Engineers in New York City have used advanced 3D-modelling to help create a unique tessellated park over the Hudson River.
New York’s recently-opened Little Island is a US$350-million, one-hectare urban oasis — and a monument to cutting edge engineering technology.
Designed by London-based Heatherwick Studio and New York-based landscape architecture firm MNLA, Arup Associate and Project Manager Yongwook Jo led the team of engineers who brought their vision to life.
“The original design concept pictured a park ‘floating’ above the Hudson River, propped up by a complex array of piles of differing heights, all of which fused together at the top to create the park’s undulating topography,” he told create.
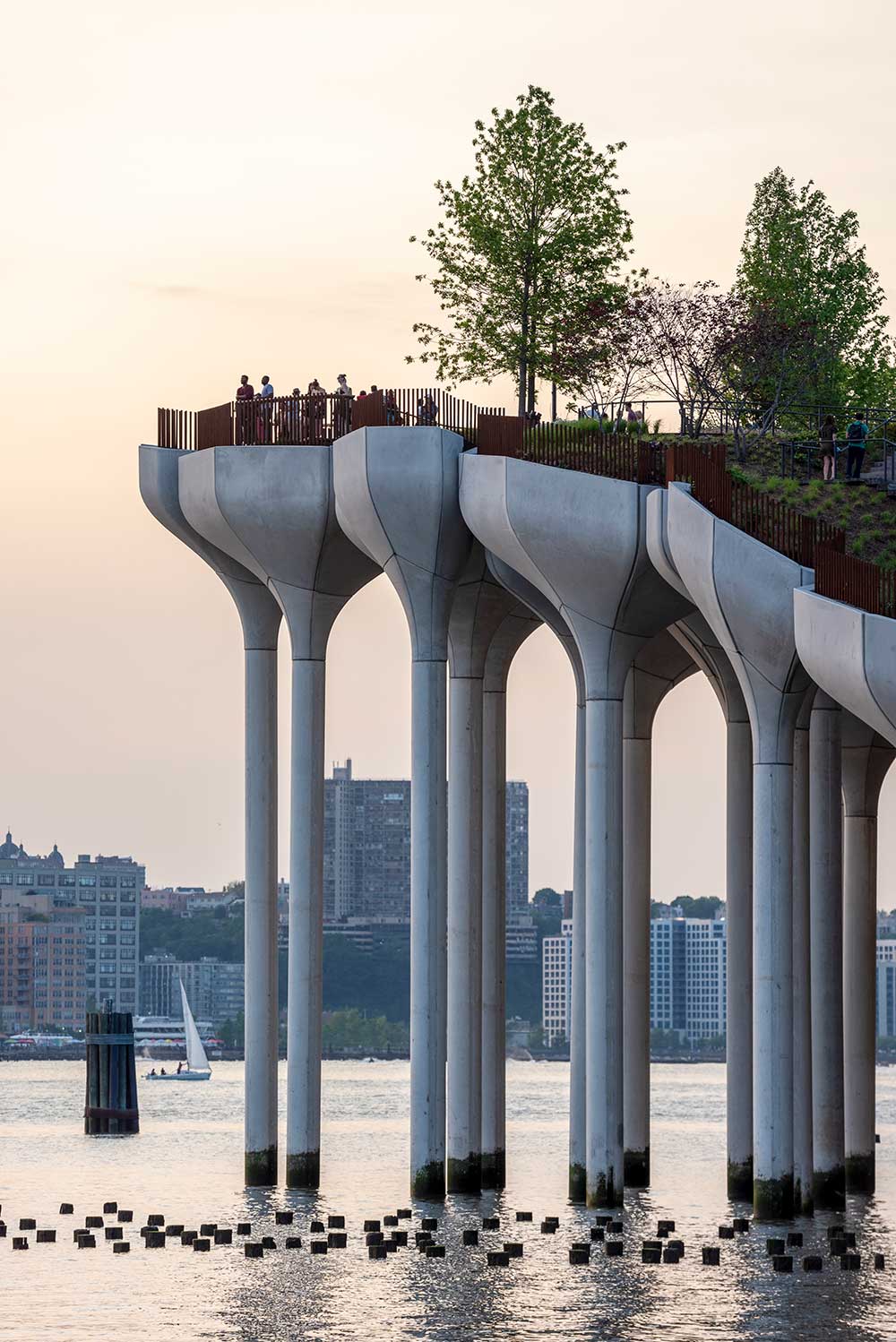
“We quickly determined that precast concrete was the best choice for the pots that form the park’s base, due to the challenges of constructing cast-in-place concrete over a river and the expense entailed in steel construction.”
