Sravani Mukkisa is optimising a technology that can give miners and geologists the data they need to make decisions while drilling.
When mechanical engineer Sravani Mukkisa first started working on an innovative new drilling tool, she knew the technology had huge potential for the mining industry.
The prototype equipment, known as DrillMax, could give miners crucial geophysics data in real time, helping them make smart decisions in the field while drilling.
But there was a challenge. The tool was unreliable, consistently breaking down two to three days into drilling.
Mukkisa, an engineering manager at Rig Technologies International, went back to the drawing board. She and her team systematically analysed every failure, bringing the product from proof-of-concept to a commercial reality in a matter of months.
Real-time data
DrillMax is a downhole “geophysics while drilling” tool. It contains instruments that measure natural gamma and take a complete hole survey as drilling is taking place.
The tool also provides information about drilling dynamics, which provide insights into rock strength and density, as well as the nature of discontinuities such as fractures and voids.
Without this live data, Mukkisa says, miners are currently drilling blind.
“You don’t know what you’re drilling in,” she says. “Having that visibility on where you are drilling, what sort of formations you are drilling into, is extremely valuable as we are moving towards sustainable digital transformation in mining. You need data to get to that phase.”
Mukkisa, a finalist in the Chamber of Minerals and Energy Western Australia’s 2022 Women in Resources Awards, says logging while drilling is already prominent in the oil and gas industry. She says 30 years of development has led to advanced surface and downhole tools.
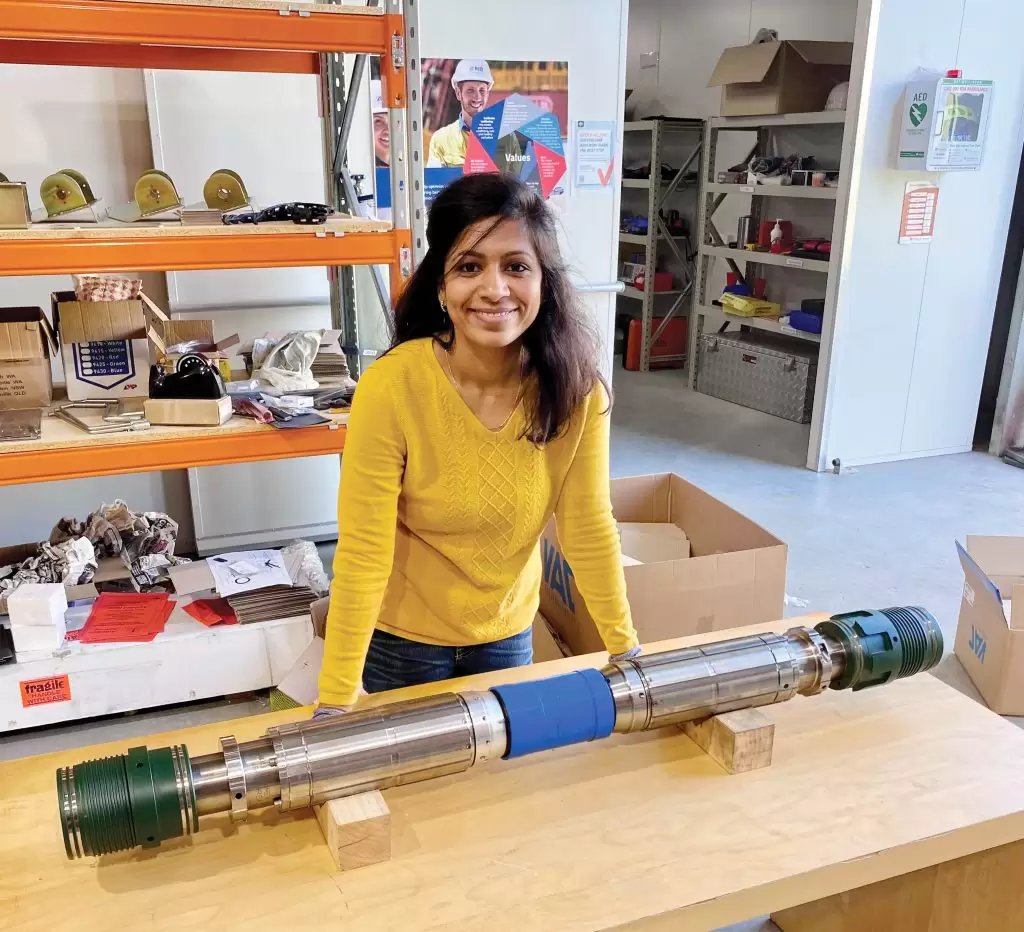
As well as a two-decade head start, Mukkisa says that’s because oil and gas primarily uses rotary drilling systems that don’t see the same level of shocks and severe space constraints as mining percussion drilling.
