When part of a vital regional river crossing collapsed, engineers raced to design a replacement bridge that could withstand heavy flooding.
Key points:
- Following the collapse of the Fitzroy River Bridge, Main Roads Western Australia, design engineers and contractors banded together to develop a new approach.
- The revised design increased the length of the bridge while reducing the number of piles driven into the riverbed.
- The bridge was launched incrementally to expedite construction, with many parts fabricated offsite.
The Great Northern Highway in Western Australia’s Kimberley region provides a vital overland link between Broome and Darwin.
When a bridge over the Fitzroy River 400 km east of Broome was severely damaged during flooding caused by Tropical Cyclone Ellie in January 2023, engineers raced to design and build a replacement bridge that could withstand heavy traffic, adverse weather forces and flooding.
The team managed to deliver the project an entire six months ahead of schedule and in time for the start of the following wet season.
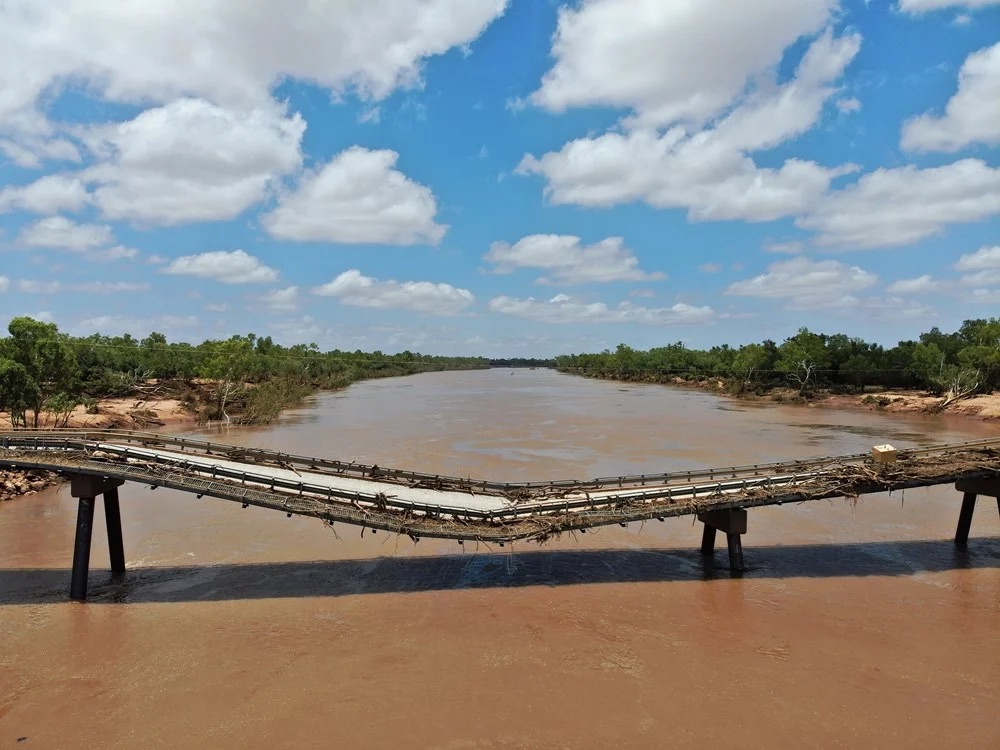
Ready to launch
The Fitzroy Bridge Alliance, which is composed of four parties – Main Roads Western Australia, BG&E, BMD and Georgiou – was responsible for design and construction across the project’s lifecycle.
It was a team effort from the beginning, according to Emir Muhlisic CPEng MIEAust, Associate Director at BG&E.
“BG&E was engaged by Main Roads Western Australia at the end of January 2023 as lead designers to develop a preliminary concept for the Fitzroy River Bridge disaster recovery project in the Kimberley,” Muhlisic told create. “When we first visited the site, what was important for us to understand was the ferocity of the damage caused by the flood.
“The power of the Fitzroy River is hard to describe unless you witness it in person. Even though the river level was much lower than it had been during the flood, the river’s flow was still quite fast.”
This understanding of the natural conditions influenced the design of the new bridge.
“When we examined the length of the river, the times of the year the river floods, and how long we’d need to construct the bridge, it was apparent that we needed to launch the bridge,” Marcus Toleman CPEng MIEAust, Senior Bridge Engineer at BG&E, explained.
“This would ensure there wasn’t a risk that the water level would come up before the bridge had been completed and stop work onsite because the superstructure could not be launched over the flooded river.”
By assembling the bridge structure on the bank of the river and launching it incrementally across a line of piled foundations secured into the riverbed, construction could occur both onsite and offsite, increasing the speed of the project.
“The benefit of this method is that you can do all the superstructure deck work while you’re still building the substructure,” Toleman said.
First, a three-bay launch area was arranged on the western embankment, according to Rowan Dillon, Construction Manager at BMD.
“In one bay we were assembling steel,” Dillon told create. “In the next, we assembled the formwork and deck reinforcement, and poured the deck.
“It was all about doing as much fabrication offsite before loading onto a truck and transporting up to 2500 km from fabrication shops in Perth. Imagine two 1200 mm I-beams braced together; three of those arrived and these were then braced together onsite, forming a six-beam superstructure.”
But the relative speed of onsite construction was still dependent on external factors, Toleman added.
“The bearings required a long lead time, because they were designed and fabricated in Victoria and had to come to the site via Perth,” he said. “We were able to install the permanent bearings with a special launch plate on top, which the launch bridge slid across. But we couldn’t start that until the bearings arrived.”
The bigger the better
Given the bridge’s location, it needed to be technically designed to survive for 2000 years – but the impending arrival of the wet season required it to be finished within the space of months rather than years.
“When we were starting to plan and procure the steel pile casings, we had no geotech information at all; we had very limited data,” Dillon said. “So we designed the biggest piles possible.”
The amount of work conducted in the riverbed needed to be minimised.
“To give an idea of scale, the previous bridge was a 10-span bridge – but it was approximately 100 m shorter than the new bridge, which is only an eight-span bridge and 270 m long,” Toleman said. “One of the key things we wanted to do was make the spans as long as possible to minimise the piers we had to install in the river.
“Historically, and especially in the Kimberley, bridges have been made out of concrete. But due to the complexities of the launch design and the remote location, it wasn’t considered possible to build a concrete bridge in such a short time. As a result of this, we needed to design a steel-concrete composite bridge.
“REDCOR® weathering steel was used for the Fitzroy River Bridge because it requires less maintenance than galvanised steel. This is particularly important for a bridge in such a remote location.”
Dillon summarised his time on the project as rewarding in more ways than one.
“For construction engineers, this has been a dream job, being able to have an influence and work alongside the design engineers,” he said.
“We may have a different lens on things, but being able to work together to achieve the same purpose created massive time saving – and so much work was done upfront to get that right.”
For more from create digital, check out the below:
- Could robots help sift through construction waste?
- Five countries using land reclamation techniques
- From bushfires to flooding, this civil engineer has seen it all.