As the global race for sustainable energy intensifies, this Australian company is perfecting the art of separating hydrogen from water using only direct sunlight.
There is nothing new or revolutionary about the concept of splitting water to produce hydrogen. As a process this is relatively easily achieved, but rather energy-intensive.
Recent projects have focussed on the production of green hydrogen using renewable energy to power the process. The infrastructure required to do so adds significantly to the cost per kilogram of the resulting product, often bringing the final product as high as $8 per kilogram.
But what if no external source of energy was required at all?
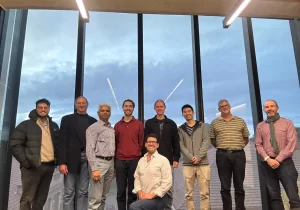
A team at Sparc Hydrogen, led by project manager Vinodhan Gopalan MIEAust, is just two to three years away from commercialising technology that utilises the photocatalytic process.
Rather than using solar or wind power, this process involves the use of direct sunlight to split drinking-quality water into hydrogen and oxygen.
How does photocatalysis work?
“With today’s technology, the sun shines on solar panels, converting light to electricity – which is then channelled into the electrolyser to split water into hydrogen and oxygen,” said Dr Jimmy Lea FIEAust CPEng. Dr Lea, who conducted a Master of Engineering research project on the photocatalytic splitting of water into hydrogen and oxygen, helped to lay the groundwork for understanding variables affecting photoreactor efficiency.
“You then grab the hydrogen, pump it into a fuel cell, it converts back into electricity, and then you drive the car,” he said.
This method involves several complex energy conversions, each contributing to inefficiency and added cost.
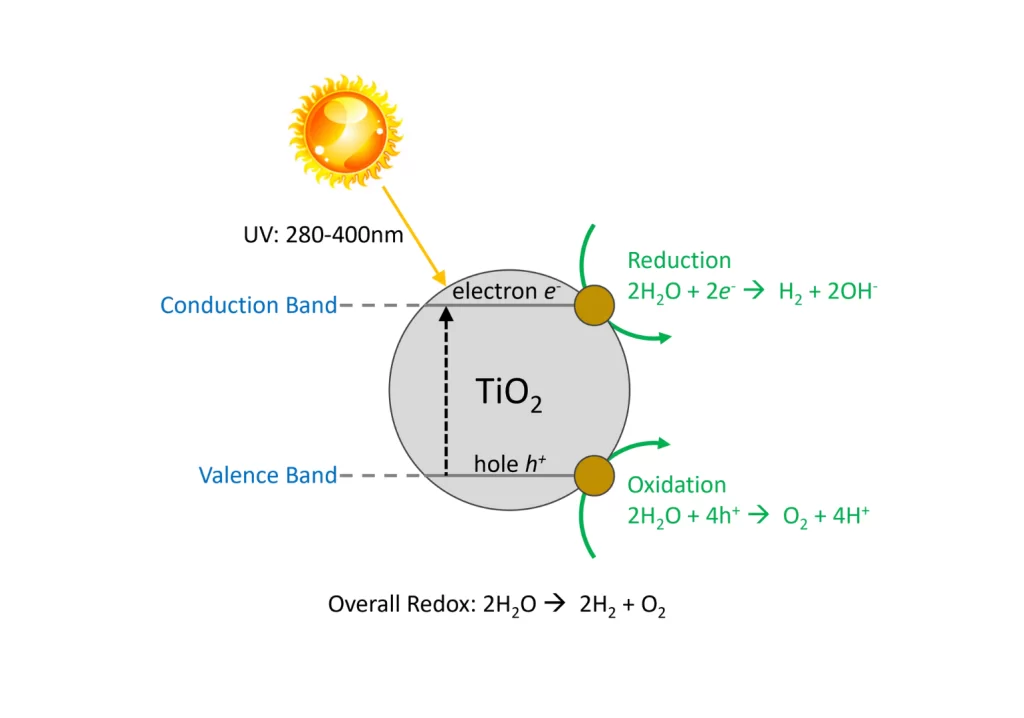
“In contrast, emerging technologies like photocatalysis streamline the process, reducing energy losses and providing a much more efficient alternative,” Lea added.
