Chemical engineering students from the University of Queensland (UQ) have helped investigate how sugarcane could be used as a clean energy source to create hydrogen.
Professor Damien Batstone of UQ’s Faculty of Engineering, Architecture and Information
Technology, said bagasse, or sugarcane pulp, and other agricultural residues were an abundant resource that could generate ‘green’ or carbon-negative hydrogen at scale.
Biomass from crushed sugarcane stalks and leaves could also potentially produce hydrogen for under $3 per kilogram, one third of the cost of current options, he added.
Last year, 150 students in 36 teams were tasked with designing a process to produce hydrogen gas from bagasse with either thermal gasification or hydrothermal gasification as their process.
Generating pure hydrogen
Caitlin Welsh, a chemical and materials engineer who has a Bachelor of Engineering (Hons) from UQ, and her team, were responsible for designing a thermal gasification process for an input of 2000 t/day of bagasse.
“I was allocated the pre-treatment node where I was required to design units to heat and dry the bagasse in preparation for gasification,” she said.
“Part of my role was to ensure the bagasse was pre-treated to ensure highest possible efficiency. I needed to do this while ensuring the pre-treatment node did not counter the energy savings in the gasifier.
“So, I applied energy integration in my design by utilising steam produced downstream in my pre-treatment for heating of bagasse.”
Welsh, who is currently working at Visy Board as a graduate engineer, said that, with thermal gasification, there will always be by-products such as ash, tar, carbon dioxide and carbon monoxide gas.
“The hydrogen can, however, be extracted and the by-products captured in the downstream process,” she said.
Eva I Iong Lam, who also has a Bachelor of Engineering (Hons) from UQ, and her team were involved in the cutting-edge hydrothermal gasification process.
“It is similar to that of thermal gasification, except it involves wet biomass,” she said.
“Not only does it save energy in the drying of bagasse, but it also allows for lower operating temperatures with the possibilities to utilise a variety of biomasses as feedstocks.”
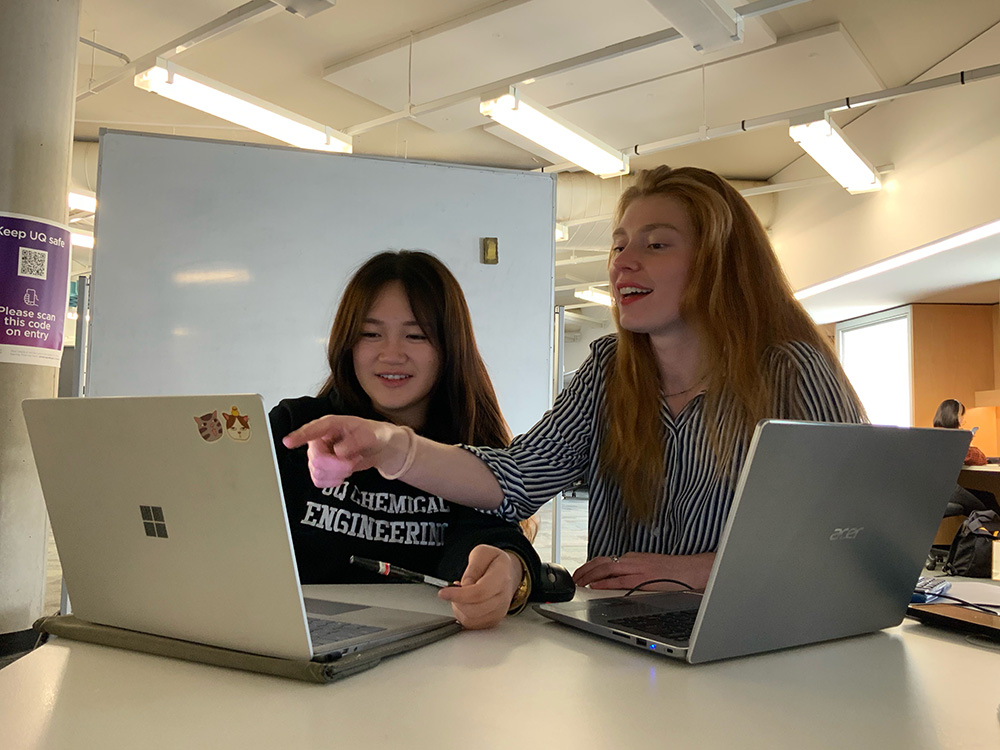
A graduate chemical engineer who now works at Engeny Water Management, I Iong Lam said the slurry was fed into the reactor, then produced a supercritical fluid where its heat energy was integrated with other processing units through a series of heat exchangers.
“Hydrogen is produced more readily under supercritical water conditions in this process,” she said.
“The gases were then separated by chemisorption using Methyldiethanolamine (MDEA) solvent.”
The models she created were also able to recover the majority of water present in the gas streams using flash tanks, so it could be repurposed within the plant.
“A key challenge was the limited availability of materials that could withstand high temperatures and pressures,” I Iong Lam said.
“I chose stainless steel 316 as the construction material for a flash tank receiving supercritical fluids as it has excellent resistance to corrosion, thermal and pressure stress.”
A future biomass technology
While gasification has been widely applied to coal processing, it has not been applied to hydrogen production from biomass at large scale, Batstone said.
“This offers an alternative pathway with potential for higher profits for canegrowers, and for sugarcane to be used in ethanol and plastic production, while fully utilising the biomass residues,” he said.
Welsh hopes that her career will include further involvement in sustainable engineering solutions, while I Iong Lam wants to continue to focus on water consulting.
“You get clean water by just turning on a tap, we never really spend a moment to appreciate the processes and people behind it,” she said. “Now, I am hoping to make a positive difference to the community I live in.”.
To develop the work done by the students, a future project by UQ will involve growers, sugar companies and likely end-users and include governments investing in a hydrogen economy.
I have contact with the CEO of H2X company set to produce Australia’s first Hydrogen Fuel Cell vehicles and he’s very interested in viable sources of Hydrogen. I have also a paper on how to get hydrogen visibly using catalytic separation of sea water using new catalysts I’d be interested in learning more on this
When my vitreous enamel solar water hot water system gave up the ghost after 30 years on tank water, I started looking for stainless steel water tanks systems, and found that these have had a mixed history in Australia. Currently manufactures of such HWS are reluctant to warranty the stainless tanks and others advise against S/S tanks. As a yacht owner and sailor i knew that 316 s/s was very resistant to rust in saltwater, but I had little knowledge about the performance at elevated temperatures.
Eventually I found a new Solar hot water system with Grade 444 stainless steel tank which advised; Compared to traditional Austenitic stainless steel such as Grades 316L and 304L, ferric stainless steels offer life cycle cost advantages. The key to its performance is the addition of molybdenum and chromium as further alloy elements whereas traditional grades use nickel.
In particular type 444 outlasts Type 316L when it comes to resisting localized corrosion or pitting attack at elevated temperatures.
Which may better suit the application envisaged in this article.