Technology installed at Orica’s Kooragang Island facility in Newcastle has nearly halved the site’s greenhouse gas emissions, far exceeding expectations.
This article was originally published in the August 2024 issue of create with the headline ‘No laughing matter’.
In an Australian first, tertiary abatement technology installed in June 2023 has been reducing nitrous oxide emissions from Kooragang Island’s three nitric acid plants – used in the production of ammonium nitrate – by at least 95 per cent.
“When we make nitric acid, one of the by-products is nitrous oxide (N2O), or laughing gas,” Paul Hastie, Orica’s Sustainability and Development General Manager, told create. “It’s a serious greenhouse gas pollutant.
“This project aimed to put a catalyst on the exhaust pipe of all three nitric acid plants to break down that nitrous oxide into nitrogen and water.”
The technology, called EnviNOx, was developed by industrial company thyssenkrupp Uhde. It consists of large reactor vessels – giant cylinders measuring up to 14 m tall and 3.6 m wide, containing an iron zeolite catalyst – able to be retrofitted onto nitric acid plants.
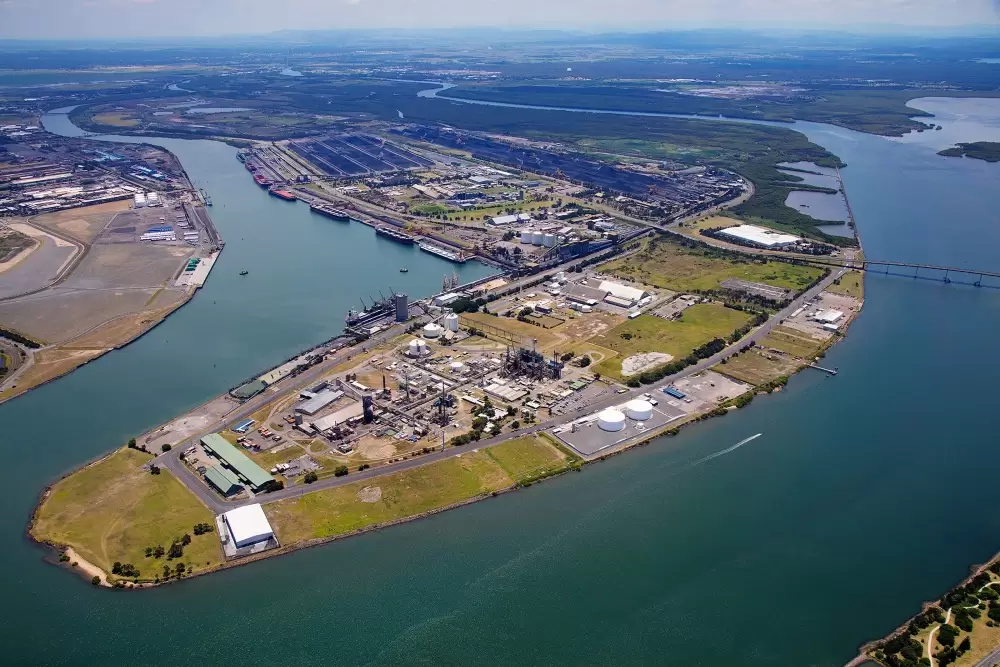
Ammonium nitrate reactions
Orica manufactures a range of products at Kooragang Island, primarily ammonium nitrate.
The site operates 24 hours a day, seven days a week, producing about 400,000 t of ammonium nitrate a year. Most is sent to mining operations in the nearby Hunter Valley, where the compound is used to make explosives for breaking up overburden.
Producing ammonium nitrate requires a complex set of chemical reactions. The 24 ha facility includes an ammonia plant, three nitric acid plants, two ammonium nitrate plants and a dispatch area.
Natural gas (methane, piped from Sydney to Newcastle) is first used to generate ammonia (NH3). That ammonia becomes an input for producing nitric acid (HNO3), which is later reacted with ammonia, producing ammonium nitrate.
Dr Gabriel da Silva, Associate Professor of chemical engineering at the University of Melbourne, told create that Australia is an extensive producer – and user – of ammonium nitrate.
“A lot of that is because of its use in agriculture as a fertiliser, and also as a mining explosive,” he said. “The ammonium nitrate process inherently deals with a number of gases that are potentially harmful to the environment, so there is an imperative to control those, both for human health and the climate.”
Serious concern
Inside the nitric acid plants, vaporised ammonia is mixed with air in the presence of a catalyst, which generates NOx gases at temperatures of 800-900°C. These gases are then absorbed into water to produce nitric acid, with nitrous oxide as a byproduct.
“When you do nothing, the N2O gas is emitted into the atmosphere,” chemical engineer Jarrad Bird, Orica’s Production Superintendent at the Kooragang Island facility, said.
