With the COVID-19 pandemic continuing to have knock-on effects on industries around the world, one Australian engineering firm says it has the answer to parts shortages.
Reverse engineering is the reproduction of a product or part that cannot be obtained by other means. It involves measuring an object and reconstructing it as a 3D-model in computer-aided design (CAD) software, then manufacturing the part.
Jason Leussink, Managing Director of Illawarra-based engineering firm Leussink, said his company first got involved in the process when the local steel mill was facing delays of weeks, if not months, for component parts that wear out over time.
“Reverse engineering can apply to any sized part, it doesn’t really matter,” he said.
“We can run finite analysis on a product to see if we can improve it by making it stronger or more wear resistant. Using CAD technologies, we can apply it to any size or shape product, from something as small as a coin to as large as a building.”
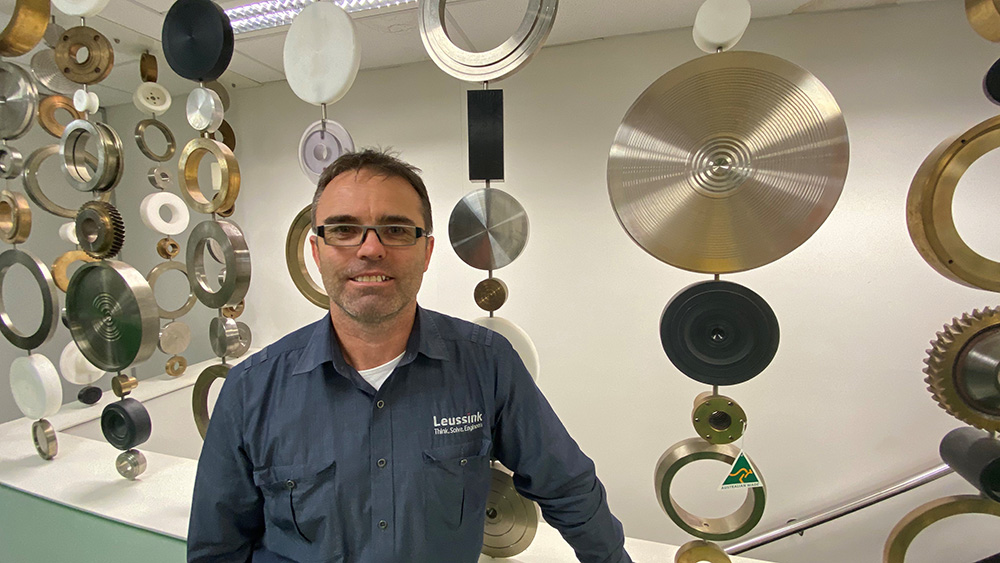
A simple reverse engineering process might involve manual measurement and data collection of a physical model’s dimensions, using hand tools such as micrometers, Vernier calipers and gauges.
“For more complex items we have technologies such as articulated measuring arms, which can measure a component while it is in service,” Leussink said.
“We distribute the Tomelleri Space Arm, which measures the geometry of physical objects by sensing discrete points on the surface of the object with a probe.”
The firm uses either touch probing or 3D scanning, which runs a laser beam over the product. By transferring the product dimensions to software, it not only reduces the risk of measurement errors, but significantly reduces the time required for the overall reverse engineering effort.
“Reverse engineering is particularly applicable where there are machines that can run 24/7 for months on end, repeating the same process over and over again,” Leussink said.
“This type of high use means parts and accessories will need to be replaced regularly, and in some cases major components as well.”
In terms of intellectual property, Leussink said the team always needs to research to ensure they are not infringing on any patents before reverse engineering a product.
“You don’t go and manufacture a whole system. It’s generally just a component which is on that particular system, such as simple bolts, shafts or pins – common items that don’t have any intellectual property restrictions.”
In the past, Leussink said that reverse engineering has largely been used for long-life machinery, where the parts are no longer being manufactured.
But with the COVID-19 pandemic now disrupting the global manufacturing supply chain, he predicts reverse engineering will be in demand for a wide variety of products and industries.
“Companies in Australia have relied heavily on overseas manufacturing,” he said.
“In the past it might have been a cheaper and faster solution to have [a part] made in China, but now it may be more cost effective to do the reverse engineering where you are, and have it manufactured locally.”