Western Australian agricultural engineers have added a novel piece of technology to the farming industry’s arsenal against increasingly resilient weeds.
Farmers will speak at length about their constant battle with weeds.
While weed control solutions vary significantly throughout Australia, tactics are expensive, time-consuming and, in the case of herbicides, prone to creating increasingly resistant weeds.
In recent years, a team of agricultural engineers from the University of Western Australia (UWA), together with agricultural scientists from the University of Sydney, has developed an innovative mechanical solution that provides an alternative to herbicides.
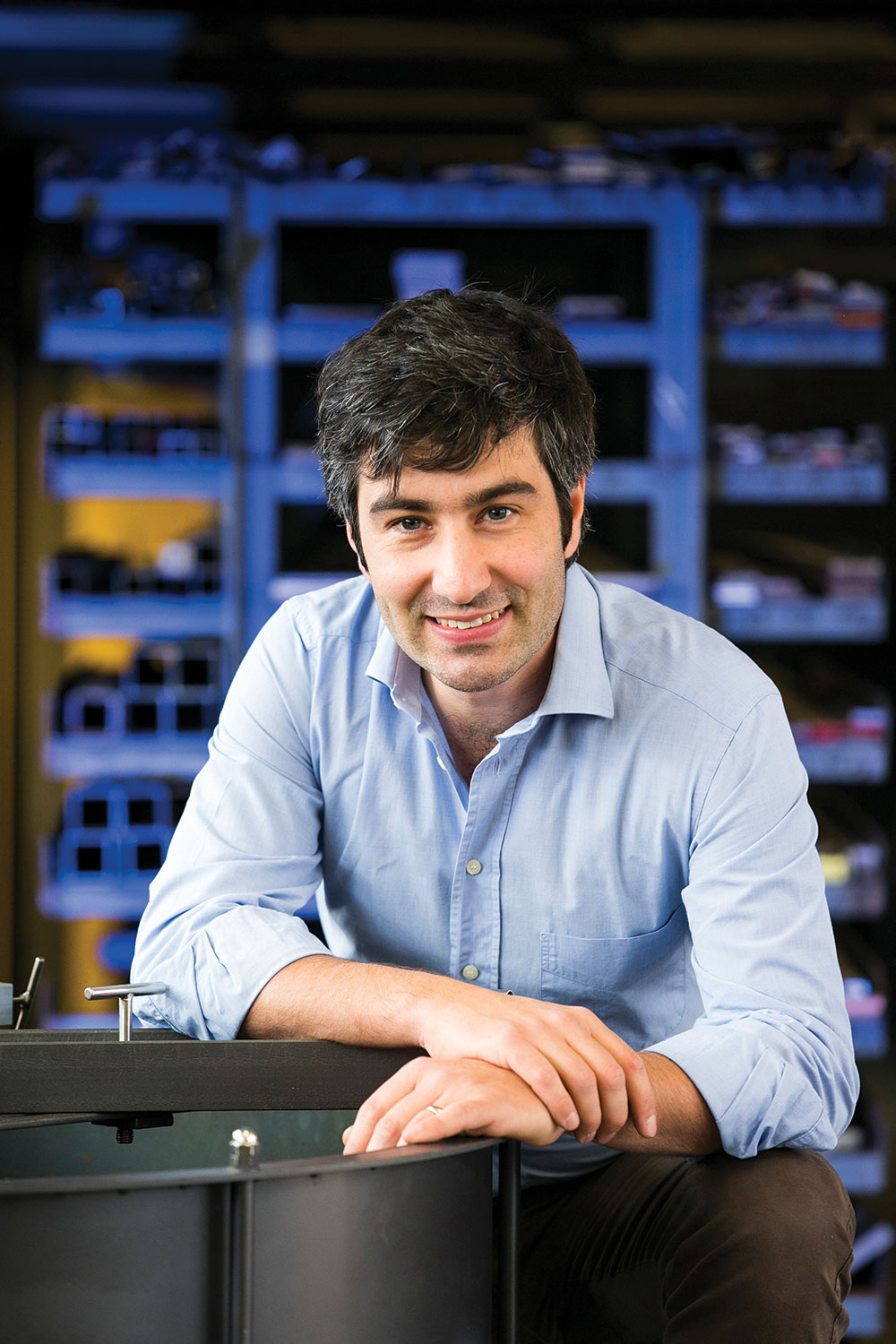
The project was undertaken by a multiskilled team of researchers, growers and industry representatives, with the engineering efforts led by Dr Andrew Guzzomi, who, in 2019, was appointed as UWA’s first ever agricultural engineer.