“The [oil and gas] industry sees a high amount of efficiencies, drilling optimisations, exploration, planning — they benefit quite a bit,” Mukkisa says. “On the other hand, mining is not there yet.”
In mining, Mukkisa says there is growing interest in understanding the ore body during drilling. That’s led to the use of wireline logging — measuring the properties of a formation by lowering instruments into the borehole.
In some cases, samples are collected and sent to labs for further analysis. That means geologists don’t have the information until later.
“They analyse the information after the fact of drilling, not during the drilling,” Mukkisa says. “It’s not right then and there.”
Failure point
When Mukkisa joined the team, the feasibility and proof-of-concept work for DrillMax had already been done. It had an innovative new technology, but it only worked some of the time.
Mukkisa says the tool had to be swapped out every two to three days — it lasted, on average, about 400 m.
“We had multiple points of failure, so it was unreliable,” she says. “Any technology … if it’s not reliable, it’s not sustainable, it’s non-economical, it’s not commercial, then you cannot see the benefits of the technology.”
The engineering team started to look at failure points, collecting data and performing root cause failure analysis. They systematically reviewed every aspect of the tool, making changes to DrillMax’s design, assembly and operating procedures.
“We gathered the data, performed analysis, came up with the plan, iterated and iterated quite significantly fast,” Mukkisa says.
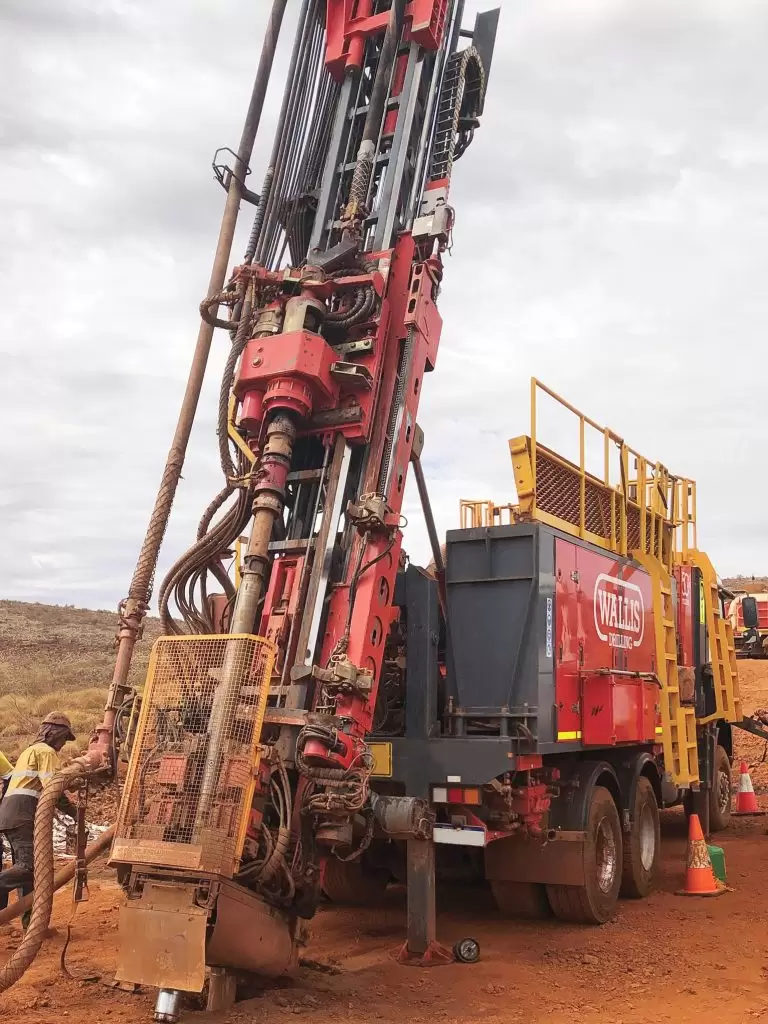
Orica Orebody Intelligence principal research fellow Roger Griffiths says Mukkisa was instrumental in engineering a “quantum leap” in DrillMax’s durability.