The process of photocatalysis works via sunlight hitting the reactor – the photocatalyst – which causes bubbles of hydrogen and oxygen – still combined in gaseous form. It negates the need for an electrolyser and the energy infrastructure required to drive it.
“The photocatalyst we’re using is in a form where it’s simply painted onto a surface,” said Professor Greg Metha, Acting-Director of the Centre for Energy Technology at the University of Adelaide, and Lead Researcher at Sparc Hydrogen.
“You have a layer of water over the top, expose it to sunlight, and bubbles of oxygen and hydrogen come off,” he said.
Because everything is reduced to the size of a nanoparticle, there is no separation between the cathode and the anode that the gas evolves off.
“It’s a combined gas, unlike in electrolysers where you’ve got hydrogen coming off one electrode and oxygen coming off another,” Metha said.
“In photocatalysis, both bubble off together. But they don’t recombine, because there is an activation barrier to them recombining.”
What is this photocatalyst? Various research groups are looking at different materials now, to find the most efficient material.
One such material, Lea said, is titanium dioxide which, in its original form, functioned as a photocatalyst but had low solar-to-hydrogen conversion efficiency.
As a result, various research groups sought either to discover other photocatalysts with higher conversion efficiency, or to modify the properties of titanium dioxide by doping it with other elements or increase its surface area to enhance overall conversion efficiency.
How the photocatalyst does its job
Titanium dioxide can absorb light energy and generate electron-hole pairs, Lea said.
“When the photocatalyst is exposed to sunlight, particularly ultraviolet light with wavelengths between 282–400 nanometres, it absorbs photons,” he said. “This absorption excites electrons from the valence band to the conduction band, leaving positively charged holes in the valence band.”
Effective separation of the excited electrons and holes is crucial to prevent their recombination, Lea added. The structure and surface properties of the photocatalyst material are vital for efficient charge separation.
“The separated electrons and holes participate in redox reactions,” he said.
“The electrons reduce water molecules at the surface of the photocatalyst to produce hydrogen gas, while the holes oxidise water molecules to produce oxygen gas.”
The hydrogen and oxygen gases produced in the redox reactions are collected separately.
“This can be facilitated by designing the photocatalytic system with appropriate compartments or membranes to prevent mixing,” Lea said.
Success is about great engineering
While the Sparc Hydrogen team, a partnership between Sparc Technologies, Fortescue and the University of Adelaide, are very interested in working with the most efficient photocatalyst, they are focussed more deeply on engineering an entire system for commercialisation.
“We’re just about to embark on what we’re calling Stage Two, a two-and-a-half-year pilot project. After that, we intend to go pre-commercial,” Gopalan said.
Stage Two is about designing a system where costs can be kept to a minimum.
The team knows that operating expenses will be low. After all, that is the purpose of the technology, to remove such expense.
Now, they’re designing a system that can work with clean, but not necessarily purified water, and even potentially cleaned sea water. The estimate is that the process would use the same amount of water as an electrolyser system, or a little less.
“The big challenge right now is the efficiency of that photocatalyst material,” Metha said. “There have been a few techno-economic assessments done saying that we need the efficiency to be somewhere between five and ten per cent.”
To put it in perspective, a photovoltaic system is about 20 per cent to 25 per cent efficient, he explained.
“For us, the photocatalyst needs to only be half that because we don’t have the capex of the electrolyser, nor the cost of the electricity,” Metha said.
“The theoretical maximum efficiency for photocatalysis is 28 per cent, which is many times greater than what we need to cut through to a hydrogen price of $2 per kilogram.
“We need to demonstrate what the plant is going to look like, so that’s where our work is focussing. Our commercialisation manager here at the university likens it to us designing a car that is agnostic to the fuel.”