With a broad range of cable pits available, it’s vital to look at their intended application from all angles.
Planning and designing cable pits requires consideration of a number of factors.
These include how and where the pit will be used, what it will contain, the levels of security required, how often and what type of traffic will be passing over it.
“When those things aren’t considered in the early stage of the planning process, that’s when things can go wrong,” said Greg Facey, Market Segment Manager, for ACO, a family owned, Australian manufacturer based in Sydney.
Facey was speaking during the recent EA Thought Leaders webinar, Service enclosures, the integration of accessible cable chambers beneath pavements.
What is involved in pit selection?
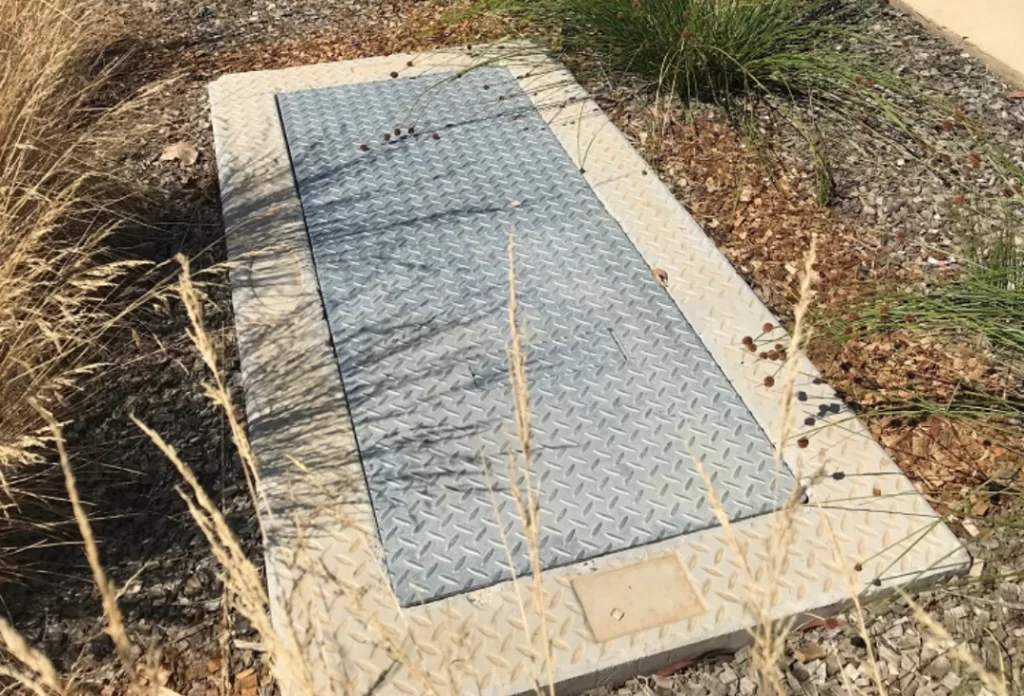
A single cable route can pass through a number of different environments and so every cable pit along the cable route may be exposed to specifically different project criteria. There are five key factors to consider during the selection process, Facey said. This applies universally across urban areas, such as residential precincts, commercial and industrial areas as well as transport hubs.
Those factors are:
- Size of the enclosure
- Location
- Traffic loading
- Safety and security requirements for workers and the public
- Individual user requirements and how the enclosure will be installed
Cable pits consist of two key components, the subsurface chamber that interfaces with the conduits and the surface entry point, comprising the lid, or access cover.
When selecting an enclosure size, what will be contained in the pit should not be the sole consideration. Other factors informing selection are access (practical working area) and the minimum cable bending radius.
Location is most importantly about whether the cable pit should be trafficable or non-trafficable. Non-trafficable might be in a footpath, whilst trafficable might be in a driveway or loading dock.
“We need to consider the anticipated traffic scenario for each of the enclosures,” Facey said. “There might be no anticipated traffic, some incidental traffic or (it might be) regularly traversed by vehicles.”