“While this discipline is common in Europe and the US, there is a lot of potential in Australia for agricultural engineering, which involves applying engineering and technology skills to an agricultural problem,” Guzzomi said.
A prime example of this is the development of the Weed Chipper, a device that consists of mechanical tines or hoes controlled by a hydraulic system.
The Weed Chipper is based on a modified cultivator such as the Shearer Trash Worker, which is hydraulically powered and towed by a tractor like many other conventional pieces of farming equipment.
The Weed Chipper’s tines are designed to remain in stand-by position above the ground and when triggered, dig into the soil and “chip” out the weed before returning to a stand-by position. The tines are activated when a weed is detected by using a commercially available Weed-It sensor that detects reflected light from green plant material.
Because this and other commercially available sensors cannot discriminate between crop and weed plants, the Weed Chipper is currently only suited for weed control in fallow paddocks where all growing plants are considered weeds.
The signal from the Weed-It sensors actuates the valves, which initiates the rapid pressurisation of the hydraulic ram that, in turn, engages a weed-chipping tine.
The rapid weed-chipping operation is completed within 0.3 seconds.
The result ensures minimal disturbance to the soil in a fallow paddock, enabling farmers to maintain a conservation cropping program while removing weeds without the use of herbicides.
The team conducted multiple weed-kill efficacy trials using standard V-shaped sweeps, but determined they did not effectively control weeds across the entire width of the sweep and so designed their own novel sweeps.
“Our design incorporates a flatter, leading edge that engages with the soil like a hoe would, proving to be more effective in removing the weeds from the soil, whereas weeds were more likely to glance off the side of standard sweeps,” Guzzomi said.
“We demonstrated very high weed-kill rates for plants from the two-leaf stage up to plants that were 70 cm in diameter that herbicides would not readily control.”
The pre-commercial prototype is 6 m wide and features 17 tines that are designed to dig into the ground and retract while the device travels at about 10 km/h.
Market ready
Guzzomi said he wanted the Weed Chipper to be accepted by the market as quickly as possible, so he took a retrofit approach, where a widely available cultivator and tine system was modified.
“The overall package of the Weed Chipper is similar to existing products that farmers are familiar with, and using commercial off-the-shelf components like this is quite practical as there is widely available maintenance and repair support in place for these systems,” Guzzomi added.
The team has tested the Weed Chipper in low-density weed conditions where there is roughly one weed every 10 m2, similar to locations in which spot-spraying is used.
“These variables governed how we re-engineered the Shearer Trash Worker tine module to activate, chip the weed out and return to standby mode inside of a metre of travel,” Guzzomi said.
UWA agricultural engineer Dr Carlo Peressini was primarily involved with the development of the Weed Chipper’s tine module, enabling it to complete a full cycle within the established parameters.
Peressini told create he first defined the various tine positions throughout a full cycle, such as closed, stand-by, max torque and bottom position, and identified the active forces at play in the stroke-reload phases of the cycle.
In order to maximise market uptake of the Weed Chipper, the tine module repurposing was achieved with minimal kit parts and commercially available components where possible.
The system was designed to integrate with existing Shearer Trash Worker components, so the stroke phase of the cycle had to be performed using the existing hydraulic system.
