It’s been 15 years since Rio Tinto successfully pioneered the world’s first remote operation centre in mining. Since then, technology has allowed for advanced automation and AI to optimise operations and safety.
When Rio Tinto pioneered the use of a remote operations centre (ROC) in mining in 2008, the main goal was to enhance productivity at their Pilbara operations, which was undergoing a major capital expansion program at the time.
It was a strategy that used advanced monitoring and control technologies to optimise operations from afar, and shaped the way for the ROCs widely used today.
As technology has developed, ROCs have continued to change mining operations by integrating automation, AI and real-time data analytics. Specific technologies, such as automated haul trucks and drone surveillance, have improved operational efficiency and safety, and the shift towards intelligent integrated remote operation centres (12ROCs) has also transformed the workforce, demanding new skill sets in automation and data analysis.
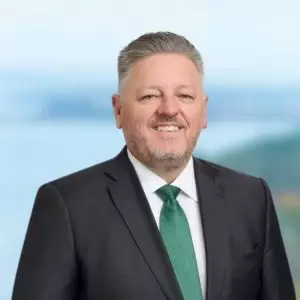
For Greg Lilleyman, mining director and industry consultant, who was involved with the Rio Tinto ROC from the start, in the beginning it was less about adopting new technology; it was more about centralising visibility over the entire iron-ore production system and adding capacity to operations.
“We were developing the ROC concept at the same time as we were embarking on a massive capital expansion of the Pilbara operations at Rio Tinto,” Lilleyman told create. “So, the ROC was seeking to add even more throughput than the capital program would otherwise have delivered.
“This was the true key to the change we undertook with the ROC. It wasn’t really about new technology, but about new operating and management processes to optimise the whole system. The payback from an investment perspective was that we felt we would get more tonnes through the system without having to do any physical upgrades to the network in the Pilbara.”
Through the ROC, the team was able to optimise the use of the truck monitoring systems, which were Komatsu technology (now known as Komtrax) by placing experts in the ROC who monitored engine performance, and made informed decisions to guide the maintenance team onsite. Some new technology was also introduced to help with tracking and charting traffic.
Following the success of the first ROC, Rio Tinto went on to launch an automated hub in Perth 2010, which controlled its rail systems, infrastructure facilities and port operations, 1500 km away from the site.
Lilleyman notes that while technologies such as communication systems, cybersecurity measures and fibre optics have all seen improvements, these upgrades are applicable to both ROCs and traditional onsite control rooms. The fundamental technology remains consistent regardless of the setting in which it is used, he said.
“They are much more sophisticated now and very embedded into the way the whole system is run.”
Intelligent integrated ROCs
Today, most major mining operations across the globe rely on ROCs, which have evolved into Intelligent Integrated Remote Operations Centres (I2ROCs), incorporating AI and predictive analytics.
A 2020 McKinsey & Company report noted that mining companies had shown increased interest in ROCs as a strategy to safeguard employees and maintain operations during the pandemic.
The report looked at a survey from MST Global (now called Mine Site Technologies following an acquisition by Komatsu in 2022), a leading digital technology provider for the mining sector. The survey shows some companies had relocated around 15-20 per cent of their onsite workforce to remote locations by setting up “control towers” to oversee operations, enabling non-frontline roles to work remotely.
Others have gone even further, introducing 12ROCS to create a digital ecosystem underground, connecting all hardware and third-party integrations into one platform that provides real-time data anywhere and at any time.
“Some companies have implemented cloud-based systems that aggregate site data into a single data lake that can be accessed, analysed and visualised for decision support, creating a ‘room of screens’,” the McKinsey & Company report stated. “Other companies manage and actively control plant automation systems, fleet management systems and remote-controlled machines from the ROC.”
“The most sophisticated companies manage all these functions on a larger geographic scale, covering the value chain from end-to-end, optimising post-processed ore logistics and port facilities used by multiple mine sites within a region, with regional parts and supply warehouses monitored across multiple assets for supply-chain optimisation.”
