The modern desire for low-carbon materials means rammed earth, a paleolithic technology, is enjoying a resurgence in popularity.
This article was originally published in the August 2024 issue of create with the headline “Rammed earth”.
With a known history dating back around 10,000 years, rammed earth is perhaps a surprising contender to be an on-trend building material.
But architects and engineers across the globe are rediscovering and reworking the ancient technique, driven in large part by its promise of ultra-low embodied emissions.
Deep foundations
Rammed earth is a durable – and enduring – construction technique. Landmarks such as Alhambra palace in Spain and sections of the Great Wall of China, constructed centuries ago, are testament to its longevity.
Even today, an estimated 30 per cent of people globally live in earthen buildings, particularly in the Middle East and North Africa, where an unbroken architectural tradition has produced rammed earth buildings up to 10 storeys tall.
In much of the western world, however, concrete has mostly supplanted rammed earth construction, particularly on scales larger than single-family homes.
Low-carbon opportunity
Today, strong sustainability credentials are spurring renewed interest in rammed earth.
Its chief advantage is its abundant availability. Ideally, rammed earth uses soil from the construction site, minimising the amount of material needing to be transported to the site, as well as the amount of spoil needing to be trucked away. These benefits are particularly marked for remote projects.
If unstabilised – that is, not using cement or lime as a stabilising agent – it is infinitely recyclable too. However, many projects built as part of the recent rammed earth renaissance have used stabilisers.
This is partially for the superior performance characteristics – cement-stabilised rammed earth can have up to 10 times the strength of unstabilised – but crucially for the predictability that such stabilisers can deliver. However, using cement and, to a lesser extent, lime can largely negate rammed earth’s low-carbon benefits.
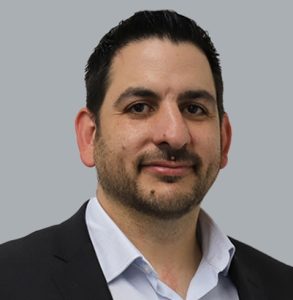
Australian research has found cement-stabilised rammed earth is just 15 per cent less carbon-intensive than traditional brick veneer construction.
In fact, using cement as a stabiliser in rammed earth construction can lead to higher embodied emissions compared to concrete, said Aaron Hazelton, Managing Director of engineering consultancy Indesco, as the greater thickness of rammed earth walls can mean more cement is used.
Australian ambition
Indesco is the engineering partner for the Dairy Road mixed-use precinct under development in Canberra. The project is designed to make use of rammed-earth walls and columns in residential buildings of up to six storeys.
The 14 ha site was the dumping ground for waste from the construction of Parliament House and the National Gallery of Australia, and this soil will form the substrate.
A strong intention to maximise the precinct’s sustainability means avoiding cement and lime stabilisers, which has demanded an advanced engineering approach, UNSW Canberra Associate Professor Jianfeng Xue CPEng said.
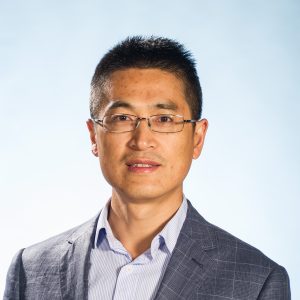
Xue is leading a research project, funded by Innovation Connections and the Australian Research Council’s Industrial Transformation Training Centre for Whole Life Design of Carbon Neutral Infrastructure (DfC02), to develop a low-carbon soil stabilisation testing method for determining the strength of rammed earth structures, as well as develop models for calculating bearing capacities and a carbon neutrality index for unstabilised rammed earth structures made with different aggregate mixes.
“For rammed earth, you need the right type of soil, a bit of clay and a bit of everything,” he said. “But the soil from the Dairy Road project doesn’t have enough clay to build rammed earth structures, so we need to improve its strength with novel techniques of low-carbon embroidery.”
For this project, researchers at UNSW Canberra have been working with Indesco and Precast Projects to investigate using geopolymers and blast furnace slag as stabilisers.
Setting standards
Hazelton said determining the right design parameters for stabilised rammed earth is both the biggest challenge for the project as well its biggest opportunity for impact.
“We don’t want rammed earth to be a standardised product, because so many of its advantages come from how the approach can be modified for site-specific conditions,” he said.
Xue’s research project has so far analysed more than 500 rammed earth samples made using soil from the site. He says suitable design parameters should ensure this level of testing is unnecessary for future projects.
Given the certification hurdles that stabilised rammed earth can present in Australia, some research efforts have focused on creating a low-carbon standardised rammed earth.
Research from the University of Western Australia, led by Dr Alexandra Meek in 2020, investigated a range of potential rammed earth mixtures made from recycled construction waste (crushed brick and concrete), and industrial byproducts (blast furnace slag, fly ash and silica fume), stabilised with sodium hydroxide or hydrated lime.
Meek found these methods could reduce the carbon intensity of Australian house construction by up to three quarters.
References
Niroumand, H. Zain, MFM. Jamil, M. Niroumand, S. Earth Architecture from Ancient until Today. Procedia – Social and Behavioral Sciences. 2013
Meek, A. Elchalakani, M, Beckett, CTS, Grant T. Alternative stabilised rammed earth materials incorporating recycled waste and industrial by-products: Life cycle assessment. Construction and Building Material, 2020.
Tuckey, J & Damda E. From the ground up: What you need to know about building with rammed earth. Architecture Today, 2023.