The daily rail commute for residents across Perth is getting a revamp thanks to skilled engineers who are delivering the next generation of trains in Western Australia.
On the outskirts of Perth, a sprawling industrial complex is playing host to the biggest shake-up of train manufacturing capabilities in Western Australia in nearly 30 years.
This takes the form of the WA Government’s Metronet Railcar project, which will see the construction of 246 new C-series railcars for the Perth metropolitan rail network.
The project — which sees the return of railcar manufacturing to the state — also includes building six diesel railcars to replace the Australind service, which runs south of Perth.
The $1.6 billion project is being led by international rail specialist Alstom and supported by more than a dozen WA subcontractors, which are delivering 50 per cent of the project’s total value with local expertise, facilities and materials.
While components are made at each subcontractor’s existing facilities, all the work converges at the bespoke railcar manufacturing complex in the Perth suburb of Bellevue.
The facility is split into three separate workshops. One is for the assembly of bogies, which mainly consist of the frame, wheelsets and suspension system. Another is for high voltage (25 kV) testing.
Much of the actual train assembly work takes place in the main workshop, with every railcar passing through six distinct stations — assisted by overhead gantry cranes — to undergo specific works.
Station to station
The site team receives the fabricated railcar shell into the workshop and begins at station one by enclosing each railcar with floor, ceiling, doors and windows.
At station two, Alstom’s crews make and test all the relevant looms and fit them along with pneumatic piping to cable trays which run the length of the railcar.
Once fully assembled, the cable trays roll under station two and are affixed to the underside of the railcar shell, thereby making the process ergonomically comfortable for the crews.
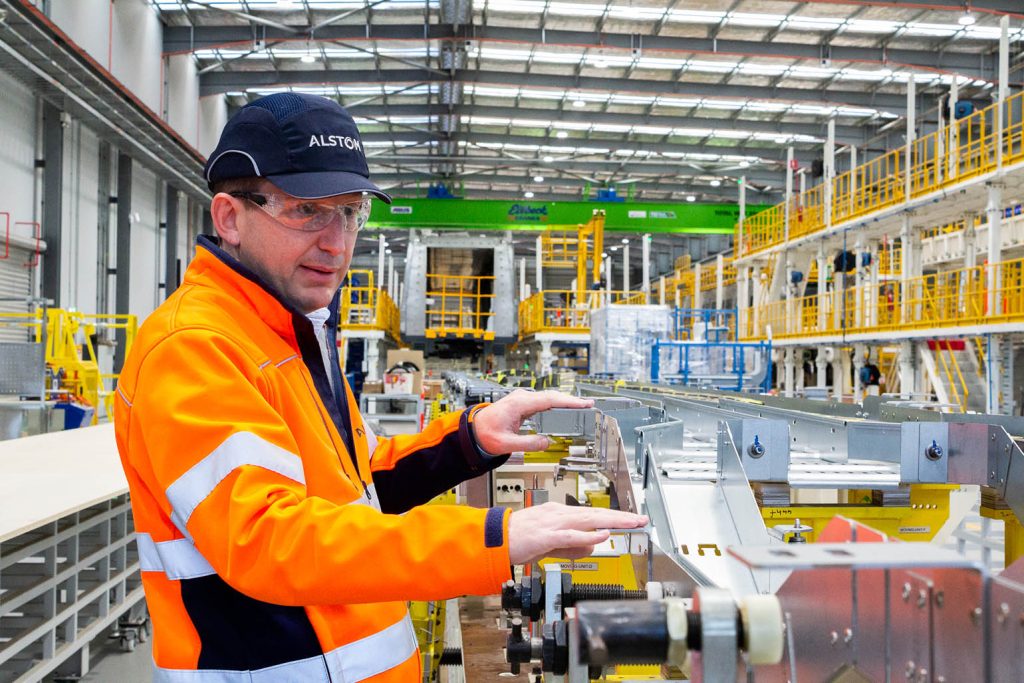
Station three features multi-level scaffolding, which allows for roof access to install air-conditioning systems and underframe access so workers can install traction and auxiliary converters as well as other underframe equipment.
Once the cabling of the railcar has been extensively tested, it is sent to station four and attached with the pre-assembled bogie frames. Exterior signage and final inspections are carried out at station five where the railcars are coupled together to make each set of six cars.
Outside the main workshop, the completed railcar goes through a watertightness test and additional testing in the high voltage workshop. At the time of create’s visit, the Bellevue facility was home to 110 full time Alstom employees, with most staff hired locally.
“The site is still in the ramp-up phase. There will be 150 to 170 employees working in Bellevue by the end of 2022,” Alstom Project Director and mechanical engineer Fabrice Ponti says.
“Much of the team consists of fitters and electricians, as well as manufacturing engineers, quality control engineers, buyers, supply chain specialists, and an extensive project team.
“Our engineers work closely with the mechanical and electrical fitters and electricians in the workshop to ensure the many systems in the train are assembled properly and are working as per the expectations.”
Once Alstom has fully ramped up, it has set a time of six days per car per station. Alstom expects to take three-and-a-half months from the first car shell entering and the completed six-car train leaving the facility.
