A unique, high-capacity retention system has kept a prestigious waterside development safe and on schedule, despite the challenges for design and construction engineers to overcome.
When it is completed in late 2025, Isle, a 25-storey residential tower overlooking the Brisbane River, will contain 124 luxury apartments and a three-level basement.
The development is being built by a leading Australian property group as part of the city’s prestigious Newstead Waterfront precinct.
The developer needed a large-scale and cost-effective shoring solution to support construction of the basement, so it engaged and partnered with Coates Engineering Solutions to deliver a comprehensive internally braced hydraulic retention system.
“The sheer scale and complexity of Isle means no other temporary works shoring provider could have offered a proprietary solution,” said David Dragicevich, Coates’s National Technical Engineering Manager.
“The quantity of materials required and extreme loads we had to support meant it was beyond the capability of any proprietary system in Australia. We had to procure new equipment from overseas which had never been used on these shores.”
Unrivalled expertise
Coates is Australia’s biggest equipment hire and solutions company, and supports multiple industries including mining, infrastructure and construction. It also provides engineers, project managers and installation experts for end-to-end management of temporary works projects.
It was approached by the developer in June 2022 and began onsite work a year later. It will remain involved until the basement is finished in approximately June this year.
“It’s a very large undertaking that’s further complicated by its proximity to adjacent properties and the fact the basement is below the water table,” Dragicevich said.
“That meant the developer couldn’t easily use soil anchoring in all locations, as that involves drilling holes through the diaphragm retaining wall, compromising its ability to retain water.”
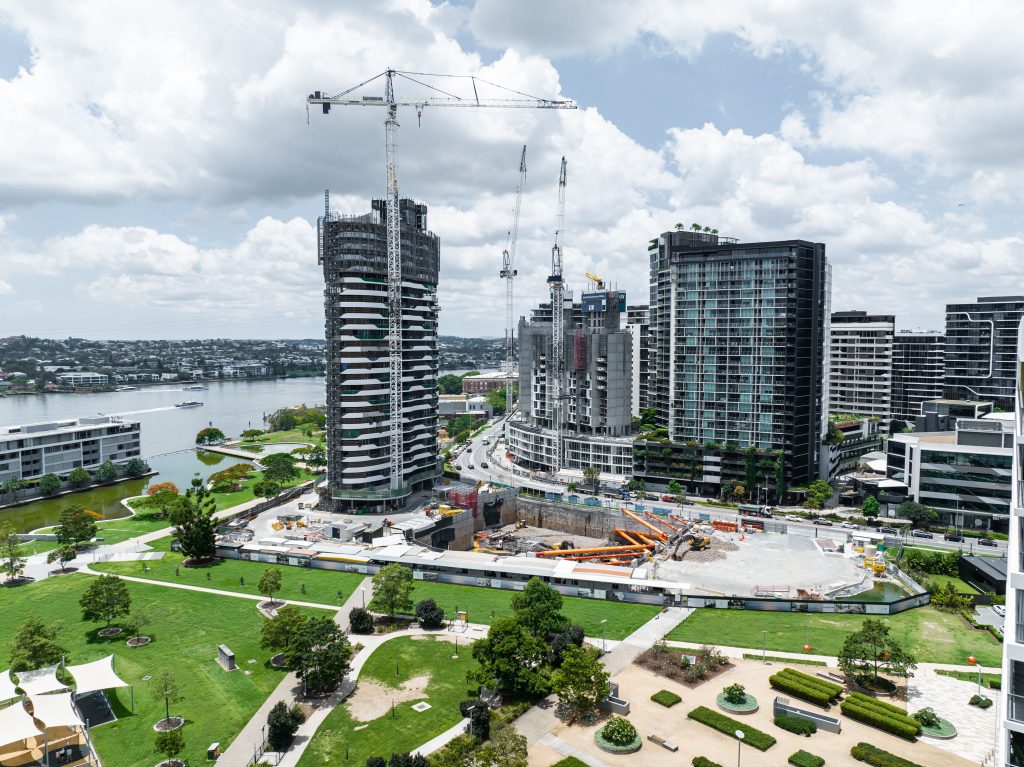
Instead, Coates deployed a proprietary hydraulic bracing solution, the HW500 waler system, which was designed by Dragicevich himself and is the biggest of its kind in the country. Unlike a sacrificial structural steel system, it can be disassembled and used again, substantially reducing costs for the developer.
“We’ve made sure our equipment can be easily removed from the site once the building’s complete,” Dragicevich said.
“To achieve that, we lifted the top level of bracing up above the level of the capping beam, which is very unusual but hugely beneficial as it won’t impede the future construction of the ground floor slab.”
High-capacity solution
The basement’s three braced sides have high loads and 30 m bracing spans, demanding a shoring solution that uses large, high-capacity equipment. The bracing couldn’t be fixed directly to the capping beam due to the reduced levels of the ground level slab, meaning thrust blocks had to be added on top.
Maintaining sufficient access for loading out material made the excavation particularly challenging. In addition to the HW500, 14 hydraulic struts and rams were diagonally braced across two corners, with six on the first basement level and eight on the second.
“The innovation that comes with these struts and the new HW500 waler was essential for designing a solution that was both efficient and cost effective for this client,” said Stephen Reghenzani, Coates’s Temporary Works Engineer.
As the struts are so long, they are subject to thermal loading which needs to be accounted for in the shoring design. This means that as they get hotter during warm weather they expand and push against the shoring wall, generating significant additional load that must be carried by the struts and passed through their connections to the retaining wall.
To combat this, two of the larger MP375 struts were designed to be wrapped in 50 mm thick insulation in case thermal load limits were reached.
“There were some early concerns about coring into this retaining wall to connect the waler,” Reghenzani said. “We worked extensively as a team with the developer and their retention wall designer to agree on the adjustments that were needed, including strengthening parts of the retention wall to compensate for the waler attachment.”
Performance monitoring
Throughout the entire project, the Coates engineers and the developer analysed readings from telemetric sensors to carefully monitor the load and displacement.
“Being able to remotely monitor the forces being applied to the struts and understand their performances in real time provides additional assurance for all parties around the safety of this system,” Reghenzani said.