Engineers at Monash University have developed a technique to upcycle plastic and old tyres to create a diesel alternative.
Combining fragments of the waste materials using a coffee grinder and then exposing them to intense heat in a process called rapid pyrolysis, the researchers were able to produce an oil without the polluting compounds that would usually result from recycled tyres.
“Scrap tyres are basically waste,” explained Professor Lian Zhang, who led the research. “People either dump it or burn it as a very cheap fuel, and it causes a lot of environmental problems.
“We are trying to turn the tyre … into a number of high-value products. By reacting it with plastic, we can make sulfur-free oil that could be used as a substitute for diesel.”
The plastic used in the process can take the form of low-density polyethylene (LDPE) or polystyrene (PS), encompassing a wide range of consumer goods.
“We tried several plastics … like LDPE, PP [polypropylene], and PS,” PhD student Wahyu Narulita Dewi said.
Whereas previous attempts had combined materials high in hydrogen, such as plastic or recycled tyres, with biomass to release sulfur in the form of gas compounds, on this occasion the researchers tried to make use of the synergistic relationship between plastic and the rubber tyres.
“They have some similarities. For a chemical reaction, normally we think if these two things have a good match, they would do something magical,” Zhang explained.
“If we can put them together and make a valuable product, that’d be really great.”
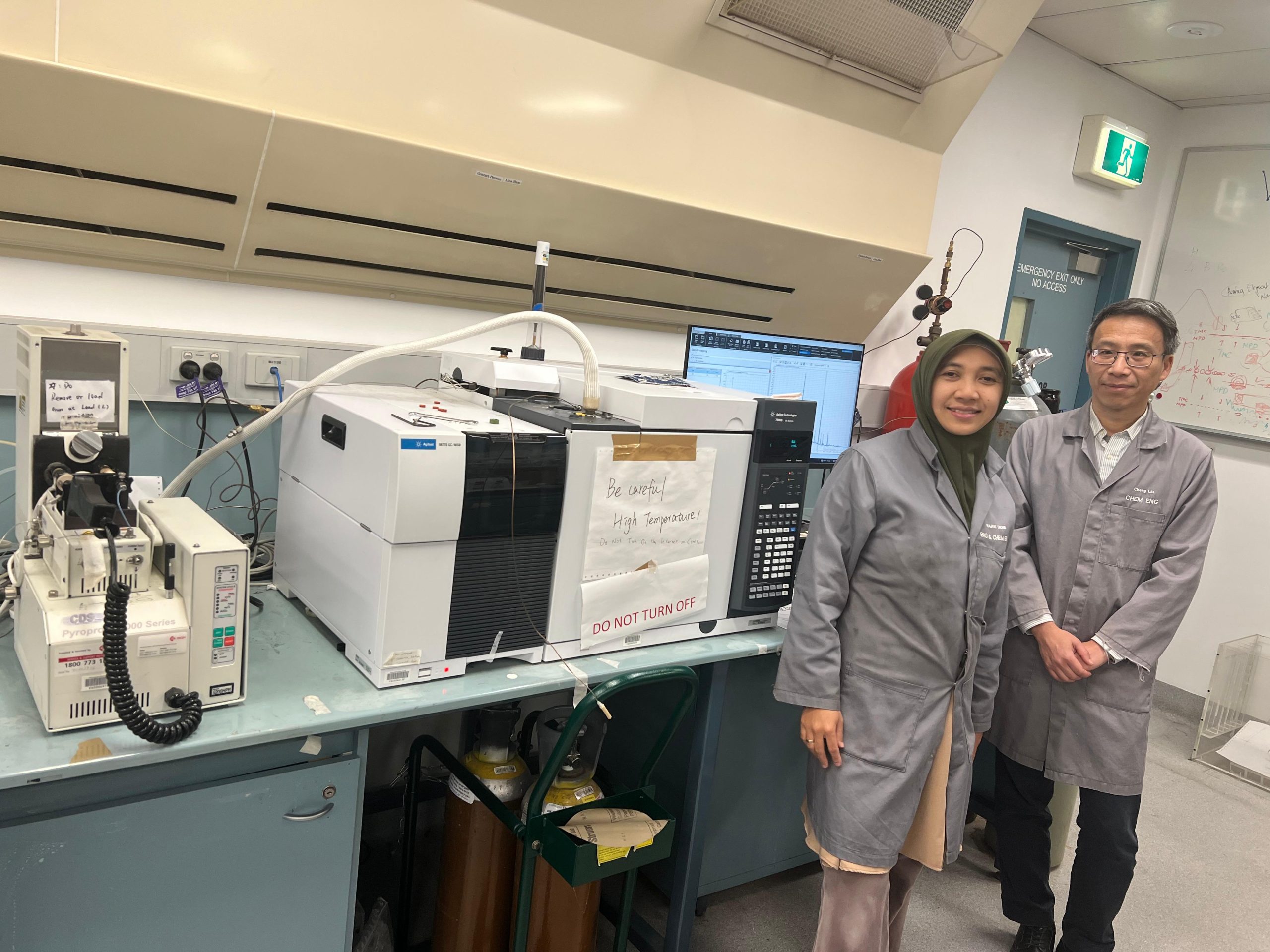
Added sulfur
Even though it is environmentally harmful when recycled, the problematic sulfur is part of the mix for a reason: it is added to new tyres when they are produced to help resist abrasion from the road surface and increase the material’s lifespan.
“So people add a lot of zinc, a lot of sulfur, but later on when you dump them, that turns into something really bad,” Zhang said. “But from a chemical reaction point of view, that sulfur or zinc could be a good catalyst to react with the plastic.”
One challenge the engineers encountered was converting the tyre material into a form that would allow it to be used in the lab.
“We got scrap tyres from the tyre recycling company; we got a mixture of tyres, so it came from truck tyres and passenger cars,” Dewi recalled.
“In our lab we have a micropyrolysis reactor, so the size is very limited – we use only 0.3 mg, so the size of the granules is around 200 to 500 μm. We put it in a coffee grinder to make the small sizes.”
The team also added liquid nitrogen to the mix, preventing the rubber from emitting heat as it was crushed.
“After that, we mixed it with plastic with a certain ratio, and then we put it in a very small tube because we use a microreactor,” Dewi said. “It’s very challenging, especially the first time I tried the reactor out. To get one tube to put into it took maybe one hour.”
As they got more adept at working with the small granules, however, the team was able to cut this time down significantly.
Getting faster
The next task, Zhang said, is to further scale up the process.
“We’ve done lab scale, so we are now trying to scale it up – up to about 10 kg per hour,” he said.
“That’s basically the core of our innovation: how to treat it with rapid pyrolysis so that you can downsize the equipment and make the equipment size really small, very compact.”
That would ideally result in an easy-to-use and portable modular device into which the recyclable material would be placed.
“In terms of the overall goal for Australia, and even for the world, the one thing we are trying to achieve is a circular economy,” Zhang said.
Solving problems for humanity’s benefit is engineers’ bread and butter. The upcoming Climate Smart Engineering Conference 2024 (CSE24) brings together some of the profession’s best thought leaders to navigate the clean energy transition.