An important factor that is often overlooked is the type and weight of vehicles that might pass over. (It’s not unusual, Facey said, to see pits intended for a non-trafficable application that have been damaged by trucks and other vehicles during the construction phase).
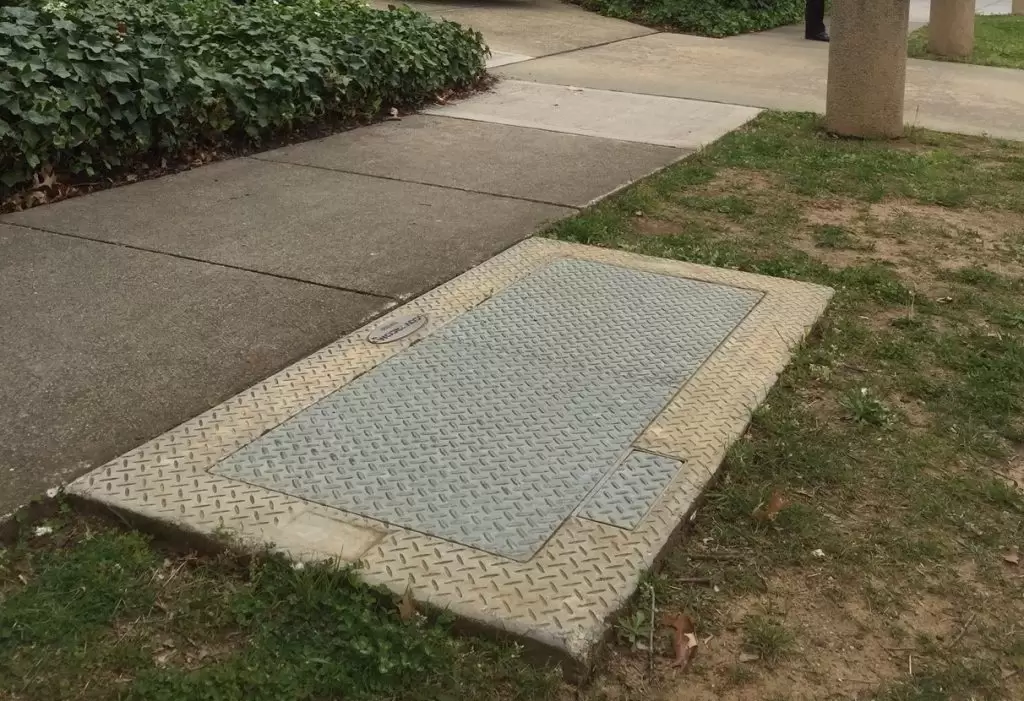
Numerous materials such as non-conductive hard plastics, glass-reinforced concrete, polymer concrete or cast iron are used in the manufacture of lids. A great feature of access covers, said Facey, is that they can be infilled with pavement elements to match or complement the pavement.
Lids and access covers are required to comply with AS 3996. “There is a wide choice of lids and access covers to meet the anticipated load requirements,” Facey said.
Chamber materials are also a vital consideration in areas of low bearing soils and high frequency traffic loads, as well as in environments of potential electrical conductivity or chemical attack. This all informs the durability and safety discussion.
A deeper dive into security
Why worry about cable pit security when in the past it has rarely been an issue?
Increased security requirements are partly to do with better development of safety measures to protect workers and the public. In other words, to protect people from cables and cables from people.
Of course the possibilities of terrorism and cyber-crime also inform a greater need to protect infrastructure and prevent access to lines that carry data.
There have been documented incidents of theft of site materials for resale, including copper. Locking down lids prevents unauthorised access as well as the lids themselves from being stolen.
To meet myriad contemporary scenarios, there are various options and levels of security available, from simple, to high security covers, involving security bolts and padlocks, to government endorsed high-security, tamper-evident locking systems.
“A variety of pits is available in the market now,” Facey said. “Choosing the right enclosure for the right application, particularly during the planning and design stage, is essential to prevent problems and product failures in the future.”
See various case studies here.
To stay up to date with product news, case studies and legislation in this area, subscribe to the specific ACO newsletter of your choice.