The engineers worked closely with David Nowland Hydraulics to adapt the hydraulics for this new application.
The design also took into account the compact geometry of the original module and, in order to minimise the soil perturbation, Peressini said he had to account for the masses and inertia of components so that he could perform the stroke-reload cycle as quickly as possible.
“We implemented a spring arrangement, as this was the easiest solution for performing the tine-reload phase, because the springs store energy during the stroke phase,” he said.
In order to design the overall spring system, Peressini had to determine the load-deflection curve by estimating the required spring stiffness, known component weights and hydraulic resistances in the reloading phase and the related angular displacements of the tine.
Combating resistance
University of Sydney Director of Weed Research Dr Michael Walsh worked with Guzzomi, Peressini and a group of innovative growers to flesh out the idea that would eventually evolve into the Weed Chipper.
The initial concept was conceived while Walsh was working at UWA during a visit to the grain-growing region of New South Wales (NSW) and Queensland in 2012, with innovative West Australian growers Ray Harrington, Andrew Messina and Lance Turner. Walsh and Guzzomi went on to secure funding from the Grains Research and Development Cooperation and started work on the project in 2015.
Walsh told create the Weed Chipper was an ideal method of combating agricultural weeds without applying herbicides.
“Previously, there has been heavy reliance on glyphosate to control weeds in fallow paddocks, and these weeds have evolved resistance to this herbicide,” he said. “The cost of herbicide resistance is about $60 a hectare per year in additional weed control costs, so to have an alternate weed control option that reduces herbicide reliance will be a major benefit to farmers throughout Australia.”
There are also mounting industry concerns about the continued availability of glyphosate, given the potential for bans of this herbicide.
Walsh worked on validating the weed control efficacy of the Weed Chipper in field trials conducted in NSW and Queensland. In these trials, weeds such as fleabane, barnyard grass, sowthistle, wild oats, annual ryegrass, turnip weed and feathertop rhodes grass were planted in straight lines at regular distance and time intervals to establish different growth stages.
“We then used single tine test rigs that were tractor three-point linkage-mounted or tractor-towed to evaluate the efficacy of the response tine in controlling the eight different growth stages of these weeds. We found that the device effectively removed all weeds regardless of their growth stage,” Walsh said.
“Excitement is building for implementing physical weed control technologies and it all hinges on the development of better weed recognition technologies to automatically and precisely replicate what the human eye can do.”
Since its development, the Weed Chipper has won broad praise and, in late 2019, the Rio Tinto Emerging Innovation award category at the WA Innovator of the Year awards.
UWA has announced the Weed Chipper is being commercialised in partnership with WA-based company Precision Agronomics Australia, and will be available for sale as a 12 m trail-behind unit in mid-2021.
Swarm thinking
In Central Queensland, a small company is taking a slightly different approach to managing weeds and other aspects of farming operations.
SwarmFarm Robotics emerged in 2012 with a mission to develop agricultural robots to bolster crop production. Their technology consists of small machines designed to couple with commercially available technology to achieve any particular task, including weed control, fertiliser spreading, mowing and slashing.
The company’s SwarmBots are touted as being able to work on their own or co-operatively as a “swarm” of units across any operation, from horticulture to broadacre cropping.
Between 2015 and 2018 the company developed 11 prototypes that helped Australian grain and cotton farmers control weeds by contract spraying more than 15,000 acres of farmland.
SwarmFarm Robotics Field Engineer Tom Holcombe says, in one instance, the SwarmBots had been deployed in the field attached to an optical sensor microwave to manage weeds.
The SwarmBot manoeuvred the sensor and microwave through the paddock and stopped when a weed was detected so that the device could microwave the weed sufficiently to kill it.
“Like a contact herbicide you will see an effect reasonably quickly,” Holcombe said.
“We have had some pretty good results so it’s another tool in the toolbox to be able to use to control weeds, and the beauty of this platform is we are moving away from blanket applications and making decisions on a plant-by-plant basis.”