International engineering consultancy Aurecon has delivered the engineering design for Sydney’s new Allianz Stadium, featuring one of Australia’s most complex stadium roofs.
Critical to the construction of the stadium was the project team’s innovative digital workflows, including one based on a ‘single source of truth’ data model for all sub-consultants.
“You could almost call it ‘the bible’ of the project,” says Joe Pirrello, Aurecon’s Technical Director for Allianz Stadium.
Digital engineering
“The way in which we structured and seamlessly shared all of the relevant building information data with many collaborators was one of the most innovative aspects of the project,” says Pirrello.
Historically, different consultants would create their own digital models of the project that they are working on. Architects, structural engineers, shop detailers – all would have their own version of the model.
“Often these models weren’t transferable. And you might find that due to the iterative design process, inconsistencies between the different models start to appear,” says Pirrello.
“We needed to establish a way that we could have a fluid interaction between the architect, the fabric consultant, the services engineers, the fabrication shop detailer and the builder.”
The solution was to establish a single source of truth, initially in order to collaborate with the architect, COX Architecture. But it was a system that operated just as well with the other parties working on the stadium.
Accelerating the process
By sharing parametric data between sub–contractors, instead of whole digital models, changes to the design could be shared much faster.
“The innovation enabled seamless translation of all necessary metadata into any of the modelling softwares used by engineers, architects, builders, fabricators and shop detailers. This saved the project up to six weeks as models could be updated and coordinated within hours, rather than days or weeks,” adds Pirrello.
This also enabled the first roof steel order to occur within three months after commencement of construction, which is significantly faster than traditional delivery approaches.
Computational engineering techniques adopted by the project team enabled the design and detailing of the roof connections to be simplified from 528 connections into only 5 connection types for the entire roof diagrid.
“Our emphasis on buildability was extremely important for a roof of such complexity. We specified the pre-assembly of the roof trusses in the fabrication workshop,” says Pirrello.
“This allowed the fabricator to validate the extremely sensitive geometry, make any adjustments prior to arriving on-site, and improve the speed of assembly and installation on-site,” he continues. “This was critical to ensuring the roof steel was installed without needing site modifications and that the laydown and working areas were used effectively.”
Maintaining architectural vision
Part of the Aurecon team’s task was to maintain the architect’s vision for the stadium, especially the roof.
“We wanted to take a holistic approach to the design and construction,” says Pirrello.
“There’s an architectural intent that drives the aesthetic of the roof shape,” he continues. “But we adjusted and refined the roof shape through our structural form-finding process, significantly improving the performance and ensuring the structure was buildable.”
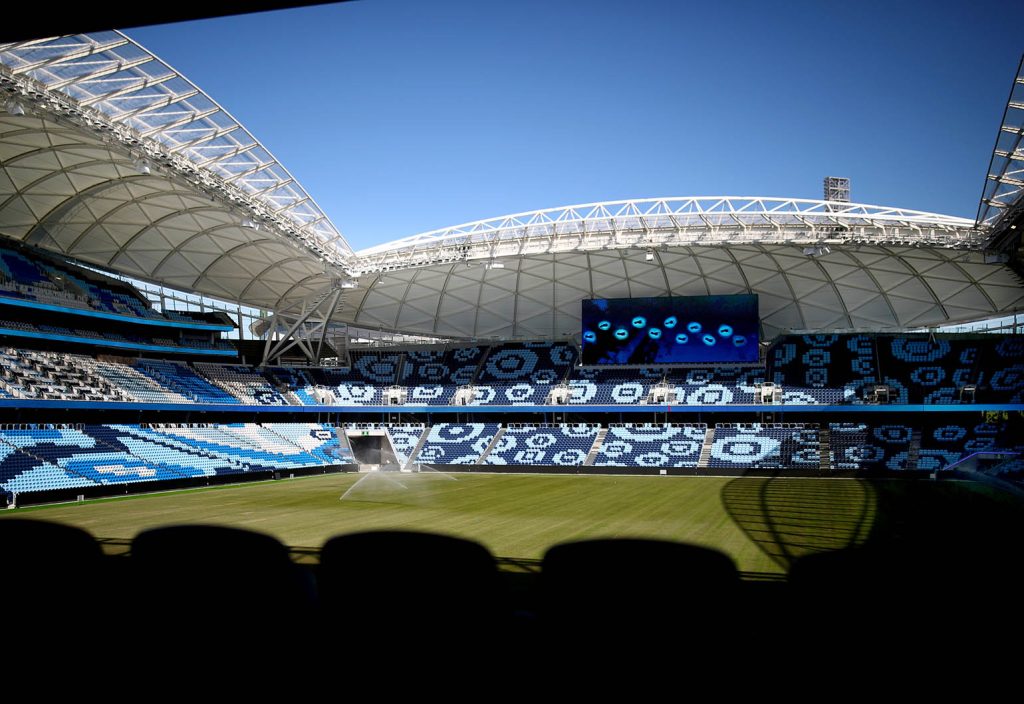
“These changes can then be shared with the architect through the parametric modelling script, and they can transfer them into their digital model.
“So the overall aesthetics are driven by the architect, but the refinement of the shape to make it cost-effective and structurally efficient comes from our structural engineers.”
COVID challenges
The design for the project started in early 2020 – the second week in January, in fact. Of course, not long after that, the world was hit by a global pandemic that changed how the project had to operate.
“Working remotely wasn’t totally new to us, but it definitely wasn’t our preferred way of working for a project like this,” says Pirrello. “Part of what makes a project successful is how you communicate and work together with other consultants as part of the design team.
“And that is much more effective when you’re co-located in a project office. But because we were already accustomed to networking ourselves into a wider business, we knew what we needed to do to overcome those challenges,” he says.
“COVID had an impact on the way we communicated, but it didn’t actually change the way that we transferred files between consultants, or our digital workflows at all,” he adds.
Hidden gems
The crowning achievement of the new stadium is undoubtedly the roof, which uses 40 percent less steel than other traditional stadiums. It contains almost 5,000 individual pieces of steel and was erected in large pre-assembled modules weighing up to 130 tonnes each, which were prepared on the pitch safely and then lifted into place.
However, Pirrello cites some other hidden gems in the design. “The superstructure is actually made up of four separate structures, designed to behave independently. It’s too large to be one structure,” he says.
“So you have a roof that bridges four separate structures, all acting independently, yet all interconnected. When you walk into the stadium you look up at the roof and you’re amazed by its beauty, but knowing that it’s all interrelated is probably something that not many people would notice.”
“It’s definitely not as exciting,” Pirrello continues, “but there are nearly 1500 piles in the substructure.
“We had to go through a very complex process to design those piles extremely quickly, to the point where we had full construction documentation issued within three months of starting the project, which is unheard of for that type of project. And it was because of the critical path nature of the project that we needed to get things out so quickly.”
The stadium officially opened to the public on Sunday 28 August.
For more of the latest engineering news sign up to create’s weekly newsletter.