Italian civil engineering giant Webuild has unveiled a state-of-the-art, automated factory that sets new benchmarks for advanced manufacturing.
The group, which is constructing the hydroelectric pumped-storage scheme Snowy 2.0, Australia’s biggest renewable energy project, designed and built the innovative facility in Belpasso, a town near Catania in Sicily.
It will make precast concrete segments for more than 30 kilometres of tunnels to be excavated by tunnel-boring machines for a new double-track railway along the island’s eastern coast.
The railway between Messina and Catania is part of a project that will create a 250km/h mainline connecting the island’s largest cities.
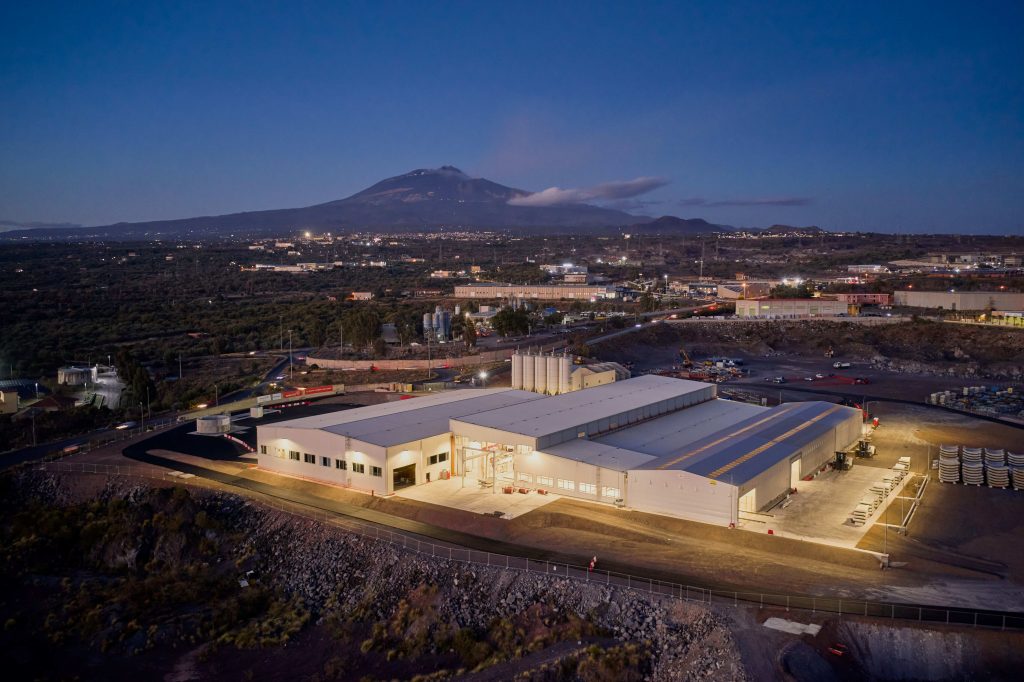
Harnessing technologies
“The most revolutionary aspect of the factory is the bringing together of multiple technologies under one roof,” said Remo Grandori, Webuild’s Director of Plant and Equipment. “Other factories have implemented some of them, but not all of them together.”
By drastically reducing the number of humans required for the most repetitive and arduous tasks, it’s producing the highest quality segments faster while using less energy, effectively raising the bar in an already demanding industry.
The entire process is digitalised, with artificial intelligence taking care of quality control. Each segment has a unique bar code and chip, so its history from factory floor to tunnel wall can be easily traced.
With machines doing the most potentially dangerous activities such as heavy lifting – each segment weighs seven tonnes – the factory is a much safer workplace. Laser-triggered sensors even sound an alarm and shut down operations if a worker strays into a hazardous area.
An infrastructure leader
Webuild is a world leader in major infrastructure projects such as metro and rail lines, hydropower plants, motorways and hospitals. Its 85,000 direct and indirect employees are present on every continent.
In Australia, its works have included Melbourne’s City Loop, the skytrain viaduct and cable-stayed bridge for Sydney Metro Northwest and Perth’s Airport Line. It’s currently working on the tunnel package for the North East Link in Melbourne and six stations and core rail systems for the Sydney Metro-Western Sydney Airport line.
Roboplant is the second innovation devised by Webuild for the production of pre-cast concrete segments. For Snowy 2.0, which will increase generating capacity by 2,200 MW and have 350,000 MWh of large-scale storage for the power grid, it developed the Force-Activated Coupling System (FACS) to strengthen the way segments interlock with each other.
FACS eliminates the need for a second lining along the inclined pressure shaft, which will come under extreme pressure when water from the upper reservoir surges through it to spin the underground power station’s turbines before emptying into the lower reservoir.
Huge efficiencies
The first indication for Webuild that the Belpasso factory was running efficiently was an immediate boost to productivity. Previously, it had taken 10 minutes to produce a segment, but that time is set to be slashed to just four minutes, a 150 percent improvement.
The four robots at the Belpasso factory will boost productivity significantly. It usually takes 10 minutes to produce a segment, but that time will be slashed to just four minutes – a 150 percent improvement – once the factory is running at full rhythm.
There will be seven people working along the production line in each of the eight-hour daily shifts. The total number of workers, including those responsible for quality control, safety checks, loading trucks and other tasks, will be nearly 60.
The robots started churning out segments in December last year, and the rate of production has gradually increased as more workers are trained and test procedures optimised.
“We aim to reach full production very soon,” said Santo Accogli, Senior Manager Plants, Underground and Tunnelling at Webuild.
Enhanced sustainability
The factory was also designed according to circular economy principles to make it as sustainable as possible: it will collect 70 percent of its water needs through recycling and rainfall capture, while rooftop photovoltaic panels will generate 40 percent of its electricity.
Webuild is planning three other plants for other projects in Italy. Once they are all up and running, they will process an incredible 3.5 million m3 of concrete to produce segments covering 300 kilometres of tunnels.
“Roboplant is a great example of how the construction of a project can be as sustainable as the project itself,” Grandori said. “It’s a worthy achievement that we share with our partners, construction firm Pizzarotti, robotics developer CP Technology and Politecnico di Milano University. This factory is the result of collaboration.”
Find out more about engineering opportunities at Webuild in Australia.