It’s an infrastructure designer’s nightmare. Midway through the delivery of a complex bridge design, the engineering team on Melbourne’s Lathams Road project realised the data they were working with was wrong.
The as-built position of an existing structure was out, both vertically and horizontally. It meant the entire new bridge they were designing had to be moved.
“The existing abutment was 300 mm off,” said Hatch Senior Bridge Engineer Tanmay Vegad.
“When we had the new structure on, all our abutments and piers had to be aligned, so that the actual envelope [was] consistent across the two structures.”
Usually, realigning a whole bridge late in the game would take a month. But the team was using a new 3D approach.
“Using the 3D modelling … the entire structural model is linked to a civil alignment,” Vegad said.
“We just had to update the location and it automatically makes those changes across all the sheets. So that was a week’s worth of work versus four to five weeks’ worth of work if it was any other way.”
Challenging design
The survey data was one of many challenges on the project, a two-span continuous bridge in Melbourne’s south-east.
The scope of work strengthened and duplicated an existing bridge over the Mornington Peninsula Freeway, adding a new lane in each direction.
It had to be built without shutting the freeway — a major arterial road — at any point during construction.
“All our designs of the bridge itself were meant to follow a specific construction sequence and detailing such that there were no disruptions to the freeway itself,” Vegad said.
“Most importantly, of course, is that the bridge [could] be constructed safely, without any risk to the road users or to any maintenance work, construction work … especially around constructing the embankments.”
With substantial earthworks required, Vegad said the team thought carefully about the materials used and worked with internal and external specialists to lessen the project’s impact on the environment.
“One of the things that we’ve adopted in the design as well is to recommend a lot of sustainable materials,” Vegad said. “Recycled crushed concrete, recycled plastic, reclaimed asphalt and the like.”
The project would go on to be awarded the 2021 Hatch Global Award for Sustainability, and was a finalist in the 2021 Going Digital Awards in the Infrastructure — Bridges category.
Australian first
The Lathams Road bridge designers were the first in Australia to use a new 3D modelling product called OpenBridge. Hatch senior structural designer Ondrej Krivka, the lead designer on the project, said it was a big challenge moving from 2D to 3D digital delivery.
Krivka said the Bentley software had to be adapted for Australian standards, such as different abutments and precast barriers.
“It’s always a learning curve when you have a new software and [are] using it on the project at the same time,” he said.
But there were several advantages. The team used a program called LumenRT, a real-time visualisation software that allows engineers to present their design on site.
“They can use a mobile phone [or] special glasses where they just can look around and see the actual model sitting there already,” Krivka said.
“It gives you a bit of perspective of how it will look. It’s also good for the client to see it.”
Vegad said the team also used 3D modelling to assess the collision barriers on the existing bridge and bring them in line with current standards.
“To rip all [the collision barriers] out and do a new construction would be extremely expensive, extremely disruptive and also not sustainable at all,” he said.
Instead, the team did a full assessment of the existing structure and designed a new steel railing that made use of existing connections.
“We could work out the amount of steel used and work out the most efficient way to replace it with [the] minimum steel we could use,” Vegad said.
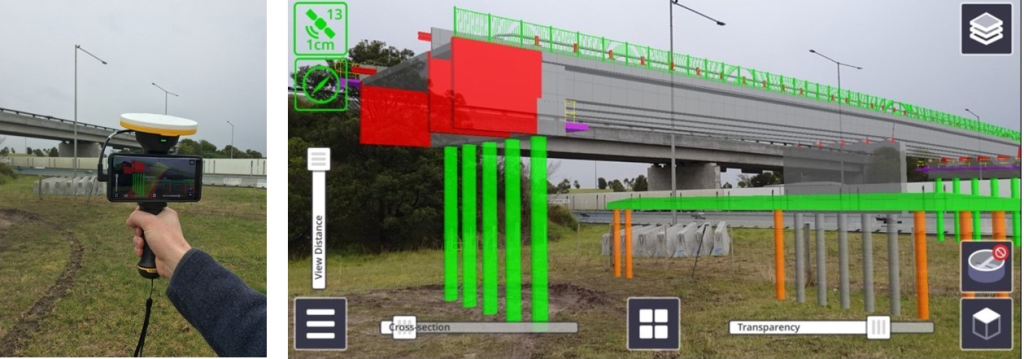
Future design
Dave Body, Senior Industry Strategy Manager for Civil Infrastructure at Bentley, sees a transformational change taking place from traditional 2D delivery of plans to 3D digital delivery.
“There’s a lot more expectation on the designer because they’ve still got to deliver on this 2D stuff,” he said.
“But they’ve also got to deliver on this new 3D digital delivery. And they’ve got to learn … how to model in this 3D environment. It’s a more accurate, more detailed object model that they previously hadn’t been doing.”
Body said digital data is also becoming central to delivery. He said the biggest thing in the near future is extended metadata, or attributed data.
“For example, [Transport for New South Wales], they’re now requesting anywhere up to 65 bits of extra attributed data that needs to be associated with each and every object or component on a bridge,” he said.
Body thinks the transition will impact the market heavily over the next five years or so.
He said this digital data can include unique asset classification or location codes.
“Somewhere along the workflow … this information needs to be attributed to that object,” he said. “It needs to be created or configured, it needs to be managed and maintained, basically within the BIM model. And then it needs to be delivered.”
Project delivery
The Lathams Road bridge design was ultimately delivered four weeks ahead of schedule, Vegad said.
Hatch Design Coordinator Joseph Armstrong credits the success of the bridge to having all of the main design software based on a single product, alongside file management in ProjectWise.
“It’s pretty flawless,” he said.
“There were no extractions or conversions … so it worked really smoothly.”
Armstrong prefers this approach over mixing file types like DWG and DGN.
“That’s when the deliverables start to fall apart,” he said. “It takes too much time to actually try and [connect] these three software together.”
For Vegad, the complexities of the project are what made it exciting.
“The whole purpose of this project was so that communities that live at that location would have a much-improved road system,” he said.
“The construction sequences that were required in order to not disrupt it, especially all the sustainability initiatives that were adopted … made it worthwhile.
“And also, the complexities of working around an existing structure and working
with a lot of stakeholders, disciplines, utilities and interesting challenges.”
A stitch in time
To construct a bridge above a live freeway, the engineers designed two spans that could be lifted into place without closing the road below.
The spans were then stitched together with post-tensioned stress rods above a single support in the middle of the bridge.
“That makes it a very efficient structure,” Vegad said.
“Also it’s a lot safer for construction, because you have less formwork, you have less materials, because these girders are all precast.”
Vegad said one of the big advantages of making this stitch was that, once done, the bridge acted as a continuous stretch across the freeway.
“Apart from placing in the span itself, most of the actual construction works have been from on [or around] the structure,” he said.