“The improvement in DrillMax reliability by more than an order of magnitude under her guidance has extended the service from groundbreakingly innovative to commercially compelling, with significant associated business impact and customer operational efficiency improvements,” he says.
Shock value
Percussion drilling can come with shocks of 2000 G and up. But Mukkisa says the sensitive instrumentation on board wasn’t designed to reliably withstand such a hostile environment.
First, the team had to engineer a damping system that reduced the highest level of shock generated by the hammer. Then, the sub-component systems were designed to further reduce the shocks experienced by sensitive electronics housed inside.
“During the initial phase, the sub-component damping system was not done right,” Mukkisa says. “It was failing inconsistently.
“So we started experimenting with different dampers itself — the materials that can absorb shocks. And also, the system around it, how we are mounting them, and what is the room of flexibility that we can provide.”
Once the damping system was fixed, the team faced its next big challenge: wear. This moved the tool from having inconsistent reliability issues to being limited by the wear rate of the inner tubes.
Mukkisa says DrillMax works with reverse circulation drilling. It’s a method that uses dual-wall drill rods: an outer drill rod and an inner tube.
“You have a cylinder in a cylinder,” Mukkisa says.
Air is pumped through the gap between the two cylinders, and the hollow inner tube allows the drill cuttings to be transported back to the surface. But when the rock samples come through the inner tube, it wears out.
DrillMax is also designed with a dual wall, so miners can still get the drill cuttings, and there are pockets within the tool to accommodate the sensors.
The diameter of the inner tubes matches that of the hammer inner tube, so customers don’t lose the sample rock sizes they’re used to.
Mukkisa says that meant working with really thin sections inside the tube. In early iterations of the tool, the inner tube wore so fast that it would buckle or collapse under pressure within three to four days of use.
“I literally sectioned the inner tube to see the wear pattern and the rate,” Mukkisa says.
Adding to the challenge was that the wear was different depending on the type of formation being drilled.
“Some would wear faster, some would wear slower,” Mukkisa says. “If you’re drilling into granite, it’s different versus drilling into clays.”
Mukkisa then went back to the manufacturing and design process, modifying the design and adding high-strength materials to the part of the inner tube that copped the most wear — right behind the hammer.
Refined product
In the future, Mukkisa hopes to be able to include even more sensors on DrillMax. That includes spectroscopy tools that would allow miners to work out the mineral composition as they drill.
Key to this is the development of live communications, a downhole power generator and reliable inter-tool communications.
“Putting these together … the application is open for all the things that we would do on wireline,” Mukkisa says.
Mukkisa says you can have great technology, but no one will reap the benefits if its performance isn’t economically viable.
“Even a phone — if it’s not reliable enough, you’re not going to buy it,” she says.
For more of the latest engineering news sign up to create’s weekly newsletter.