The Arup team was tasked with finding solutions for everything from green infrastructure to venue planning and infrastructure design, but it was throwing around ideas with the architect that led to the striking pot design to support the undulating upper surface.
“To meet the architectural intent of an irregular appearing column grid, a ‘Cairo-Pentagon,’ which tessellates in plan, was adopted for the typical plot plan shape, which then blends via doubly curved surfaces to the cylinder pile below,” Jo said.
Twelve versions of this pentagon shape were then supplemented by additional pots around edges, the amphitheatre and the southern entrance. There were 39 different types of pots fabricated for the project, with 132 pots in total.
The pots were broken down into discrete pieces, consisting of a column head and four-to-six petals, for ease of fabrication and transportation, and were connected offsite by a series of stainless-steel connections.
“Connections were for the temporary case prior to installation on-site and in-situ concrete beams and slabs being poured,” Jo explained.
“Pots had a series of triangular precast planks that would sit on top and support light-gauge stay-in-place formwork for the beams and topping slab.”
Advanced 3D modelling
The most notable aspect of Arup’s design is the structural approach its engineers devised for the project, which harnessed advanced 3D-design and prefabrication techniques to ensure the unique design was structurally sound. Here, Jo’s team modelled the pots and their parts to fabrication level and delivered them to the client and fabricator electronically.
“We soon realised that the conventional workflow in 2D would not be applicable to the project,” he said.
“Design was only possible by actively engaging the latest digital technologies, including parametric and automated design, 3D-model deliverables and fabrications with CNC-milling of foams and laser cutting of steel plates.
“We used a 3D graphic application with scripts using parametric design to make close to life 3D models for each and every one of the 787 pot pieces — 132 column heads and 655 petals.”
The design project itself was a feat of engineering, with Jo’s team virtually labelling each steel element and rebar of the 132 pots, before submitting the 3D model for fabrication and enlarging it in a virtual fabrication yard. Any particular pot could have up to 1940 unique components — all individually modelled and tagged with a unique identifier.
“We produced the 3D models, providing extraordinarily detailed specifications for the offsite fabricator,” Jo said.
“By breaking each pot into discrete pieces and coming up with an efficient connection concept, the team also ensured that the pots could be shipped more economically and assembled on site with relative ease.”
When it came to the actual construction, Jo said the digital fabrication processes — including the robotic milling machine for the foam formwork, automatic rebar bending machine and the virtual fit-up using 3D scanning of the fabricated precasts — were directly fed from the 3D models.
Onwards and upwards
Alongside the 3D design process making constructing doubly curved surface concrete elements possible, Jo also believes that the off-site fabrication and assembly were the keys to the success of the project.
“Fabricated precast elements for pots were transported to a yard on the Hudson River, where they were assembled,” he said. “Eight stations were built to expedite the assembly process. The completed pots were transported down the Hudson River in a barge to the site and placed on top of the precast piles driven into the water.”
Jo believes that the Little Park project has shown that using digital design and fabrication on a large scale is feasible. His key takeaway was that having every member of the design and construction team on the same page from a the digital and 3D perspective is critically important for a complex project.
Arup is now using the digital workflow with scripted and automated design iterations to help make other design processes more efficient.
“We are developing a tool to create a detailed analysis model for an extruded high-rise tower,” Jo said.
“We’re already applying some of the specific tasks we did for Little Island to other projects. For example, we used the same logic and steps to create very detailed rebar models for a complex curved concrete structure in a museum project.”