outskirts of Geelong, a team of engineers is refining technology that could one day feature in the next generation of fighter jets.
They’re integrating thin-film solar cells into carbon composite sheets, building a single aircraft part that is both structural and a solar panel.
Other research in the building is exploring composites for hydrogen storage and harnessing the conductivity of carbon fibres to create a battery from an aircraft wing.
The facility is the research and development arm of Quickstep, an Australian manufacturer producing advanced composites for defence, commercial aircraft and drones.
The company’s contracts include parts for Super Hercules military transporters and F-35 Joint Strike Fighters. It’s intricate, high-tech work.
“It’s a much more complex process than just pouring steel or aluminium in a mould, or smashing it in a stamping die,” said engineer Luke Preston, Quickstep’s Head of Technology and Partnerships.
“You’ve got to build it up and layer in a really specific way to get your strength.”
Carbon fibre is 14 times as strong as steel, but only in one direction.
“On average, you roughly get half the weight for the same strength,” he said. Composites also make it easier to manage any damage.
“In metal, if you get a crack, as you vibrate and move that part, the crack will propagate,” Preston said.
“However, if you get a crack and some damage in your carbon fibre … the damage doesn’t grow over time.”
Preston said composites can also have other materials embedded into them.
“[In] aircraft, you often have copper mesh to protect for lightning strikes,” he said.
“Or you can put Kevlar-style materials in if you want to help ballistic protection.”
It’s the kind of manufacturing the country will need more of if Australia is to revive its ability to make world-class products at home.
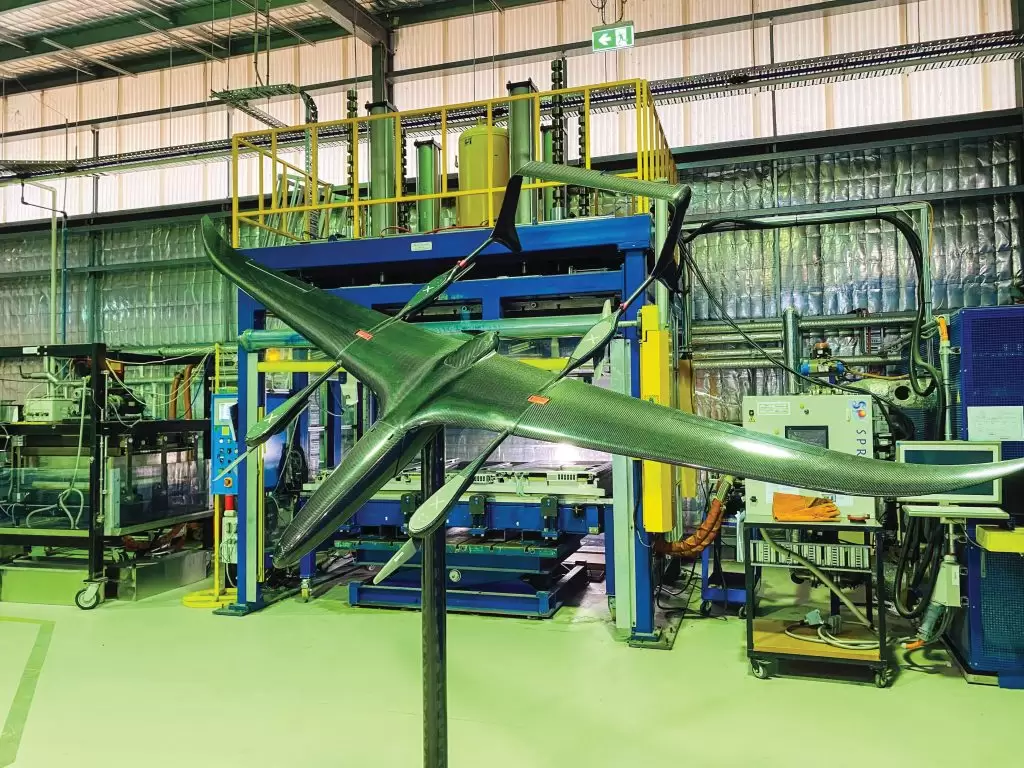
Industry 4.0
In the first industrial revolution, steam power was used to mechanise production. For the second, electricity created mass production. The third, or digital, revolution automated it.
The fourth is expected to blur the lines between the physical, digital and biological worlds.
Engineers Australia CEO Romilly Madew AO FTSE HonFIEAust EngExec said the fourth industrial revolution is being led by economies that have harnessed artificial intelligence and the Internet of Things to optimise data exchange in their manufacturing processes.
That presents Australia with an opportunity.
“Australia has an effective window to build on our use of Industry 4.0 technologies in advanced manufacturing to compete with low-cost manufacturers from other countries,” Madew said.
