Converting plastic and polystyrene into durable railway sleepers could help reduce waste – and show how vital engineers will be to a circular economy.
According to Victorian company Integrated Recycling, which has been operating a factory at Mildura since 2010, a kilometre of railway track laid with its Duratrack railway sleepers uses 64 t of recycled plastic.
The sleepers are 85 per cent made of recycled material, a mix of “polystyrene and agricultural plastic waste, including cotton bale wrap, vineyard covers and pipe from the mining industry”.
They also have a lifespan of 50 years, compared to 14 years for timber, and are resistant to rot, fungus and termites.
In June, 190 of these sleepers were installed at Melbourne’s Richmond Station for an 18-month trial. It continues the apparent progress towards mainstream use of recycled composite sleepers.
Alternative sleepers are gaining acceptance worldwide, but, as Cong Qiu and Graham Tew of Monash University’s Institute of Railway Technology (IRT) wrote in 2017 in the magazine Newsrail, a “major issue within Australia is that there is no standard or code that currently exists for the use of these products”.
“There are some standards overseas, but they were developed for main-line operations,” Ravi Ravitharan, Director at IRT, told create.
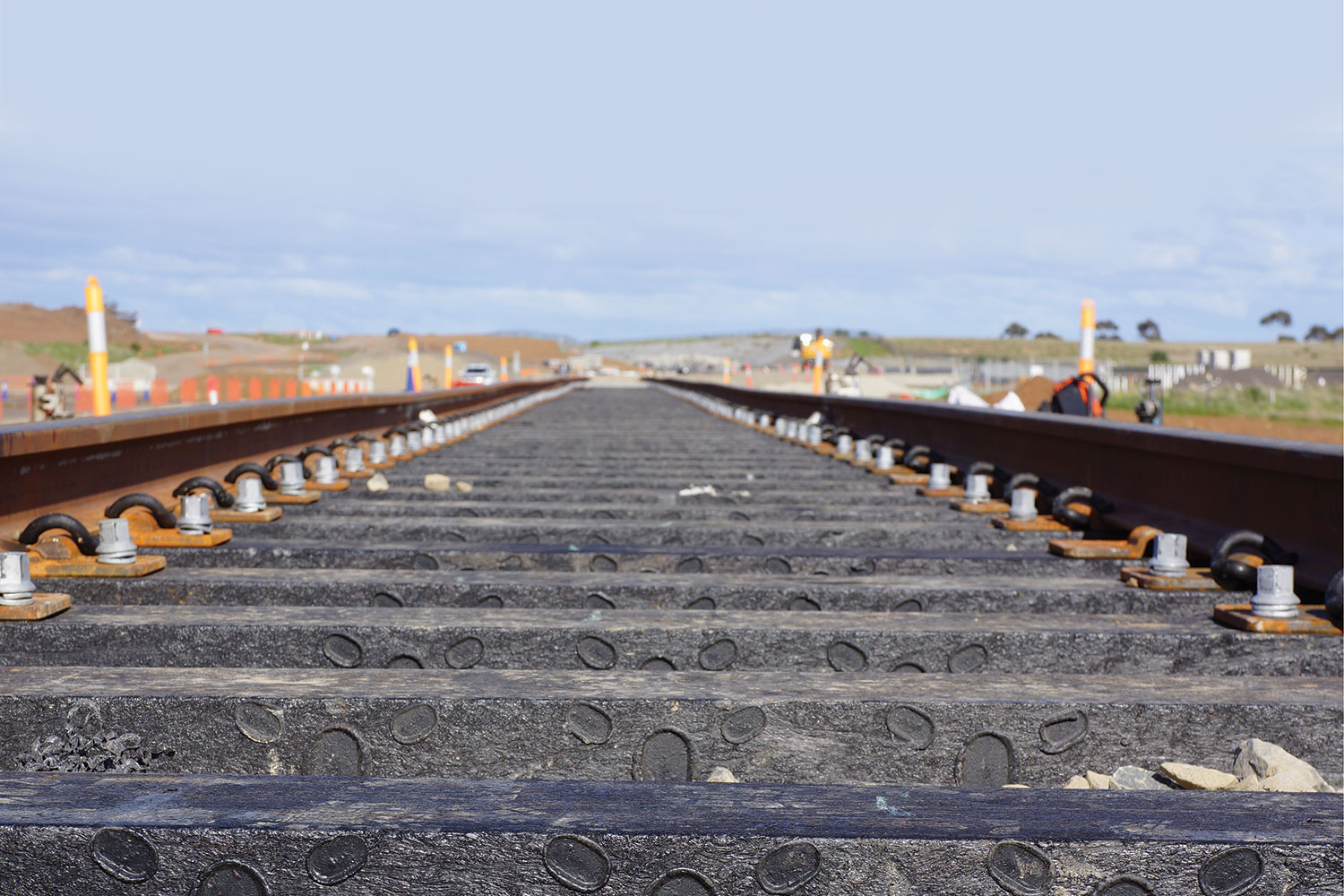
Since 2015, however, IRT has worked closely with industry to explore some of the issues requiring consideration when developing a new standard.
