An updated advisory from the Galvanizers Association of Australia (GAA) highlights best practices and considerations for repairing field welded or damaged areas.
As the Australian construction industry continues its push towards more circular construction habits, many companies are designing galvanized steel structures for reuse. With this in mind, the quality and frequency of repairs will play an important role when assessing components before they’re reused.
The Galvanizers Association of Australia (GAA) has recently updated its advisory note on Repair of Field Welded Areas and Other Damage, in part due to the discontinuation of the popular Galvanite range from Jotun Paints (the document is downloadable for free from GAA’s technical publications page – sign-in required). The new advisory note contains a range of other options that adhere to Australian Standards.
When it comes to damage, the ideal approach to repair would be to send the components back to the galvanizer to go through the hot-dip galvanizing process again, says Ann Sheehan, Corrosion and Sustainability Officer at GAA. However, while this method ensures the very best outcome, in many instances, it’s not feasible or practical.
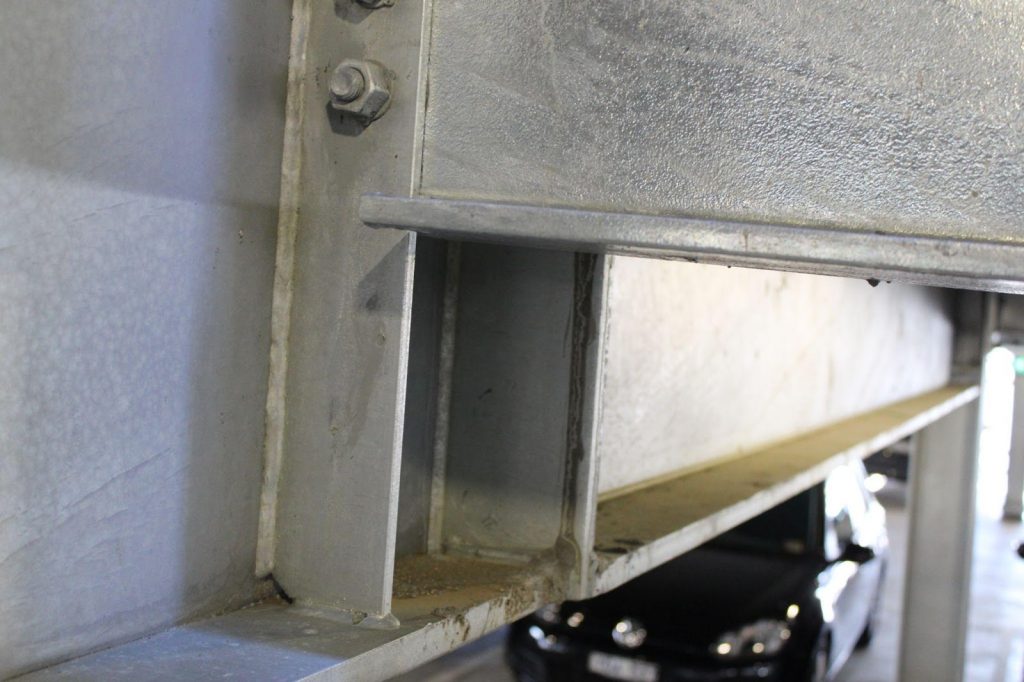
For most field repairs of damaged areas after hot dip galvanizing, the GAA recommends the use of organic zinc-rich epoxy paint. It also recommends using a brush or roller application to help ensure the damage is evenly covered by the required coating thickness specified in the Australian Standards. In some circumstances, zinc thermal spray may also be used. However, repairers should be very wary of using aerosol sprays as a stand-alone repair method.
While Australia’s Standards outlines the amount of zinc required in zinc-rich paints, the international community does not have specifications for this. Our national Standards specify both the methods and the quality of the zinc-rich paints that need to be met for repairs to damaged or field welded areas of galvanized steel.
Some zinc-rich paints are marketed as cold galvanizing products – commonly known as ‘cold gal’ – and care should be taken to ensure that any product used for repairing hot dip galvanizing meets Australian Standards, says Sheehan.
“We do come across a lot of usage of cold galvanizing aerosol sprays, which is concerning. We don’t recommend using this method as these aerosols often don’t have any zinc in them, and even when they do, the coating application is quite thin and inadequate for corrosion protection.”
According to Sheehan, the two main reasons people choose to use aerosol sprays are the convenience of application and the aesthetic appeal, with many advertising a shiny silver tone that will match an initially shiny galvanized article.
“However, in this case, the easier aerosol option does not do the job that’s needed for a full-strength repair that’s up to Standard,” says Sheehan. “The aesthetic win is also a short-lived one, as organic zinc-rich paints applied with a brush or roller will better match galvanized material as it dulls over time. The shinier aerosol paints do not do this, and it ends up sticking out like a sore thumb after a few years.”
Repaired areas of hot dip galvanized steel are normally considered to be ‘most at risk’ of early corrosion because field repairs usually occur in less controlled conditions than factory repairs. An earlier maintenance inspection timeline should be implemented for any repaired areas compared to the rest of the structure.
By paying attention to the quality and efficacy of repairs to damaged areas, engineers and companies can minimise the need for maintenance and ensure their structures continue to serve beyond their intended primary purpose.
For more information about making repairs to damaged areas of galvanized steel, you can download the latest advisory from GAA’s technical publications page – sign-in required.