Left untreated, micropitting of gears due to surface fatigue can lead to serious issues. Selecting the right lubricant can help keep it under control.
While individual micropits are too small to see with the naked eye, they can change the shape of gear teeth to cause vibrations, misalignment and noise, and increase the chance of fatigue failure.
Micropitting is more prevalent in case-hardened (carburised or nitrided) gears. Another factor that can contribute indirectly is using a lubricant with additives such as chlorine, potassium-borate or sulfur-phosphorus, which are designed for extreme pressure (EP) operating conditions.
As well as causing havoc with gears, damage to gear teeth from micropitting can lead to metal particle contamination of gearbox oil that affects bearings and seals.
From little pits, big pits grow
Micropits are generally under 100 microns wide – about 50 to 70 times narrower than a human hair. As micropitting wears down gear teeth, load is concentrated over a smaller area and reduces the gears’ accuracy as they mesh.
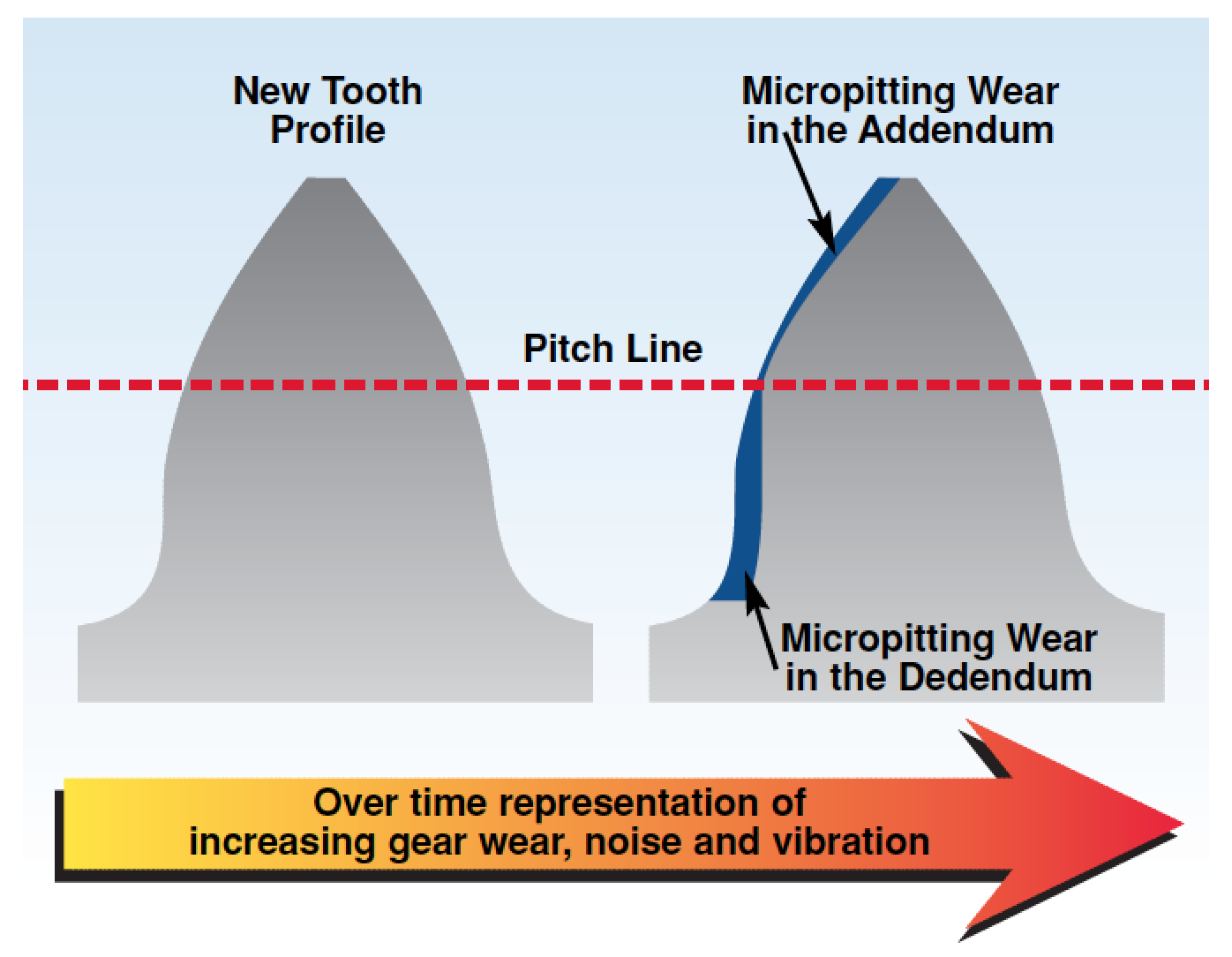
As micropits multiply, they can be seen as dull, matted areas on the surface of gear teeth. They can be tricky to detect in a visual inspection, often requiring illumination from multiple angles to confirm their presence. Intense direct lighting gives better results than diffused fluorescent illumination.
If allowed to continue unchecked, micropitting can escalate to major gear wear, or macropitting, which is one of the most common causes of industrial gear failure.
Pesky particles
The micropitting process starts with tiny surface cracks, which nucleate and wear away an increasing amount of surface material, similar to the damage caused by abrasive wear. But unlike abrasive wear, micropits result from rolling or sliding contact fatigue between the surface and subsurface layers of gear teeth.
The metal particles worn from the gear teeth are circulated in gearbox oil and can cause more damage by making ‘debris dents’ on other gear and bearing surfaces.
This can lead to surface changes on bearing rolling elements and races, and result in spalling – subsurface metal fatigue that can cause large arrow-shaped chunks of metal to detach from surfaces.
Particle debris can also wear down seals to cause leaks and let more contaminants into the system.
Although filtration of gearbox oil can be used to remove metal particles, much of the damage described above can occur before the particles are filtered out.
ExxonMobil scientists estimate that hard debris particles from micropitting on gear teeth have the potential to decrease bearing life by more than 20 per cent.
Prevention is better than cure
A proactive approach to preventing micropitting can extend the life of gearboxes and associated bearings.
This can be achieved in three ways: select ‘super-finished’ surfaces for gears and bearings; alter the operating conditions; or choose a gearbox lubricant designed to keep micropitting at bay.
Of these options, changing lubricant formulation is the most practical measure. Super-finishing comes at a high cost and is generally reserved for critical industrial processes; and operating conditions can be beyond the end-user’s control.
A key indicator of potential micropitting is the ratio of mean-surface roughness to oil-film thickness.
Increasing the lubricant’s viscosity index can provide a thicker oil-film under similar operating conditions than a lower viscosity alternative, and a lower traction coefficient can assist in easing surface fatigue.
So replacing gearbox lubricant with a synthetic oil that has a high viscosity index and low traction coefficient (such as the Mobilgear SHC™ SMP Series) can reduce the risk of micropitting and its consequent damage.
[Find your Mobil authorised distributor here]
While micropitting is a major concern in modern industrial gearing systems, it is important to choose a lubricant that also gives good protection against other failure mechanisms such as abrasive wear and scuffing. Other properties to consider are foam control, corrosion protection and compatibility with seal materials.