An expert’s review of galvanized steel around Australia found a number of common misconceptions about the methods and standards when it comes to the inspection of galvanized steel.
One of the most economical and low maintenance corrosion protection systems, galvanized steel is a critical material for Australian infrastructure.
Recent changes to the National Construction Code 2022 mean that it’s more important than ever to understand galvanized steel inspection requirements.
“The code has put in place specific minimum coating weights, which can be equated to coating thicknesses, for different corrosivity areas,” said Ann Sheehan, Corrosion and Sustainability Officer at the Galvanizers Association of Australia (GAA).
“It’s important to be able to inspect galvanized steel to know whether you’ve got the right thickness or the right product for that application as the service life is proportional to the coating thickness.”
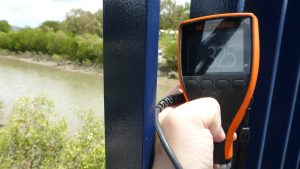
The type of galvanizing can usually be determined by the coating thickness. Most fabricated products in Australia use batch hot dip galvanizing, which has a thicker coating than continuous or electroplated coatings. Measuring coating thickness therefore helps businesses understand whether the coating is right for their application.
However, Sheehan said that while the requirements for average coating thickness are well understood, local coating thickness is commonly confused with the results of a single measurement.
“For batch hot dip galvanized steel above six mm steel thickness, the local galvanized coating thickness has to be above 70 μm and this is the average of all the measurements taken within a single reference area, while the average coating has to be more than 85 μm and is the average of all measurements taken on an article.”
Not the same as paint
Paint and galvanizing both use the same type of magnetic gauge to measure coating thickness. Measuring the change in magnetic flux density at the probe, which is translated to the distance from the steel surface, reveals the coating thickness.
But on Sheehan and her colleague’s recent series of inspections around the country, they found that many firms were conflating the requirements for inspecting paint and galvanizing.
“Paint is very different because it’s applied by an applicator,” she said. “Inspections are looking for surface and ambient temperature, dew-point, curing of the paint during the coating process, as well as coating thickness and various coating defects.”
A qualified inspector of both coating types, Sheehan said that people too often mistakenly label a ‘defect’ as a galvanizing issue when it is in fact purely a paint issue — the two have different Standards and testing requirements.
Galvanizing requires the steel to go through a series of baths to clean the surface before it is dipped in molten zinc. The coating formation is not fully controlled by the galvanizer as it depends on the way steel metallurgically reacts with the molten zinc. Paint, on the other hand, only forms a mechanical bond with the steel surface after being sprayed or brushed on and will commonly undergo adhesion testing. Some methods of testing adhesion for paint require scoring through to the base metal — something that can’t be done with a galvanized coating.
“Adhesion usually isn’t an issue for galvanized products, however, cohesion within the coating itself can be,” Sheehan said.
Cohesion issues can occur when large brittle alloy layers form. These can manifest in flaking of the galvanizing after impact during transport and handling.
“If we see flaking, it means it’s a break within the coating, rather than at the steel surface.”
Another way the inspections differ is that the measurement requirements for paint generally have much smaller and more specific intervals. For galvanized steel, this often results in specifiers asking galvanizers to take far more measurements than is required to comply with the Standard, AS/NZS 4680.
All the hot dip galvanizing inspection requirements are covered in the two-day HDG Inspectors course run by the Australasian Corrosion Association, developed by Sheehan and other experts at the GAA.
To learn more about how inspection methods for galvanized coating thickness might affect you, download the AN 37 Acceptance inspection and sampling methods for hot dip galvanized coating thickness. Note: Registration to the website is required in order to download documents.