Mechanical and chemical engineers have joined forces to create a fluid-repelling coating that could cut energy bills and emissions from refrigeration systems and other industrial processes.
While water readily forms droplets and drips away from surfaces, fluids used in refrigeration systems are more likely to spread out in an insulating layer of film which can put a damper on energy efficient cooling. This is known as ‘wetting’.
Engineering researchers at Massachusetts Institute of Technology (MIT) in the United States have developed an ultra-thin polymer coating that repels refrigeration fluid and causes it to drip away and allow heat to be transferred more effectively.
The researchers say their coating could also be used to improve the efficiency of other industrial processes including distillation, waste heat recovery, and the production of liquified natural gas (LNG).
Difficult drops
Researchers have spent many years developing surfaces that improve the droplet formation of systems that produce steam, such as cooling systems for coal-fired power stations. But there are relatively few studies that have focused on fluids that have a less powerful attraction between their molecules.
This attraction, known as surface tension, pulls the molecules on the surface of a liquid towards its downstairs neighbours, causing it to form drops. The liquids used in refrigeration have a lower surface tension than water, so form droplets less readily.
According to Mechanical Engineering Professor Kripa Varanasi, getting low-surface-tension liquids to form droplets that drip easily from surfaces has been a “serious challenge” that has affected the energy consumption of processes that use these liquids.
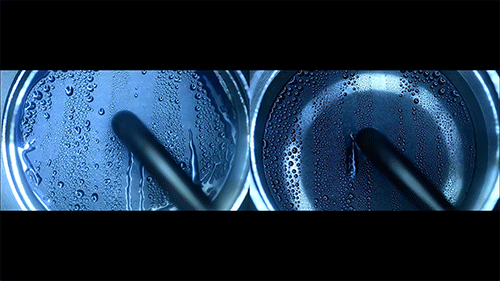
“If it forms a film, it becomes a barrier to heat transfer,” Varanasi said in a media release, adding that heat transfer is improved when droplets form and drip away from a surface such as metal, taking heat with them.
Varanasi’s team cracked the problem by using initiated chemical vapour deposition to depositing a layer of solid polymer less than one micron thick onto surfaces.
The coating repels low-surface-tension fluids as they condense, causing them to form droplets and drip away, making room for more fluid to condense on the surface and continue the cycle.
They improved the performance of the coating by tuning its grafting angle to provide a surface that allows droplets to form and slide off as easily as possible. And to make sure it would work on the shell-and-tube heat exchangers used in oil refineries and chemical plants, the engineers tested their coating on both flat and tubular surfaces,
According to the researchers, the coating could be applied to industrial scale equipment onsite, giving existing plants an efficiency boost. The treatment is also “materials agnostic” – and can be applied to stainless steel, titanium and other metals used in condenser manufacture.
Every little counts
Varanasi estimates that condensation cooling systems that use water can achieve an efficiency of 40 per cent, while low-surface tension fluids halve that efficiency to 20 per cent. As industrial processes using refrigerants and other low-surface-tension fluids are widespread, even a small efficiency gain for each system could add up to a big overall energy saving.
The researchers’ findings, recently published in Joule, stated that the ability of the fluid-repelling coating to promote droplet formation led to heat transfer that was between four and eight times more efficient than that of the uncoated surface.
But because condensation is only one component of the cooling cycle, the overall energy efficiency gain was only around 2 per cent. But the researchers say even this small amount is considered a big achievement.
“In this field, you’re fighting for tenths of a per cent,” said researcher Karim Khalil.