Alstom has implemented the latest tools and efficient processes, with workers given iPads to manage their activity in the workshop and, for example, log quality issues and missing parts found in a particular fitting station.
“These processes give autonomy to the production team to ensure the right level of quality and efficiency,” Ponti says.
He says their processes are helping with the complex logistics associated with a project of this size. He stops and points to a rack holding small bins filled with components.
“For instance, our smart bins are all on scales and are connected to an app that sends data to our supplier. So when our staff remove components, the scales register that weight change, and our supplier is informed that the corresponding bin needs to be replenished.”
While work in Perth gets underway, Alstom has also set its sights on a portion of the Queensland Government’s Train Manufacturing Program, which is slated to build 65 new six-car passenger trains.
The work includes constructing a $239 million bespoke manufacturing facility in the Maryborough region near Hervey Bay, a rail facility on the Gold Coast and additional stabling and train wash infrastructure to support the new fleet of trains.
Alstom, CAF and Downer Rail are preparing detailed proposals with a successful vendor expected to be named by the end of the year.
Taking shape
Meanwhile, in neighbouring Bassendean, engineering specialist Hofmann Engineering is gearing up to build the vital bogie frames that will connect the trains to the rail network.
Operations engineer Karl Hofmann tells create that the company’s Perth team is set to build 450 bogie frames for the Alstom project.
The international Perth-based firm is no stranger to rail manufacturing, with its Bendigo team having manufactured more than 1000 bogie frames for the Victorian Government’s own metro train and Yarra Tram projects, while its Newcastle facility manufactured UGL’s freight locomotive bogies.
“We have a good pedigree of delivering quality rail components, but we didn’t have a specific bogie frame production line in Perth so upgrading the facility to allow us to manufacture these frames efficiently was the first challenge for us,” Hofmann says.
The company invested $30 million in its local factory, installing a robotic welder, a plate-cutting machine, platebending machines and fabrication equipment for holding together the bogie frame components.
At the other end of the production line, the company has built a fully automated blasting and cleaning facility and a painting facility to properly coat the fully machined components.
“We are also in the process of installing a new gantry milling machine which will be crucial for making bogie frames and other equipment,” Hofmann says.
Hofmann — whose grandfather and great uncle founded the company in 1969 — says while the investment in facilities is significant, the company is confident it places it in a better position to serve other clients in the mining and renewable energy sectors.
“Moving forward we will build the frames utilising about 70 per cent Western Australian materials, with the remaining 30 per cent coming from overseas in the form of raw castings and plate material,” he says.
The manufacturing process will be in the hands of Hofmann’s team, which includes 40 mechanical engineers and electrical engineers who work with a team of boilermakers, machinists and metallurgists.
“There are always new and novel ways of manufacturing, and working with experienced train specialists like Alstom on this project has been a great learning opportunity for us,” he says.
“Likewise, there are procedures that our team in the jobbing shop environment have introduced to the manufacturing process to bring the efficiency up so there is a good exchange of knowledge and information all around.”
Increased demand for engineers
The railcar project is one of many Metronet projects revolutionising the Perth rail network, with the NEWest Alliance, consisting of Downer and CPB Contractors, building the Yanchep Rail Extension and Thornlie-Cockburn Link.
Downer Engineering Manager Graham Holden FIEAust says, “Whether rollingstock or infrastructure, the testing, commissioning and introduction of a new asset into service is always comprehensive, with many stage gates and controls to ensure safety, reliability and excellent customer experience”.
Holden also says Metronet is unprecedented in WA history in its scale and value. “This drives the need for an expanded rail engineering workforce in the state,” he says.
Not only does the industry need more specialists, it also needs leaders and engineers who can address the complicated and complex interfaces both within and between the Metronet projects. “There are enormous opportunities for engineers with the skills and motivation to enable effective integration,” Holden says.
Network integration
Meanwhile, Western Australia’s Public Transport Authority (PTA) is overseeing the entire project and has a dedicated team ensuring the next generation of trains will operate effectively on an existing rail network.
PTA Project Engineer Stephanus Oosthuizen has been involved with the project from the tendering stage. When asked about engineering challenges the team is currently working through, Oosthuizen points to the addition of a third door on each side of the railcars — to help passengers egress faster and reduce station dwell times — as presenting the team with a complex task.
“Our network has some platforms located on curved sections of track, so it means that the middle door will potentially have a bigger gap between the platform edge and the rollingstock compared to the doors at each end of the individual railcars,” he says.
“The PTA are currently evaluating several options to resolve the matter.”
The PTA will carry out testing to ensure the trains are suitable for use by the public. Oosthuizen says all the testing will happen at a railcar level and a train level in Perth on the PTA’s existing passenger network.
“This is already quite unique for us, as our existing A-series and B-series trains were tested in Queensland where they were manufactured,” he says.
The Alstom team will carry out all factory-level testing and static testing at the Bellevue facility.
Starting in the last quarter of 2022, the PTA teams will then oversee tests conducted by Alstom on the trains on isolated sections of the passenger network.
The first trains will commence passenger service in late 2023.
For more of the latest engineering news sign up to create’s weekly newsletter.