Standard bearer
IRT has worked with Integrated Recycling, beginning with a project supported by Public Transport Victoria (PTV) on recycled plastic sleepers for Tourist and Heritage (T&H) railways.
The shortage of timber for sleepers and the resulting high maintenance demands from using secondhand sleepers has forced operators to rethink their options. The outcome of this project was the development of guidelines for testing plastic sleepers to ensure adequate performance within T&H railways.
“A testing program of Integrated Recycling’s Duratrack product against these guidelines saw their product certified for use,” Ravitharan noted.
Ravitharan has more than three decades of experience in applied research in railway technology, beginning at BHP-Melbourne Research Laboratories, which turned into IRT in 2000.
His awards include an Academy of Technological Sciences and Engineering Clunies Ross Award in 2014, shared with Peter Mutton and Graham Tew.
“In the absence of transparent standards, it is difficult under the regulatory framework to introduce new products into the railway environment due to potential safety and risk concerns,” Ravitharan said.
“Innovation has to go hand in hand with clear standards and guidelines to support the implementation of new technologies into any railway operation.
“IRT is a major contributor in standards development groups broadly in Australia and is a key member of the development group now drafting a new standard for alternative material sleepers (AS1085.22) by the Rail Industry Safety and Standards Development Board, for consultation and introduction into the Australian railway environment.”
Ravitharan notes that a paper presented by IRT researchers at the Railway Technical Society of Australasia Conference on Railway Excellence in 2018 gained the attention of the Rail Industry Safety and Standards Development Board, which has led to the Richmond station trial and the drafting of the new standard.
Circular future
Whether it’s in infrastructure or elsewhere, the move to create value out of what was once waste and move towards a circular economy seems likely to continue.
Time will tell how rapidly recycled plastic sleepers are adopted by state governments and others.
Ravitharan believes engineers will be crucial to the success of this adoption.
“We need to really invest heavily on the development of engineering capabilities well before we start thinking of capital projects,” he said.
“For me, I think engineers are extremely important in the development and creation of new technologies and innovations for the railway industry, and it’s a profession which has to be nurtured and continuously developed.”
Northern trial
Ravitharan said that though the interest in alternate materials for sleepers came initially from tourist and heritage railway operators, the technology has since gained attention from Queensland Railways (QR), who began exploring the development of a new sleeper suitable for QR operations.
“IRT was approached to assist Integrated Recycling in the preparation of documentation with the use of alternative composite sleepers for this particular tender,” he told create.
Investigations on the possible suitability of Duratrack sleepers are underway in Queensland, with 150 sleepers installed in October and in November 2018 for in-track trials east of Toowoomba between Helidon and Gatton, and in the Western Downs region between Chinchilla and Miles.
Two other companies have qualified for in-track testing with QR. These tests are expected to finish by the end of 2020, according to QR Post-trial, QR plans to replace 700,000 hardwood timber sleepers.