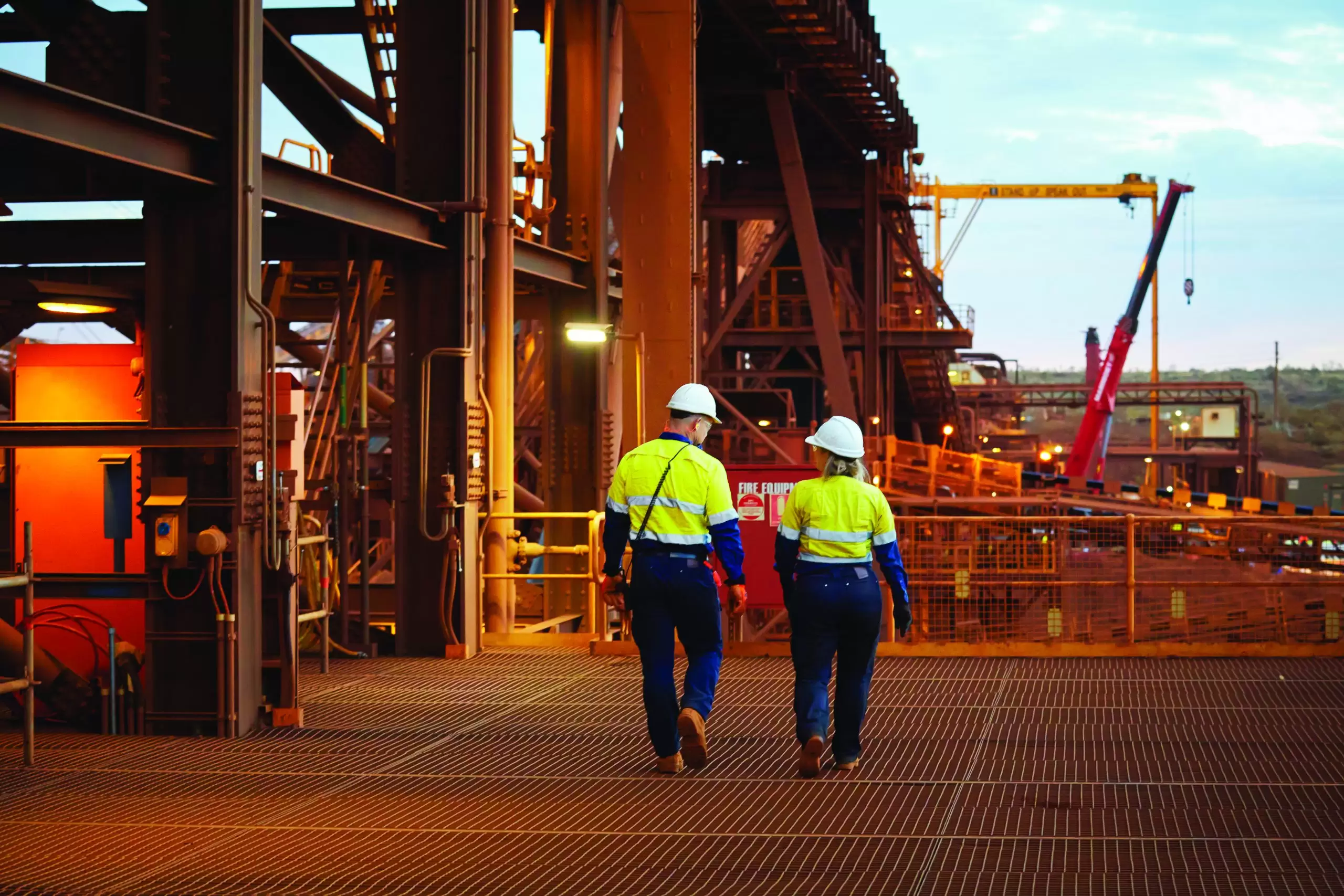
These technology advancements have built on the original concept for ROCs, Lilleyman said.
The things that would have changed are the operating and management processes, and perhaps some of the decision support tools that management uses to continue to optimise the overall system capacity.
“Our very first step on the journey to the ROC was demonstrating we could run the West Angelas process plant control room from Perth, and then the West Angelas pit control. After that we expanded to include Yandi and Hope Downs in what we dubbed the EPROC [East Pilbara Remote Ops Centre], which was in the CBD right outside my office.
“It is pleasing to look back now and note that each of the other major iron-ore producers went on to develop their own version of the ROC. So we certainly led that change and adoption by others.”
Find out how remotely operated vehicles improve safety in underwater engineering operations.