“Our ranks of highly skilled and qualified professionals give us an advantage in the niche product space.”
Earlier this year, the Australian government launched an inquiry into advanced manufacturing.
“Advanced manufacturing in Australia is bigger than people think, at $100 billion annually and hundreds of thousands of jobs,” Madew said.
“And there are still great gains to be made.”
One Australian business that has embraced advanced manufacturing is Breseight, a precision engineering company founded in 1983. Over the years, it has diversified to offer services including 3D printing and laser sintering, before launching medical device offshoot BresMedical.
The company collaborated with European oral and maxillofacial surgeons to develop ImplaNav, a system that improves the accuracy and safety of dental implant surgery.
It is also commercialising personalised joint replacements and a range of orthodontic cutters.
Breseight Managing Director Kevin Cullen, the son of one of the company’s founders, said its medical devices path began with 3D printing technology.
“We just followed the line of where the products could be used,” he said. “And basically brought in technology and education to get us down that path of innovation.”
Part of Breseight’s strategy has been to partner with research organisations, and the company collaborates with universities in Australia, the US and Europe.
Cullen, who trained as a mechanical engineer, said the first challenge was to bring new standards into the company, such as the ISO 13485 certification for medical devices. But one of the hardest things was getting the company’s existing workforce up to speed.
Staff had to transition from working in a contract shop to producing innovative medical devices.
“You’re going from an old school-type knowledge to a higher level,” Cullen said.
“[It was] just a different way to think for the company.”
Workforce challenge
Dr Cori Stewart is the founder and chief executive of the Advanced Robotics for Manufacturing (ARM) Hub, a not-for-profit supporting Australian manufacturers.
She’s worked with hundreds of local businesses looking to integrate robotics, artificial intelligence and other Industry 4.0 technologies into their operations.
Cullen’s training challenge is something Stewart has seen again and again as companies seek to modernise their manufacturing processes.
“It usually is a workforce challenge,” she said.
Stewart said the ARM Hub aims to design solutions with the people working on the floor.
“They’re the experts, because they know what success looks like; they know what they’ve got to produce at the end,” she said.
Stewart said it can help to allay people’s fears about losing work, no longer being good at their job, or not being relevant.
“And we know, by putting them at the centre, they will then be much more likely to use the technology that comes out the other end,” she said.
“They’ll have a sense of ownership, they will have designed it, and they will have been trained in it through that process.”
Madew agrees it’s a challenge for businesses to keep up with the rapid pace of technology and keep their workforce ahead of the curve.
She said micro-credentials can provide an opportunity for engineers to rapidly upskill in fast- developing areas of Industry 4.0.
“It’s an option that offsets the overhead of investing heavily to study technology that is evolving rapidly,” Madew said.
“And it’s very effective at fostering cross-skilling so engineers from different disciplines have a path into advanced manufacturing, as well as high-value transferable skills.”
Madew said areas for businesses to upskill include innovative design, technical leadership, reliability and post-production intangibles, such as after-sales service.
“Engineers are prized in this space, particularly those whose communication skills are honed for sales and the ability to apply technical detail and talk through end-user benefits,” she said.
Manufacturing myths
Preston, who started his career at Ford and spent four years at Tesla before returning to Australia, believes two “easily believable but really untrue” misconceptions about manufacturing are limiting the country. The first is the idea that manufacturing is low-tech.
Preston said when the automotive sector shut down in Australia it was made to appear as a knuckle-dragging industry.
“Now companies like Tesla are leading the world through technology, through a car company,” he said. “We need to really grow our appreciation of it.”
The second misconception is that Australia is too small a market and shipping products around the world is prohibitively expensive.
“I think that’s a big falsity, because the dirt gets shipped as unrefined dirt, as iron ore,” Preston said.
“Battery materials [lithium and copper] get shipped as unrefined materials.”
Preston said Australian minerals might be sent to China for refinement, then the US or Europe for manufacturing, before being delivered back to the local market.
“If you did a full study of the full lifecycle of dirt to product, the best way to deliver that product would be to add all the value next to the hole where you dug your dirt,” he said.
“I think there’s such an opportunity. We need to be adding the value and using that to grow the country significantly.”
The “new surgeons”
Stewart said advanced manufacturing needs a wide range of engineering and design capabilities, including electrical and mechanical engineers.
“The engineering base is fundamental,” she said.
“And it’s hard to be able to recruit fast enough across industry.”
Stewart thinks Australia should celebrate engineers the way they’re celebrated in places such as Germany.
“I think they need to be the new surgeons,” she said.
“We have to build really fast, we have to invest really quickly, and we have to have our ear to the global market.”