Belying its nickname “laughing gas”, nitrous oxide is a serious concern when it comes to climate change. The colourless and odourless gas, commonly used as pain relief in medical procedures and childbirth, proves potent and long-lived when released into the atmosphere.
According to the CSIRO, N2O has a global warming potential 273 times that of carbon dioxide over a 100-year timescale (though Australia’s greenhouse reporting scheme applies a global warming potential of 265). The gas is the third largest emissions source after carbon dioxide and methane.
Concentrations of N2O in the atmosphere are now the highest in 800,000 years, a situation unequivocally the result of human activities, according to the IPCC. Da Silva said these factors make removing N2O “low-hanging fruit” for companies looking to reduce their greenhouse gas emissions.
“For every kilogram of nitrous oxide you remove, that’s the equivalent of almost 300 kg of CO2,” he said.
While nitrogen fertilisers used in agriculture are the main global source, industry also contributes about 14 per cent of human-caused emissions, according to the Global Carbon Project.
Abatement technology
From design to operation, Bird was involved in all aspects of installing the tertiary abatement technology.
Over the previous decade, Orica had trialled approaches to reduce nitrous oxide emissions. None came close to the effectiveness of EnviNOx, where nitrous oxide emissions are removed from the tail gas after the absorption stage. Bird said that each of the three new reactor vessels – one for each nitric acid plant – are filled with catalyst in a pelletised form.
“It’s arranged in a way that the flow path through the reactor is quite tortuous so that you’re encouraging mixing and contact with as much gas and catalyst as possible,” he said.
“The tail gas comes in the top. We add ammonia, which reacts with the catalyst to reduce any residual NOx gases. We also add methane, which reacts with the N2O.”
While the system is extremely effective at removing nitrous oxide, Bird said an “added bonus” is the removal of residual NOx gases, a known air pollutant.
“It’s not something that we could do with our previous technology, where we still had a small amount of NOx gases … this technology has enabled us to reduce that to zero.”
Da Silva said that processes that work on multiple air pollutants – if implemented and operated correctly – can have the benefit of improving local air quality at the same time as reducing greenhouse gas emissions.
Learning through doing
Years of careful planning, data collection and technical design preceded the onsite installation, which began in October 2022 and was completed in June 2023.
“It was a brownfield installation, so we had to retrofit new pipework and control logic, and design all our safety trip systems,” Bird said.
The new technology had to be integrated into every aspect of the plant’s operation, from training procedures to asset maintenance.
Each nitric acid plant was done sequentially, with the added challenge of installing the plant, with minimal disruption, at a facility that operates around the clock.
“For the first plant, we built the whole analyser room and frame,” Hastie said. “We built it adjacent to where it was going to be put in. So as soon as we shut down, we took out a vessel and lifted the prefabricated room into place. That saved a huge amount of time.”
While Kooragang Island marked the first use of tertiary abatement technology in Australia, for Orica it was the second time globally. The team benefited from previous experience at a site in Canada.
“I was fortunate enough to go over to our Canadian site,” Bird said. “I identified areas they found challenging. We had to dot our Is and cross our Ts when commissioning analysers, as it was completely new technology for us.”
He added it was also crucial to leverage the knowledge and support of the thyssenkrupp Uhde engineers.
Orica is so pleased with the results in Newcastle that plans for installing the same technology at Orica’s Gladstone site are already underway. And everything learned through the experience at Kooragang Island will be applied to assist the next installation.
Meredith Read, Orica’s Acting Head Sustainability, said the company completed a net-zero study to identify further decarbonisation opportunities.
Four pathways were identified: renewable hydrogen; feed and fuel switching to biomethane; carbon capture and utilisation/storage; and alternative methods for producing ammonia.
Support included $25 million from the Clean Energy Finance Corporation in the form of debt finance and $13.06 million from the NSW Government Net Zero Industry and Innovation Program.
For the CEFC, this was the green bank’s first major direct investment into the manufacturing sector. CEFC Head of Wind Joe Harber said the potency of nitrous oxide together with the immediate effectiveness of the technology made it a high-impact investment.
“It was an incredibly large abatement project,” Harber said.
“[It was] one we were keen to make sure happened, because for a relatively modest amount of upfront capital, you had a sustained impact and high abatement level.”
The savings from the technology are already enormous, approximately equivalent to 11 per cent of Australia’s chemical industry process emissions.
Read said given nitrous oxide emissions from producing nitric acid make up 51 per cent of Orica’s direct emissions (Scope 1) globally, secondary and tertiary abatement technology will be “a key lever in Orica’s decarbonisation pathway and ambition to achieve net zero emissions by 2050”.
For those involved, the benefits extend beyond just numbers. Hastie said it has changed how the site and industry are perceived within the organisation and the wider community.
“We’re really proud that Orica was a leader in this, especially in Australia, that we’re not waiting for others to do it.”