Swinburne University of Technology is collaborating with some of the brightest new manufacturing talent to help them harness the potential of additive manufacturing and Industry 4.0.
The fourth industrial revolution is transforming the manufacturing industry, fuelling innovation, driving productivity gains and creating new models for growth. But can it also present a solution to some of the pressing challenges of COVID-19?
The answer may be found inside Swinburne University of Technology’s Factory of the Future and Manufacturing Futures Research Institute in Melbourne.
A hub for innovation — and collaboration — its engineers recently teamed up with Australian manufacturer SPEE3D to 3D print and trial a copper coating for metal push plates that can kill 96 per cent of the virus that causes COVID-19, SARS-CoV-2, in just two hours. A recent study by CSIRO also confirmed the coronavirus that causes COVID-19 can survive for nearly 28 days on some of the common surfaces such as phones and ATMs.
Associate Professor Suresh Palanisamy, Deputy Chair of Swinburne’s Department of Mechanical and Product Design Engineering, said this is just one example of how the university is collaborating with industry to explore the potential of additive manufacturing and Industry 4.0 technologies.
“Metal additive manufacturing has been around for more than two decades, but industry in Australia faces a number of barriers to entry,” he said.
“The two major challenges are due to the initial capital expenses and not enough qualified and trained workforce to take-up the challenges in this area.”
Swinburne has been working with a number of industries to both train and educate them in these capabilities. For instance, Palanisamy has been working with a defence industry sector for more than a decade with the support of organisations like DMTC, DSI and DST Group in the additive manufacturing area.
“By working with Swinburne, businesses can test and validate their innovations and build a business case for investment in the technology,” he said.
Manufacturing innovation
Swinburne’s Factory of the Future is home to a suite of advanced visualisation, additive manufacturing and design tools that allow researchers, students and businesses to explore conceptual ideas for manufacturing next-generation products.
With the support from the Victorian Government, the LightSPEE3D 3D printer is one of its latest instalments. Developed in partnership with SPEE3D, it was recently used to 3D print the anti-microbial copper called ACTIVAT3D onto metal push plates.
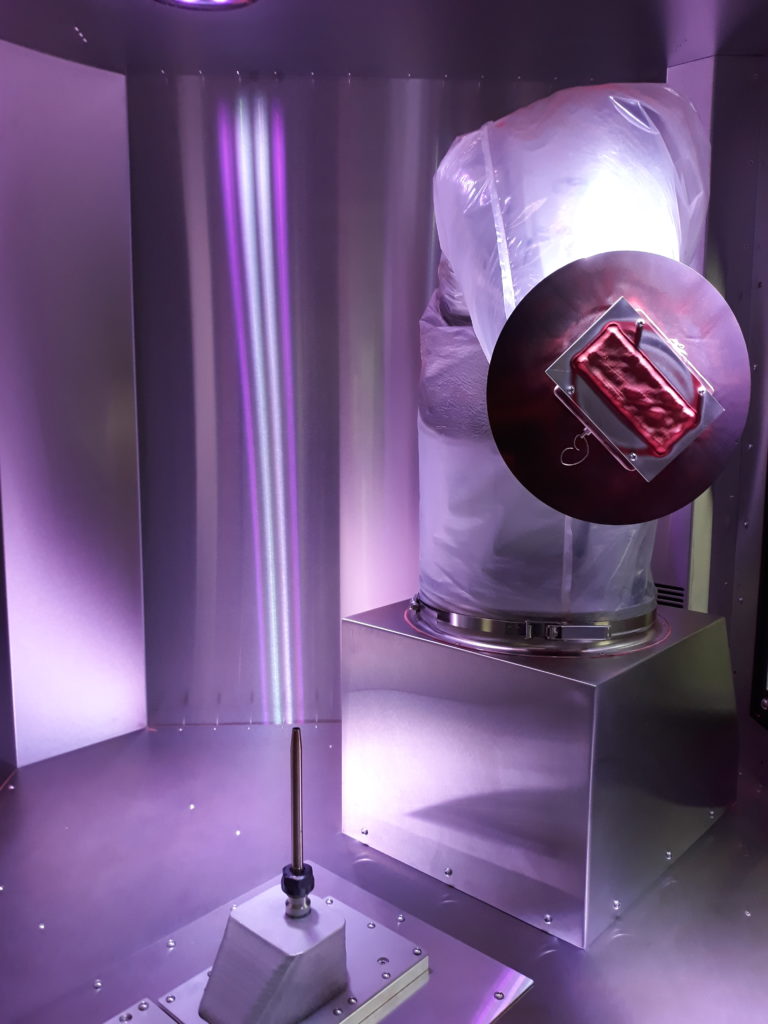
Copper parts are difficult and expensive to produce using traditional methods and 3D printing is one of the tools available to rapidly deposit the materials.
By modifying algorithms that control the LightSPEE3D metal printers, metal parts such as push plates, handles and other frequently touched metal items can be coated with the anti-microbial copper to help limit the spread of COVID-19.
“A crisis like COVID-19 requires a quick response and we were able to demonstrate the capabilities of the ACTIVAT3D copper push plates in a short timeframe,” Palanisamy said.
“We removed a push plate, fitted it in the machine, printed a part within about 12 minutes and then put it back on the door. The entire process was completed within 20 minutes.”
SPEE3D CEO Byron Kennedy said the company focused on developing a solution that could be deployed rapidly and was more efficient than printing solid copper parts from scratch.
“The lab results show ACTIVAT3D copper surfaces behave much better than traditional stainless steel surfaces and this may offer a promising solution to a global problem,” he said.
“The technology can be used globally, addressing local requirements — be they in hospitals, schools, on ships or shopping centres.”
Working together
With the recent Federal Budget including a $1.5 billion investment in the Modern Manufacturing Strategy, Palanisamy said there will be even more opportunities for local businesses to explore the potential of innovative technologies, compete internationally and create jobs.
“Industry 4.0 is not just about additive manufacturing. It encompasses a whole business-wide transformation,” he said.
“The Australian Government has been putting a lot of money into the manufacturing sector, so we have to clearly focus on how we can innovate and what we can achieve locally.”
Science and technology are changing what it means to be a manufacturer today — and welcoming a whole new generation of innovators into the sector.
Palanisamy sees huge opportunities for growth and says this will be fuelled by greater collaboration between industry and research.
“There is a major skills gap in the current Australian industry sector for both advanced manufacturing and industry 4.0 areas,” he said.
“Two years ago, Swinburne launched Australia’s first Associate Degree program in Industry 4.0 and it is also working on new specialisations in this area to cater to post-graduate cohorts.”
“We’re here to help manufacturers get to the stage where they can make quantitative decisions about the technology that is most suitable for their future and, at the same time, address the skills shortage.”